By Steve Brewer & Mark Nymeyer, Emerson
This is the second article in a two-part series explaining how innovative valve solutions can be used to improve mining operations. The first article, “How advanced control valves, regulators and relief valves improve mining operations,” covered valve solutions for crushing/grinding/ball mills, digestion/autoclaves, flotation/thickening, and leaching/solvent extraction processes. This article will focus on tailings disposal and water management/chemical makeup, and it includes a section on actuators, along with a use case.
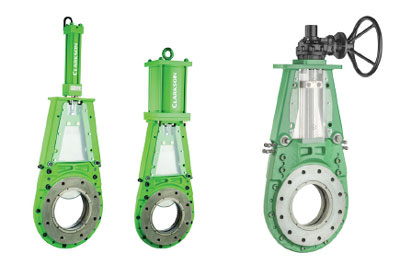
Tailings disposal
One of the more punishing applications in a mine can be found in the tailings disposal network. The movement of large amounts of dense, abrasive material through a very long piping network is never easy, but the problem has been made much worse as mines have removed increasing amounts of water from the tailings slurry as part of their conservation efforts. This makes the resulting slurry even thicker and more difficult to transport.
The natural result of dewatering is significantly elevated pressures at the front end of the disposal piping system, where very large pumps must push the material over long distances (often miles) to reach the disposal area.
All the valves in the system face very abrasive and erosive conditions, but the valves at the head of the network also face very high pressures requiring 300# flange ratings.
The best valves for this service are a range of full-ported, severe service knife gate valves depending on the location in the tailings network. Clarkson KS3 ASME Class 300 Severe Service Knife Gate Valves are very well suited for the head of the network since they carry full 300# flange pressure ratings. As pressures fall, Clarkson KS1 ASME Class 150 Severe Service Knife Gate Valves work well and are cost effective with their 150# flange rating (Figure 1). Both valve designs utilize full port entries, are reversible, and employ wear rings to extend valve life.
In addition, both the KS1 and KS3 have a large, precision-molded seat mounted below the flow stream to provide reliable shutoff, and each has a field adjustable transverse seal to limit leakage outside the valve body. The KS1 and KS3 can be actuated with pneumatic, hydraulic, or electric actuators.
Water management and chemical makeup
In addition to all the mine unit operations discussed above, there are many necessary processes involving utilities, water recovery and management, and chemical makeup. Each of these will need automated isolation valves that provide long service life with minimum maintenance.
Basic water management can be handled using butterfly valves with stainless disks and EPDM seats, such as the Keystone Series GR Butterfly Valve (Figure 2). Chemical makeup valves usually involve more corrosive chemicals, such as caustic or sulfuric acid. In these cases, a resilient seated butterfly valve with PTFE lined body and disc, such as the Keystone Figure 990 Butterfly Valve, is a better choice.
The line sizes for tailings water recovery can be very large. In these applications PTFE-lined butterfly valves, such as those found in the Keystone Series GRF series, can be a good option as they span line sizes from 2-72 inches.
These areas typically include chemical storage tanks that may require nitrogen blanketing and overpressure protection. The focus here is to protect the tank while minimizing nitrogen usage and avoiding tank emissions to the atmosphere. The Fisher brand offers a complete line of tank blanketing regulators suitable for a wide selection of setpoints and flow capacities. Tank vents should be carefully chosen as some models tend to leak significantly near setpoint, increasing emissions. Enardo Enhanced Sealing High-Performance Vent-to-Atmosphere Pressure/Vacuum Relief Valves provide tank venting and can operate up to 90% of setpoint, while keeping leakage less than 0.1 SCFH, making them well suited for this application.
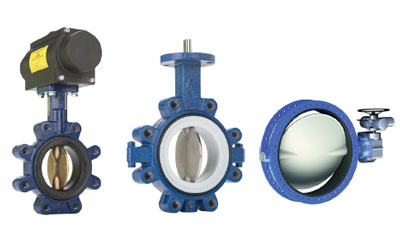
Valve actuators
Historically, most mines have employed a combination of pneumatic actuators around the processing areas, and some manually powered hydraulic actuators in the very remote tailings areas. Electric actuators were less common due to torque limitations and electric power availability. The advent of much more efficient, high torque motors, spring failure options, robust diagnostics, and wireless remote access has greatly changed the suitability and viability of electric actuators (Figure 3). Some mines are also faced with very limited water availability, making it difficult and increasingly expensive to operate an air supply system. As a result, many sites are increasingly utilizing electric actuators.
While pneumatic actuators are still commonly utilized in chemical processing areas where air is usually needed anyway, valves installed on remote tank applications or tailings networks tend to employ advanced electric actuators, such as the Bettis RTS and XTE3000 (Figure 4).
The embedded controls and communication options of these actuators enable remote control and monitoring of far-flung tailings distribution networks even when power is limited. These features also allow advanced control in remote tank applications as described in the use case below.
Use case
A mine uses water trucks for dust control on roads throughout the pit. To reduce travel distance to refill the trucks, the mine decided to repurpose a tank located far away from the processing area. They then needed a way to fill this tank without any external controls because the location lacked wiring or radio telemetry. The main water supply lines were approximately one mile away, with a 300-foot difference in elevation, with the tank being higher than the water lines.
The tank was fitted with a local level transmitter, and a water supply line was run to the tank from the process area. However, the mine needed a means to keep the tank full without running control wires over that same distance. The solution was to mount a Bettis RTS actuator with built in PID functionality on a 10-in. Keystone K-LOK High Performance Butterfly Valve installed on the water feed line at the tank. The level transmitter was wired into the actuator, and a stroke profile was programmed to open the valve when the level dropped too low and close it when the level approached full. This solution resolved the control and communication issues by providing a flow setpoint from the local actuator.
At the other end of the pipe in the process area was a VFD that sensed local pressure in the water line. When pressure fell, the VFD would start and ramp to speed. As the pressure rose above a certain value, the pump stopped.
When the tank required water, the actuator would open the valve, dropping the water header pressure. The VFD would then ramp up to speed, pumping water over a mile into the tank. As the tank filled, the actuator closed off, raising the water header pressure, and eventually tripping the pump. The tank was kept full without running control wires, and the fail-safe electric actuator on the tank’s fill valve protected the tank from overfilling, even during loss of local power.
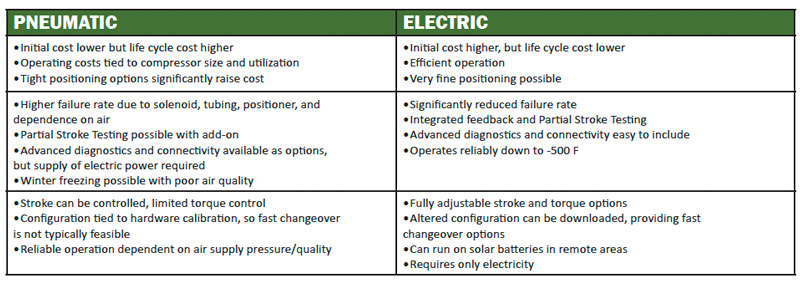
Key takeaways
The best control equipment choices will vary from mine to mine and process to process. However, there are common applications across nearly every mine that can be effectively handled with the right choice of actuated valves, regulators, and relief valves. The major process challenges include:
- Tailings Disposal: Water conservation efforts have greatly reduced the water content of the tailings, resulting in very erosive slurries and elevated pressures at the head of the pumping network. This application now requires severe service knife gate valves with much higher pressure ratings and are better designed to handle the thick, abrasive tailings slurry. Clarkson KS3 knife gate valves have a full 300# flange pressure rating and work well in the high-pressure pumping areas at the head of the tailings distribution network. As pressures fall, the Clarkson KS1 knife gate works well. Both valves are reversible, have wear rings, are fully maintainable, and offer advanced seal designs to provide zero environmental leakage and excellent shutoff.
- Water Management / Chemical Makeup: Water management may involve simple applications but can involve very large line sizes around the tailings water recovery areas. Chemical makeup usually involves concentrated and dilute acid and caustic solutions that can be quite corrosive. For less challenging water applications, valves like the Keystone GR provide reliable service. Larger line sizes may require lined butterfly valves such as the Keystone GRF. Corrosive applications often require a fully-lined butterfly with tight shutoff such as the Keystone F990. Hazardous storage tanks may require blanketing regulators and tank vents. Enardo ES series tank vents can significantly reduce emissions since they can operate at 90% of set pressure yet have minimal leakage. When paired with a properly designed tank blanketing system, the equipment can protect the tank while keeping nitrogen usage and tank emissions low.
Mining processes offer a diverse set of challenges for automated valves and controls. Proper equipment selection requires a full understanding of the difficulties associated with each unit operation, as well as knowledge of the numerous equipment options available to satisfy those needs.
Emerson has extensive experience in a broad range of mining applications and a proven track record of successful installations in many mines worldwide. It also offers a broad selection of control solutions, and the expertise to help mine operations select the right equipment that meets all requirements.
All figures courtesy of Emerson.
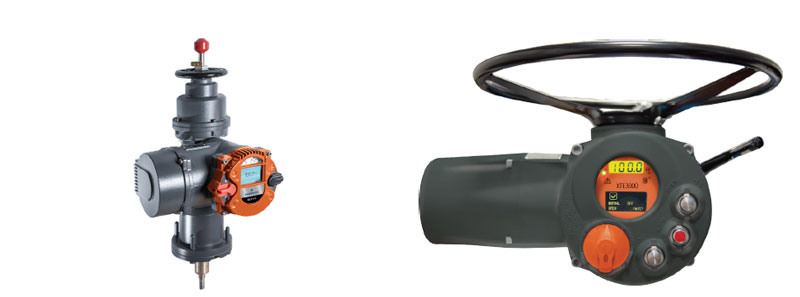
About the Authors
Mark Nymeyer is the hybrid industry manager on the global industry sales team at Emerson for their flow controls products. In his 13 years at Emerson, he also served as the product marketing manager for their Fisher rotary valve and actuator product lines. Nymeyer works at the Emerson Innovation Center in Marshalltown, Iowa. He holds a BS degree in marketing from the University of Iowa and is a Certified Functional Safety Professional.
Steve Brewer is a business development manager at Emerson for their isolation valve group, covering the mining industry in North America. With 23 years of experience at Emerson, he has provided sales leadership in regional and international roles. Brewer holds an MBA degree from The University of Phoenix in Reno, Nevada.