North American Mining discusses the current state of autonomous mining and its part in unlocking the industry’s future.
by Jonathan Rowland
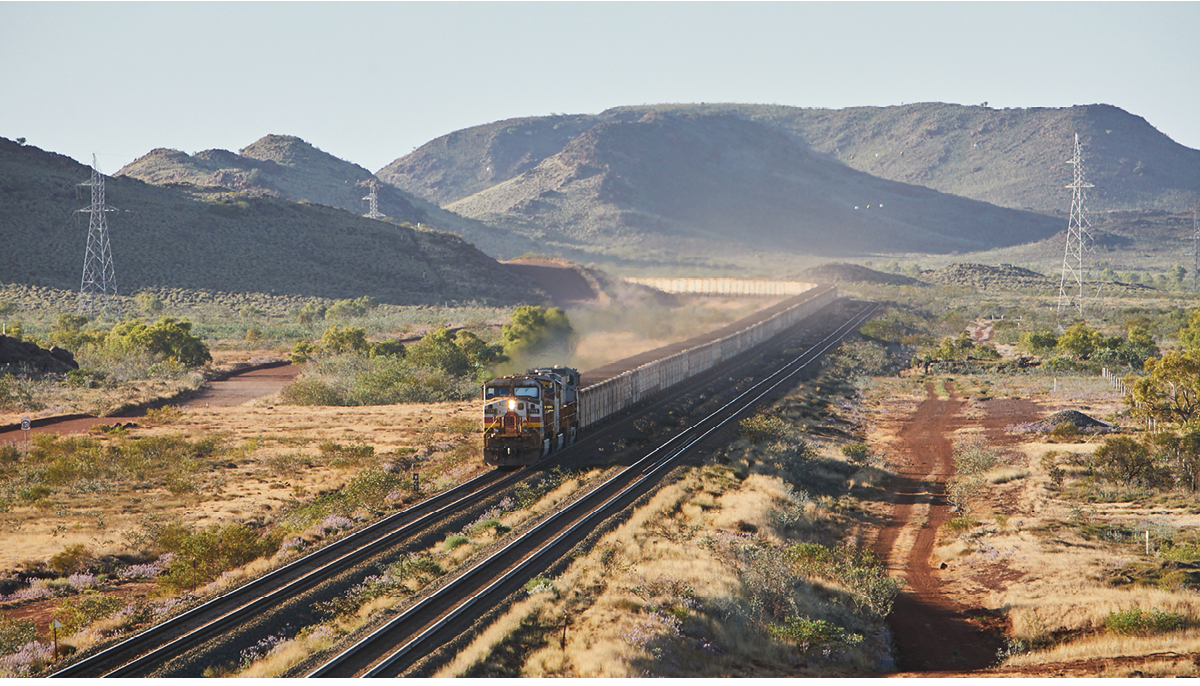
Most – if not all – mining companies recognize the potential benefits of automated and autonomous mining systems for safety, operational efficiency, cost reduction, the ability to work in remote and harsh environments, and the reduction of emissions and waste. Despite the somewhat slow adoption of such systems compared to other industries, mining is now making significant advances with “various degrees of automation and autonomous solutions being integrated into mining operations worldwide,” Prof. Greg Baiden, president of Penguin Automated Systems Inc., mining engineer, and an expert in robotics and intelligent systems, told North American Mining magazine.
According to Sachin Jari, general manager for Mining, North America, at ABB Process Industries, “the majority of mines around the world, including in the U.S., Canada, and Mexico, are automated, in the sense that control systems carry out manual, repetitive tasks and decisions.” But here is where terms can become confused because although ‘automation’ and ‘autonomy’ are often used interchangeably, “they are not the same. I don’t believe any mining company would say they have fully autonomous operations from pit to port.”
The industry has reached the closest point to fully autonomous mining (see Figure 1) in the Pilbara iron ore mining region of Western Australia. Generally, however, “the proliferation of autonomy is limited to haul trucks and production blast drills at top-tier mining companies,” said Dr. Chirag Sathe, chair of the Autonomous Mining Working Group at Global Mining Guidelines Group (GMG).
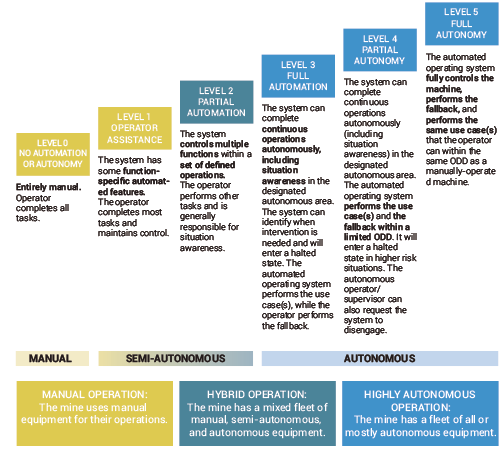
Challenges and considerations
“Implementing an autonomous solution requires significant upfront expenditure in communication infrastructure, equipment, and site preparation,” explained Sathe. “Not many mining companies can afford to spend this capital cost upfront. Autonomous solutions also require specific infrastructure – road networks, communications, data centers, etc. – which takes a couple of years to prepare, while there are long lead times for autonomous truck delivery, which can tie up vital capital funds. Finally, developing an autonomous solution is time-consuming and costly for product developers. This has limited the products available.”
For ABB’s Sachin Jari, however, the “most significant challenge is our mindset and operating culture. Mining remains relatively conservative, so we must consider how people think, design the mine, and operate when discussing autonomy.” Early-stage involvement from all stakeholders is, thus, essential. “An all-electric, fully autonomous mine, with digital systems embedded in the design from the start, looks quite different to a traditional operation using diesel equipment and a human workforce. Sitting the mining company, OEMs, and technology subject matter experts around a table to consider the site and understand what implementing autonomy will take allows for a better result.”
ABB’s contract at Ioneer’s Rhyolite Ridge lithium-boron project (Figure 2) in Nevada exemplifies such a collaborative approach. ABB is delivering process automation, power management, and electrical distribution to the site, but it “all started with joint discussions,” explained Jari. “This allowed us to integrate engineered solutions to drive optimization and digital transformation from the outset. Ultimately, these embedded solutions will allow Ioneer to efficiently and responsibly produce materials necessary for electric vehicles and renewable energy with lower emissions, reduced water usage, and a small surface footprint.”
“Autonomy significantly reshapes mine design, planning, infrastructure, and ultimately the business outcomes, requiring an increased focus on connectivity, efficiency, and data-driven optimization,” agreed Baiden. Digital infrastructure “is particularly critical, with wireless networks at the heart of things. Future terabyte-per-second wireless systems far exceeding 5G capabilities, such as Penguin’s patented Optical Communication System (OCS; Figure 3), will form the central nervous system of the future mine to support the integration of cooperative robotic systems.”
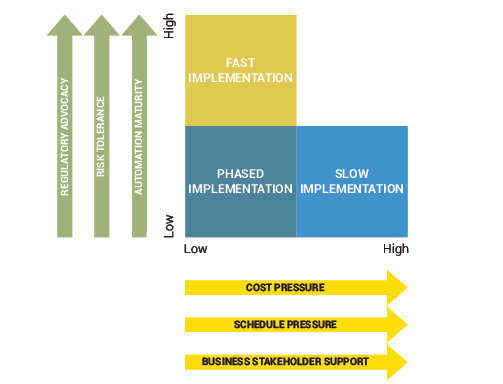
Additional areas of consideration when implementing an autonomous mine include:
- Physical Infrastructure: optimized haul roads and pathways, charging and refueling stations, maintenance hubs and repair bays, geofencing and other safety barriers.
- Operational changes: centralized control centers, predictive maintenance, AI-driven monitoring, AI integration into operational planning, fleet management automation.
- Workforce and training adaptations: reskilling and upskilling the workforce, human-machine interaction (HMI) training, safety and regulatory adaptations.
- Sustainability and environmental considerations.
The role of AI
Mining is “known to be further down the digitalization curve than other industries, which means there’s room to grow and leapfrog in technologies,” said ABB’s Jari. “Data is the key. But, in this industry, gathering it is one thing; using it to empower autonomy is quite another.”
Baiden offered an example of how machine learning and AI can help here. “Several years ago, Penguin was asked to create a robot system to remove hang-ups (Figure 4) as current operating practices placed personnel at risk. The human operator had to be removed from the danger zone for this task to be undertaken safely; however, previous practice relied on the miner judging ‘by eye’ how best to remove the blockage by identifying the keystone.”
To solve this issue, Penguin gathered sensors to process and analyze images of the problem areas with machine learning and AI algorithms to identify the keystone. “With the problem identified, we moved a small drill to the keystone, loaded a charge, and removed it – and thus the hang-up. It might be a small example of how AI and autonomy can be applied to mining to solve production problems and protect lives, but it indicates the greater opportunities available.”
“Humans are not particularly effective at consistency,” added Jari. “In contrast, AI-based digital fleet management systems use data to make consistent and optimized decisions about equipment utilization and workforce orchestration, transforming data into an asset.”
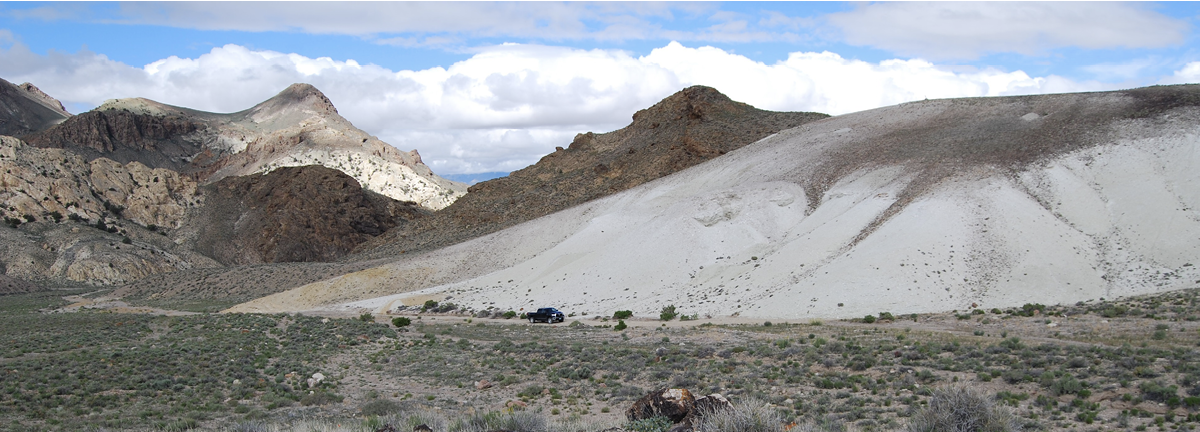
Interoperability and autonomy
Based on current autonomous solutions available in the market, “one of the biggest risks of autonomy is being confined to a particular supplier with limited equipment size options,” noted Sathe. “For example, only certain haul truck classes are currently automated. However, most mining companies will have different-sized fleets from different suppliers. This becomes a major roadblock to implementing an autonomous solution. There have been a couple of new vendor-agnostic suppliers in the market, but their market share is small, and they face a huge uphill task when competing against the major suppliers.”
Interoperability is thus “crucial” to successfully developing and implementing autonomous mining, particularly at existing sites, explained Baiden: “The ability of various systems, machines, and software to work seamlessly together is essential to achieving a wide range of outcomes.”
These include:
- Reduced systems upgrade and maintenance costs
- Operational efficiency and optimization
- Smooth coordination between machines
- Real-time data sharing and analysis
- Safety and risk mitigation
- Harmonized safety protocols
- Consistent HMI
- Scalability and future-proofing
- Adapting to new technologies
- Seamless expansion across sites
A “pressing example” of interoperability’s criticality “comes from the transition to battery-electric vehicles (BEVs),” said ABB’s Jari. “Rapid progress is required here to decarbonize operations in line with global targets. We believe this is best accomplished together rather than in silos. For example, our eMine approach embraces interoperability between infrastructure and electric vehicles along the three interface dimensions: electrical, mechanical, and communication. We are also a founding member of the CharIN Mining Taskforce, tackling the standardization of energy delivery systems for mining haul trucks. This is vital to accelerating the industry’s adoption of BEV technologies, reducing duplication in technology development, and developing a solution applicable to all major applications. Similar initiatives around autonomy would help speed up delivery of a fully autonomous mine.”
Autonomy at brownfield sites
When implementing autonomous solutions, “greenfield sites have the upper hand, as it’s easier to embed new technologies in new mine designs than at brownfield sites, which usually have an operational culture in place. Although this culture can work as a catalyst, in reality, it is often a barrier to innovation. In these cases, we, the technology providers, must take a step back, exercise empathy, and understand the reasons behind a behavior. This human factor is unique to digital solutions, and it can be a company’s best asset or most difficult challenge,” said Jari.
“Brownfield sites also have operational constraints since any new autonomous solutions and related infrastructure should be implemented with minimum (and ideally zero) downtime,” the ABB expert continued. “Lastly, the solution proposed may have to be implemented in phases to reduce upfront costs. The challenge is that the project needs to deliver results from day one to justify investment and reinforce the culture change, as no site manager likes to spend money today to see possible results three to four years down the road.”
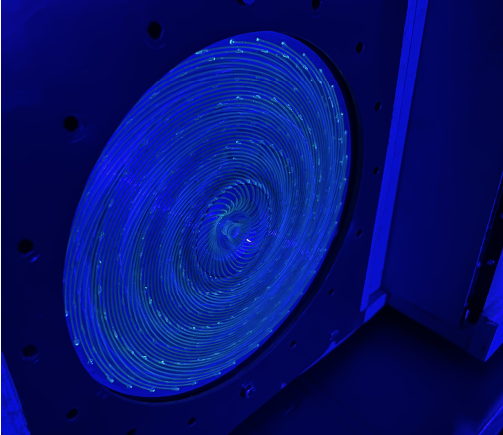
Cybersecurity and regulation
As mines become more reliant on digital infrastructure, AI, and networked systems, “they become more vulnerable to cyber threats,” noted Dr Baiden. It is also true that cyber attackers are increasingly targeting operating technology (OT), costing industrial companies billions of dollars a year.
However, securing OT raises some issues. Industries such as mining often rely on legacy equipment lacking modern security features. Patch and upgrade management can be inconsistent and complicated, particularly when dealing with obsolete systems. At the same time, new regulations are increasing pressure on a small pool of cybersecurity workers, whose services mining companies will have to compete for against other (more fashionable) industries. Yet system resilience – the capability to recover quickly in a cyberattack – is crucial to ensure uninterrupted production.
“Cybersecurity is an often-overlooked, yet critical, component for the success and safety of future autonomous operations,” concluded Baiden. “As the industry moves toward greater autonomy and digital integration, proactive measures in cybersecurity will ensure that mining operations are both efficient and secure.”
The regulation of autonomous mining systems is another aspect to consider. “Regulation is catching up with autonomy; however, only Australian state regulators have developed guidance notes to help mining companies implement autonomous systems,” said Sathe. Identifying the need for a global guideline that covers autonomous mining implementation more generally, GMG’s Guideline for the Implementation of Autonomous Systems in Mining aims to assist those implementing autonomous systems to maximize value while providing a framework to mitigate risks and manage change. Some sections of that guideline are adapted from the Western Australia Code of Safe Autonomous Mining 2015.
The autonomous vision
We are “still in Automation 1.0 mode,” according to Sathe. “We must strive to achieve full autonomy where decisions are taken at the equipment level, by equipment, in coordination with other equipment. This must start in the pit. It is possible to isolate pit operations, so there is almost no interaction between people and equipment. People can operate equipment remotely but not onsite. Once we achieve confidence in operating in such an environment, we can expand into the workshop and refueling. Robots would be expected to perform routine maintenance; robotic refueling should be deployed to remove any people-equipment interaction.”
The future of autonomy in mining “envisions fully automated, intelligent, and sustainable mining operations where AI-driven systems, autonomous equipment, and robotics handle most tasks with minimal human intervention,” said Dr Baiden, picking up and expanding on the theme. “These systems will operate in harsh and remote environments, optimizing resource extraction, reducing operational costs, enhancing worker safety, and minimizing environmental impact.”
Autonomous mining operations will also be “tightly integrated with advanced AI and data analytics, creating a feedback loop where real-time data continuously informs decision-making,” continued Baiden. “Mines will be smart, adaptive, and capable of responding dynamically to changing conditions – whether environmental, operational, or market-driven.”
The steps to achieving this vision include:
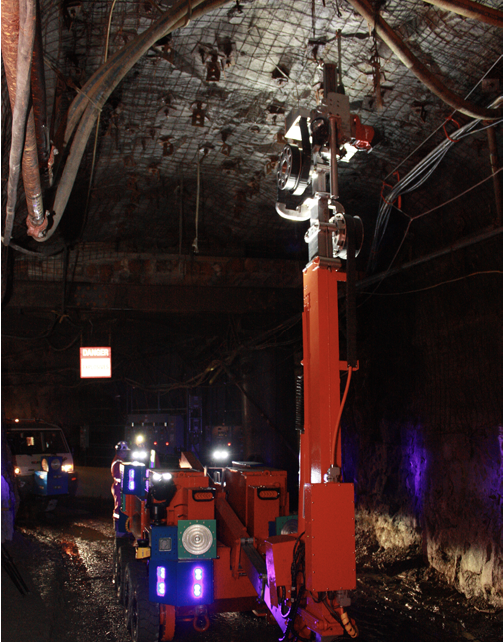
- Investing in R&D for autonomous systems.
- Developing interoperability standards.
- Implementing scalable digital infrastructure.
- Integrating AI and data analytics.
- Workforce reskilling and training.
- Developing regulatory frameworks and safety standards.
- Setting environmental and sustainability targets.
- Undertaking pilot and scale-up projects.
- Focusing on safety and public perception.
Will the industry get there? “I’m a natural optimist, so allow me to paint an optimistic picture,” said ABB’s Jari. “Mining operations have evolved substantially over the last two decades due to technology development, fueled by social pressures for sustainability and safety, as well as financial goals for productivity and profitability where ore bodies are getting deeper and more isolated. As a result, and even with these challenges, we see electric trucks, autonomous mine operations and stockyard management, systems that detect and track people’s location inside the mines, 5G wireless connectivity, and remote operations. The famous ‘digital curve’ chart that presents mining as an old-fashioned industry doesn’t pay it justice anymore.”
Baiden is also optimistic: “The issues touted today, such as high cost, workforce buy-in, and technology integration, are all solvable, especially given the upside. A typical mineral deposit implementing mine-wide autonomous solutions can achieve a near 60% reduction in costs, compounded by mining rate increases and a near elimination of safety issues. Autonomy can thus unlock unprecedented efficiency, safety, and environmental benefits.”
By investing in advanced technologies, building robust digital infrastructure, fostering interoperability and collaboration, and committing to workforce transformation and regulatory alignment, “we can create a mining ecosystem where autonomy is the cornerstone of future success,” continued Baiden.
First to be first?
“We need to stop comparing ourselves to the past,” emphasized Baiden. “We need to reimagine the mine of the future. But, until mining executives are committed to this reimagining, autonomous systems will languish, achieving only a fraction of the results possible.”
In mining, “we love to say ‘we like to be the first second’ as synonymous with wisdom.” In other words, let other industries or customers handle the risk, and I’ll focus on the rewards,” Jari concluded. “I’m afraid this is not how the world works. There are technologies and opportunities available now. We should collaborate now to unlock them.”