North American Mining asked technology and equipment suppliers for their views on the future of mining and how they are supporting mining companies in achieving that vision.
By Jonathan Rowland
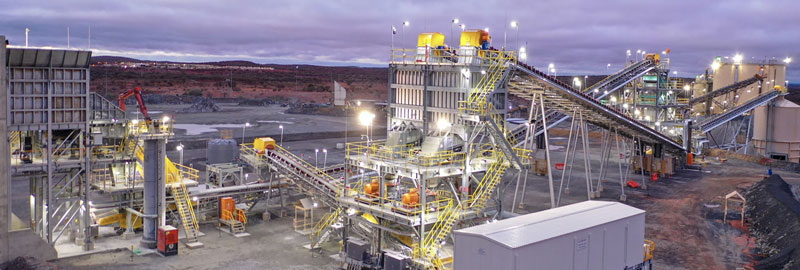
There is “much speculation about the future of mining, especially with the increased demand for greener energies,” said Scott Holub, manager of OTR Technical Services at BKT Tires. However, what does seem clear is that demand for minerals and metals will likely grow. Even unfashionable coal is enjoying a moment in the sun: production reached an all-time high of almost 9 billion tonnes in 2023, according to the International Energy Agency, a 2% increase compared to 2022, as gains in India and China offset declines in the U.S. and Europe. Despite much noise about phasing our coal for power generation, most of that production, some 87%, was steam coal and lignite.
“Despite many countries looking for fossil fuel replacements, coal demand should remain strong,” predicted Holub. But there has also been “an increase in greenfield exploration as countries and companies look to transition to low-carbon economies, electric and hydrogen fleets. This should also increase demand for metals, such as copper and bauxite, used in electrification. The mining of lithium and cobalt, major components in manufacturing batteries for electric vehicles, has greatly increased and should continue to increase in the future.”
“Mineral demand is expected to double by 2050, fueled by economic growth, urbanization, and a rising population. At the same time, the green transition will further drive demand for minerals like copper and lithium,” agreed Lucy England, innovation manager at FLSmidth (FLS). “While recycling will play some role here, mining will still meet most of this demand. Meanwhile, mining is on a sustainability journey of its own. There’s no doubt it’s a challenge. In traditional flowsheets, processing declining ore grades would increase water and energy consumption to deliver even the same output – let alone the increase we expect to be required. This is why we need a new paradigm.”
The future of mining and rock processing is “net zero”, according to Virginia Varela-Eyre, marketing and communications manager, North America, at Sandvik, picking up the potential for a paradigmatic shift in how we think about mining. “The mine of the future will also be created in collaboration with our customers, developing forward-thinking solutions focusing on electrification, automation, and digitalization. Sites will have autonomous and connected solutions, often operated remotely.”
Jeremiah Colling, director of marketing at IWT, also took up the digitalization theme. “The future of mining is set to undergo significant changes in the coming years, primarily driven by the convergence and leverage of data. This transformation will enable more objective and informed decision-making processes. While consumer markets have experienced digital transformation over the past few decades, the mining industry has more slowly adopted these technologies. However, as the industry starts to recognize the value and benefits of these advancements, a flywheel effect will occur and drive adoption.”
One “major change” will be the integration of automation and technology in mining operations, continued Colling.
“This shift will not necessarily eliminate jobs but will change their nature. Many miners fear automation will replace their jobs, but the reality is that their roles will transform to involve different tasks. For example, teleremote operations allow workers to control machines from a safe environment using joysticks. This is a stepping stone towards fully autonomous mining, where machines will operate with minimal human intervention.”
The global mining and aggregates industry is “currently experiencing a challenging reality,” concluded Daniel Biazussi, product manager at Superior Industries, a manufacturer of processing and conveying equipment. “As global demand increases and mines become increasingly complex, companies need to advance control over their processes and implement continuous improvement in operations. Furthermore, mining is one of the most demanding sectors for environmental regulations, safety, good labor practices, and sustainability. Therefore, companies in the area are turning to intelligent solutions in IoT and artificial intelligence (AI) to help them meet regulatory requirements and continue increasing productivity.”
And then there is that ever-present elephant in the mine: cost. “Mining companies have always had to watch their expenses closely to be profitable but, in the last 10-15 years, net profit margins have decreased significantly, causing companies to look for new ways to keep costs down,” noted BKT’s Holub, who tied this back to the move toward digital technologies. “As a result, moving forward, we will see more autonomous vehicles, AI, and mergers and acquisitions to help reduce costs and be more efficient.”
Against this backdrop, how do mining technology and equipment suppliers support miners to adapt to this changing world? North American Mining asked several companies from different areas of the mining and mineral processing flowsheet what they were doing.
BKT Tires
BKT’s Holub began by pointing to the company’s own supply chain. “We started producing carbon black in 2019, and today, 100% of our requirements are met in-house. This guarantees the quality of our supply and reduces the costs and environmental footprint of imports and transport.”
On the product site, with mergers and acquisitions of mines, “many have become larger, making it necessary to run larger equipment,” continued Holub. “BKT has continued to advance larger mining tires to offer mines affordable options. This year, we released our 60/80R57 EARTHMAX SR 53 loader tire and our 50/80R57 EARTHMAX SR 468 haul truck tire. We are developing our 53/80R63 and 59/80R63 haul truck tires for release in 2025.”
FLSmidth
The MissionZero Mine is FLS’s vision for the future of mining and aims to deliver zero-waste and zero-emission mining. “Achieving this will require the evolution of transformative mineral processing flowsheets,” explained the company’s Lucy England. “These will be commodity-specific and encompass technologies to improve energy efficiency, optimize recovery, enhance water stewardship and tailings management, and promote circularity. Some of these solutions already exist, while others will result from incremental, evolutionary – and sometimes revolutionary – innovation.”
England pointed to alternative grinding technologies, such as high-pressure grinding rolls (HPGR), vertical roller mills (VRM), the FLSmidth Tower Mill (FTM), or the company’s Eccentric Roll Crusher (ERC), which “have the potential to reduce energy consumption in certain mineral processing flowsheets compared to traditional grinding methods.” These technologies “may have a particular role as ores get harder and more disseminated, requiring more control over particle size to ensure effective liberation.”
Looking beyond the grinding circuit, “technologies such as bulk and particle ore sorting, the Rail-Running Conveyor (RRC), coarseAIR coarse particle flotation, and the REFLUX Flotation Cell (RFC) could also significantly reduce energy use,” England continued.
Regarding water stewardship, “our solutions focus on improving the effectiveness of water recycling to ensure zero water waste from the process. For example, dry grinding processes, such as HPGR and VRM, mean the water added during post-grinding repulping can be tailored to optimize recovery in the flotation circuit. This compares to traditional flowsheets, where the grinding circuit determines the water content of slurries,” explained the FLS innovation manager.
In addition to reducing energy consumption in the grinding circuit, coarse particle flotation can facilitate faster and more effective dewatering, enabling the adoption of filtered or dry tailings to reduce raw water requirements.
Other dewatering solutions under development by FLS include:
- Advances in the design of high-rate and paste thickeners with the introduction of new rake designs for thickened tailings.
- The AFP2525 tailings filter press, which uses high pressures and low cycle times to achieve significantly larger single- machine capacities.
- EcoTails co-mingled filtered tailings.
- EcoPaste co-mingled paste tailings.
- Smart sensors and advanced process control solutions.
“We are also investing in research to address the issue of chemical build-up in recycled process water, which can impact flotation efficiency,” added England.
“In this area, we already offer MaxR systems and reactor clarifiers to treat acid water and heavy
metals build-up in tailings water streams.”
Mining will also have to look to alternative sources of value. “Tailings are likely to become an essential source of mineral production as mining companies reevaluate what is economically viable to extract,” said England. “We expect to see greater reprocessing of tailings and a sharper focus on co-products in mineral processing flowsheets of the future using our REFLUX CLASSIFIER (RC) and GradePro Classifier.”
England also addressed pyrometallurgical processes for producing critical minerals, particularly lithium. “Our innovative lithium pyro island for spodumene concentrate conversion is the culmination of our most advanced technologies working together and features our state-of-the-art preheaters and coolers. It enables us to extract the maximum amount of lithium from the spodumene concentrate while minimizing energy use. This innovative approach reduces carbon intensity and underpins our commitment to sustainable mining practices and the MissionZero Mine. Meanwhile, our multiple hearth furnace supports circularity in lithium processing (as well as cutting Scope 3 carbon emissions) by enabling lithium producers to recycle the lime used in lithium hydroxide production. Our pyrometallurgical equipment can also run using alternative (non-fossil) biofuels, hydrogen, and electric heating technologies.”
“We firmly believe that the future of mining is cleaner, more nature-positive, and more efficient, with zero emissions and zero waste,” England concluded.
“How individual mines achieve this will vary greatly. There will be many flowsheets of the future, each contributing to a sustainable mining industry that not only provides the world with the minerals it needs to thrive.”
General Kinematics
Looking at today’s market, “we see indicators that demand will continue to grow higher than the rate at which producers can supply,” said Derek Kerkera, director of mining at General Kinematics, picking up themes noted in the earlier discussion. “Of course, and as is typical in a tight supply environment, we see that most material values are also at record highs.”
This is where Kerkera believes General Kinematics can provide mineral processors “a key” to increasing production without causing the need for the capital investment of a new processing facility. “Our Two-Mass vibratory screening equipment can remove bottlenecks, increasing material throughput while maintaining the same or even improving efficiency, all within the same footprint.”
However, that is not the extent of Two-Mass technology capabilities, according to Kerkera. “The technology positively responds to material loading and increases the vibration level, which, in turn, is controlled via a variable frequency drive. This enables the machine to constantly maintain the vibration levels, so throughput and efficiency are maintained regardless of material load changes. The equipment design also spreads out the load from the drive connection to drastically lower the stress transferred into the machine’s body.”
Because of this, equipment life is “increased substantially compared to that of a brute force unit,” concluded Kerkera. “A center spline also cuts the length of the cross members in half, reducing stress and increasing the part life, reducing maintenance needs. Lastly, because of the Two-Mass sub-resonate natural frequency design, the horsepower required to operate the machine is reduced by 4-8 times.”
Putting some numbers on these performance improvements, according to Kerkera, Two-Mass vibratory screens increase screening capacity by up to 40%, improve throughput by up to 30%, and have a service life two to five times longer than that of brute force models, all while reducing energy consumption. “This is why we believe that Two-Mass technology is the future of mining.”
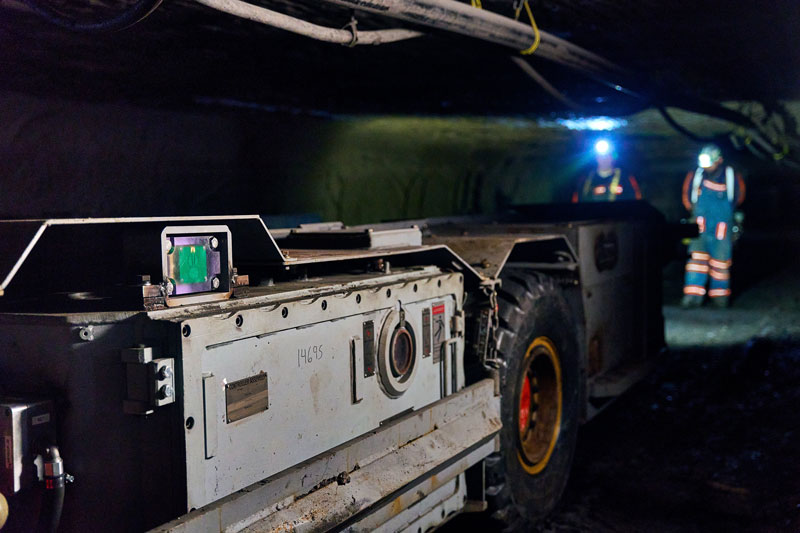
IWT
IWT focuses on developing technologies that enable the transition to fully autonomous mining. For example, the company’s Guardian Proximity System “aims to reduce underground vehicles from collisions with people,” said Director of Marketing Jeremiah Colling. “This is crucial because, despite increased automation, human presence is still necessary for equipment maintenance and other tasks. Ensuring the safety of people around tele-remote or autonomous vehicles is thus a top priority.”
The company is also active in supporting mines with connectivity, visibility, and integration of technologies, Colling continued:
- IWT connectivity solutions facilitate large data transfer from underground to above ground. This high-speed data transfer is essential for enabling autonomous vehicle operations. The company’s radio systems and platforms form the backbone of these systems, ensuring seamless data flow.
- Visibility is another crucial aspect of future mining operations. Traditionally, operators rely heavily on people – shift supervisors and other underground personnel – for
status and information, which can lead to delayed decision- making. IWT analytics platform addresses this by providing real-time visibility into operations. Operators can see the status of vehicles and personnel, make timely decisions, and understand the overall state of the mine. This real-time visibility enhances productivity and safety. - By integrating multiple systems together, IWT enables
mines to simplify maintenance and operation. This is especially important as skilled labor in the mining industry declines. Integrated solutions mean miners do not need to learn and manage several disparate systems, making their work more efficient and effective.
The future of mining will be “characterized by increased use of data, automation, and connectivity,” concluded Colling. “IWT technologies are geared towards facilitating this transition by providing safety, real-time visibility, and integrated solutions. This approach will make mining operations more productive, efficient, and safer in the coming decades.”
McLanahan
“All mining businesses are looking at how they can be more sustainable, implement digital transformation and machine learning, and keep a strong focus on health and safety for our customers and employees,” Lee Hillyer, director of global mining sales at McLanahan, told North American Mining. “These three points are important and interlinked.”
“There is a growing emphasis on reducing environmental impact within the mining industry: how do we do more with less while not impacting the performance, availability, and productivity of the equipment we are supplying,” Hillyer continued. “We are implementing sustainability within our business by refining our whole range of standardized equipment built and optimized over almost 200 years.”
According to Hillyer, standardizing the company’s range of high-quality equipment gives the following advantages:
- Interchangeability and compatibility: Standardizing parts across equipment condenses the supply chain, improving customer lead times and lowering costs.
- Ease of maintenance and repairs: Standardized products improve familiarity, allowing the company to train new employees and customers efficiently.
- Cost efficiency: Bulk purchasing of standardized parts lowers costs and streamlines manufacturing processes, reducing the customer’s costs.
- Improved safety: Standardized equipment has established safety protocols and provides familiarity with equipment operation and maintenance to service teams and customers.
- Enhanced reliability and durability: The company’s equipment undergoes rigorous field testing and quality control, improving reliability and durability. This reliability is crucial in mining operations, where downtime due to equipment failure can be costly.
- Global accessibility: Standardization facilitates global availability of equipment, spares, and support services, reducing customer lead times.
“Our adoption of digital transformation and machine learning is also imperative to the future of mining,” said Hillyer. “Increasing operational efficiency and improving safety are key to sustainability within our equipment and the mining industry. We do this using remote condition monitoring of all equipment sensors, which allows our service teams and customers to monitor the condition of the machines remotely. This helps to increase productivity and cost efficiency. For example, predictive maintenance using condition monitoring can help reduce downtime and avoid unplanned downtime by spotting issues early and avoiding equipment failures before they occur.”
Hillyer’s last point focused on health and safety. “Keeping our employees, customers, and contractors safe is critical and the only way to maintain and grow a sustainable business,” the Mclanahan executive explained. “Safe working conditions attract skilled labor and contribute to workforce retention. Additionally, minimizing accidents and health risks reduces operational disruptions and associated costs, leading to long-term economic sustainability for mining companies. As mentioned previously, our drive towards equipment standardization and digital transformation will ultimately help us achieve our goals of continuously improving the health and well-being of our employees and customers.”
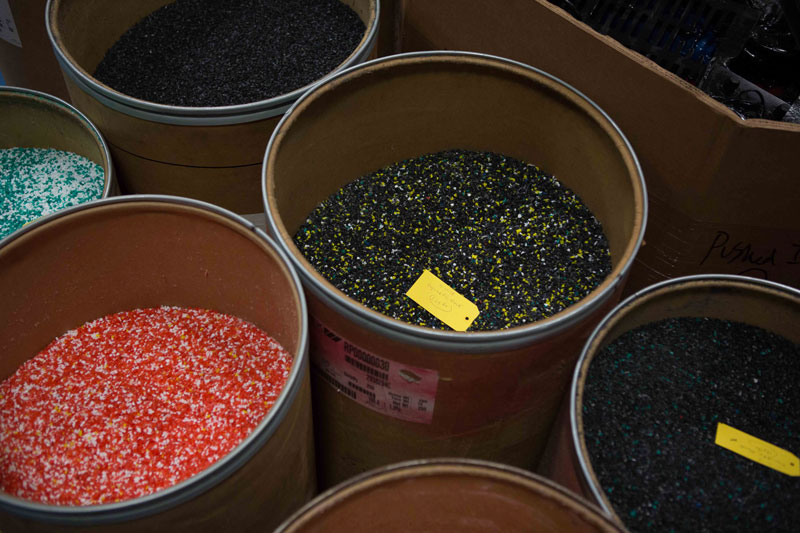
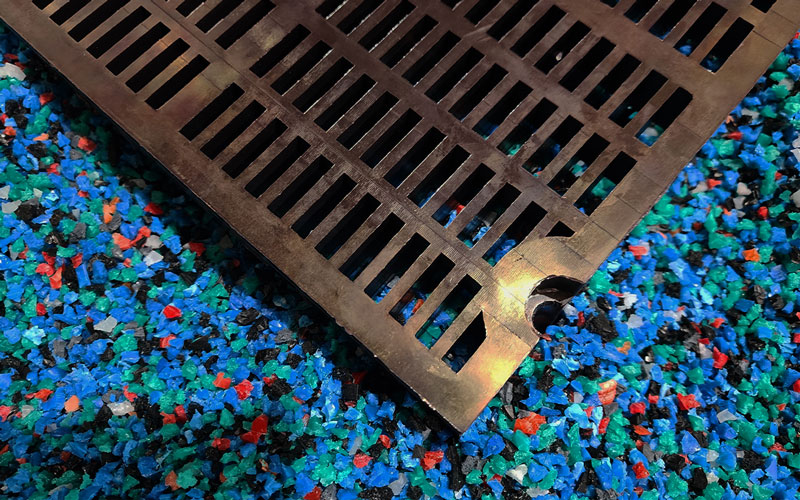
Polydeck
The future of mining “has never been more uncertain when it comes to the technology that is being employed and how it will impact us moving forward,” said Frank Harris, director of mining at Polydeck. “Autonomous vehicles, remote-controlled equipment and systems, and AI are changing how we mine. Polydeck has embraced these technologies and will introduce products that connect to those new systems, providing more information and assistance to decision makers than ever before.”
“The future of mining in America is responding to increasing demand,” added Tom Wayment, regional sales manager. “Polydeck has developed the best method for maintaining screen availability in the industry. With low inventory goals and a focus on reliability, Polydeck is developing new electronic and staffing processes to meet on-time delivery demands.” The company’s materials science in polymers and rubber compounds also “continues to meet mining companies’ needs for predictable production and maintenance processes,” noted John Griffith, Polydeck project manager.
“As Polydeck takes a strategic look at the future, we asked ourselves how we could position ourselves as innovators in an industry that is taking a more serious look at sustainability,” concluded Matthew Freissle, regional business development manager. “We have focused our time and resources on developing sustainable products that are recyclable in a circular economy and will continue to exceed industry expectations. This effort to deliver on sustainability marks us as an environmentally conscious partner in an industry looking for its next big leap forward.”
Sandvik
Expanding on her earlier comments, Sandvik’s Virginia Varela-Eyre continued to describe the company’s mine of the future vision: “We see the future of mining and rock processing as net zero, with equipment forming part of a circular and highly productive value chain, enabling customers to extract maximum value from resources from their mines while minimizing waste and energy intensity.”
According to Varela-Eyre, “all future mining products and operations will be fossil fuel-free, including electric mining equipment powered by onsite renewables. Rock processing technologies will help conserve energy and reduce emissions, providing a sustainable source of critical materials. Mines will be planned and designed to be fully automated and managed using real-time data to optimize operations. Data-driven technologies will automate processes and deliver resource efficiency across the mining value chain. They will enable optimized equipment performance with reduced energy input, smarter decision-making, and enhanced productivity and transparency.”
Extraction processes are also “optimized through highly productive and automated equipment and services while waste is eliminated,”
Varela-Eyre concluded.
“Equipment is built to last using recycled materials wherever possible and is designed for refurbishment, remanufacture, or recycling to enable circularity and material resource efficiency. There will be minimal impact on natural ecosystems, with a reduction of dust and noise. Water use is managed through a closed loop, improving access to clean water for local communities. Closing the circularity gap helps reduce reliance on finite natural resources, and mines are managed at their end of life so that natural ecosystems can regenerate.”
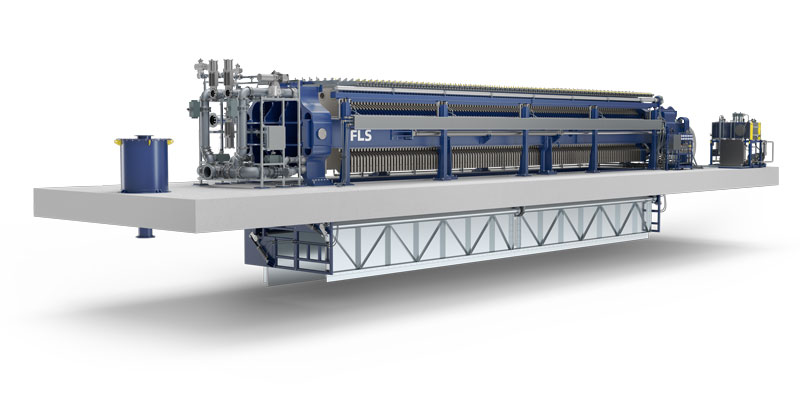
Superior Industries
Today, mining companies “cannot be efficient in predicting belt conveyor roller failures,” said Superior Industries’ Daniel Biazussi, product manager for the company’s Vantage monitoring systems. “When these components lock, the belts continue to work, a situation that can cause wear, holes in the roller housing, and tears in the belts.”
According to Biazussi, inspection is “normally carried out sensitively: operators use hearing, vision, and smell to look for faults in components, especially in the rollers. These detection methods depend on the inspectors’ experience, vision, and hearing acuity. Thermographic measurement is also used, but on a smaller scale than the others mentioned. These investigation procedures are ineffective and put the operation at risk.”
In response, Superior Industries has developed its Vantage monitoring system, which remotely monitors conveyors using intelligent rollers, detecting problems before they occur. “Already being used successfully in South America by iron ore major Vale, the system identifies and collects data, such as bearing temperature, rotation, and vibration, measured by different sensors embedded inside the rollers,” explained Biazussi. “The data can be accessed in real-time to read and monitor operation and working conditions. If there is a critical situation, an alert is issued, which allows action to be taken in advance.”
Vale chose to install the Vantage Rolls at the Brucutu mine in the Brazilian state of Minas Gerais to monitor the load, impact, and return rollers of a drum reclaimer. To date, no fire incidents have been recorded in reclaimer machines. If the temperature becomes too high, an alert is issued to the team, who can quickly identify the defect. If it is found that the roll is at a temperature limit, the person responsible requests the interruption of equipment operation to investigate what happened. If any bearing is damaged, intervention is carried out before the roller reaches a temperature that causes damage.
In addition to its Vantage monitoring system, Superior Industries is “developing deep neural networks (DNN) that can predict machine failures and even optimize process parameters for equipment reliability or production yield,” concluded Bizussi. “Transporters will be the first to receive the technology, using the enormous amount of data generated by smart rollers. Other equipment will come soon.”
TerraSource Global
Picking up on themes mentioned throughout the discussion, Raymond Pietramale, director of marketing and brand management at TerraSource Global, told North American Mining that the company “aims to make processing ore and extracting valuable minerals part of the solution, rather than exacerbating environmental problems.”
This involves “focusing on innovating products with intelligent designs and incorporating smart sensors for real-time monitoring and predictive capabilities. We also emphasize critical spares and wear parts for abrasive and corrosive applications while lowering total installed costs through material science and adopting technologies that enhance operator experience and provide proactive data.”
Van der Graaf
“Conveyor belt drives are the primary source of conveyor costs,” said Alexander Kanaris, president of Van der Graaf (VDG).
“Electricity and maintenance costs increase when dealing with inefficient external motor and gearbox conveyor drives. However, performing routine maintenance requirements, including lubricating or greasing external roller bearings and checking for vibration on these exposed components, impacts worker safety and downtime and increases maintenance and operational costs.”
Addressing these issues, the VDG drum motor is a “totally enclosed, one-component conveyor drive,” Kanaris explained. “All drum motor drive components, including the electric motor and gear reducer, are enclosed and protected inside the drive roller (drum), and the external roller shafts do not rotate. There are no moving parts outside the conveyor frame, and the components inside the drum are bathed in oil for lubrication. The premium-efficiency electric motor is connected in-line to the planetary gear reducer, which is manufactured to AGMA 12/DIN 6 rating and operates at 96% mechanical efficiency, reducing energy consumption and costs. All internal components are designed and manufactured for 80,000 hours of service life before maintenance, reducing operational costs.”
VDG’s GrizzlyDrive Series drum motors are “specifically engineered for mining and aggregate belt conveyor applications,” continued the company president. “GrizzlyDrive drum motors of 75 hp and higher are supplied with the VDG patented oil cooling/conditioning unit as standard. The oil cooling unit circulates and conditions the oil inside the drum for optimal lubrication and heat dissipation, ensuring a cooler-running motor and extending the drive’s life.”
To address lagging delamination, belt tracking, and belt traction issues, VDG developed and patented the IronGrip lagging system. It consists of steel bars welded lengthwise on the drum with hot-bond vulcanized rubber lagging sections between the bars, eliminating lagging delamination and uneven lagging wear. According to Kanaris, “IronGrip lagging improves belt tracking, increases belt traction by 40%, and has a five-times longer service life than standard lagging.”
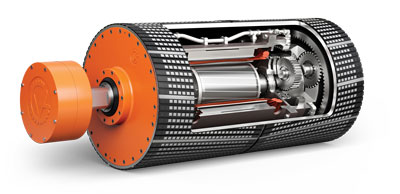
Conclusion
Whether delivering all-encompassing visions for the future of mining or laser-focused solutions that deal with specific challenges, mining technology and equipment suppliers are working hard to help mining companies become cleaner, safer, and more productive. These efforts are much needed if the industry is to successfully supply the robust demand for minerals and metals expected in coming years.
Mining companies face several challenges ahead, which technology and equipment suppliers are helping to overcome with ingenuity and innovation. Photo: IWT.
Innovations in material science can help extend the life of key equipment and meet mining company demands for predictable production and maintenance. Photo: Polydeck.
The recyclability and circularity of parts and equipment, such as screening media, will be a crucial part of the future mining ecosystem. Photo: Polydeck.
Lowering water consumption is a crucial issue for mining companies. Pictured: South32’s Hermosa critical minerals project in southern Arizona recently ordered five AFP2500 filter presses from FLS. These will help the project consume up to 75% less water than other mines in the region.
The recyclability and circularity of parts and equipment, such as screening media, will be a crucial part of the future mining ecosystem. Photo: Polydeck.
Parts will be engineered to run for longer, reducing maintenance and replacement requirements. Pictured: VDG’s GrizzlyDrive™ Series drum motors with patented oil cooling/conditioning unit deliver optimal lubrication and heat dissipation, ensuring a cooler-running motor and extending the drive’s life.