Mining companies are increasingly looking to electrification to reduce carbon emissions. In underground mining, this switch offers several other additional benefits. But making the change at existing operations is not without its challenges.
By Jonathan Rowland
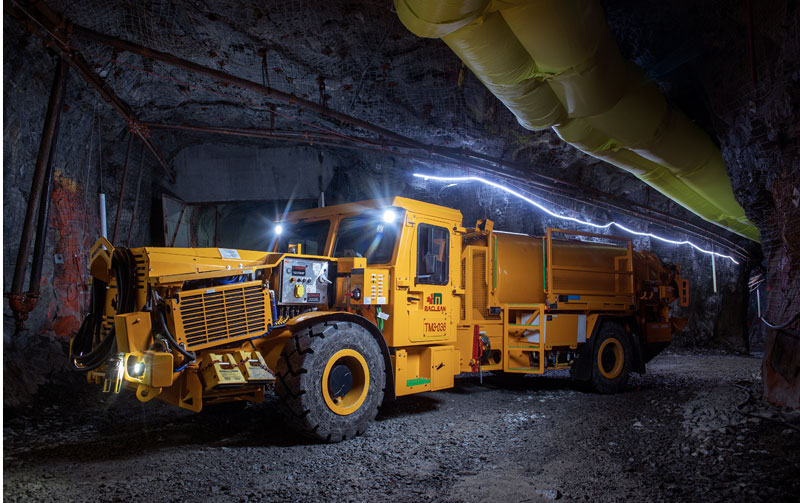
Electrification is nothing new in underground mining. Benefits include an improved work environment, with lower air emissions, heat, and noise, and thus reduced costs associated with ventilation and cooling. Electrification also offers improved energy efficiency.
But perhaps the most significant driver in today’s fast-growing market for electric underground mine solutions is environmental sustainability. When coupled with a renewable energy supply, electrification offers a pathway to zero-carbon mining. In doing so, it supports the industry’s social licence to operate at a time when ESG performance is increasingly relevant to shareholders, investors, local communities and other stakeholders.
Mines that pursue this route also gain an advantage when it comes to energy security, since renewable energy sources are often local and thus not reliant on the globalized market and supply chain associated with fossil fuels. If events of recent years have taught us anything, it is that these are much more fragile than we had previously thought. Re-shoring energy supplies not only assists in mitigating risks associated with climate change and environmental regulation; it may also offer a more secure and stable supply of energy.
One company to have opted for electric vehicles over traditional diesel models is Foran Mining, which is developing the McIlvenna Bay copper-zinc mining project in Saskatchewan, Canada. The company has signed a contract with Sandvik to deliver a fleet of 20 battery-electric vehicles (BEVs), including trucks, loaders and drills. Interestingly, the decision to go electric was made after a pre-feasibility study determined that BEVs would deliver better financial results when taking the consequent savings made in ventilation capital and operating costs. Crucially, the McIlvenna project will be powered by clean hydroelectric power.
Glencore is another to be taking the electric route in its development of the Onaping Depth nickel and copper mine in Ontario, Canada. The company has ordered a full fleet of 23 BEVs from Epiroc, including Scooptram loaders, Minetruck haulers, Boomer face drilling rigs, Boltec and Cabletec rock reinforcement rigs, and Simba production drilling rigs.
“Epiroc scored high on safety, design and testing of the entire battery system,” said Peter Xavier, vice president of Glencore’s Sudbury Integrated Nickel Operations, in a statement announcing the order. “Epiroc also offers large capacity batteries, uses a standard CCS charging protocol, has a battery swap system, and the designs are universal and compatible. In addition, the batteries have integrated cooling systems and safety systems built into the design.”
Located below the existing Craig mine, the $700 million Onaping Depth project will see mining take place at depths where the ambient rock temperature can reach 40°C/104°F. As at McIlvenna, the anticipated savings on ventilation and cooling costs gained by going electric “will be substantial,” according to Glencore.
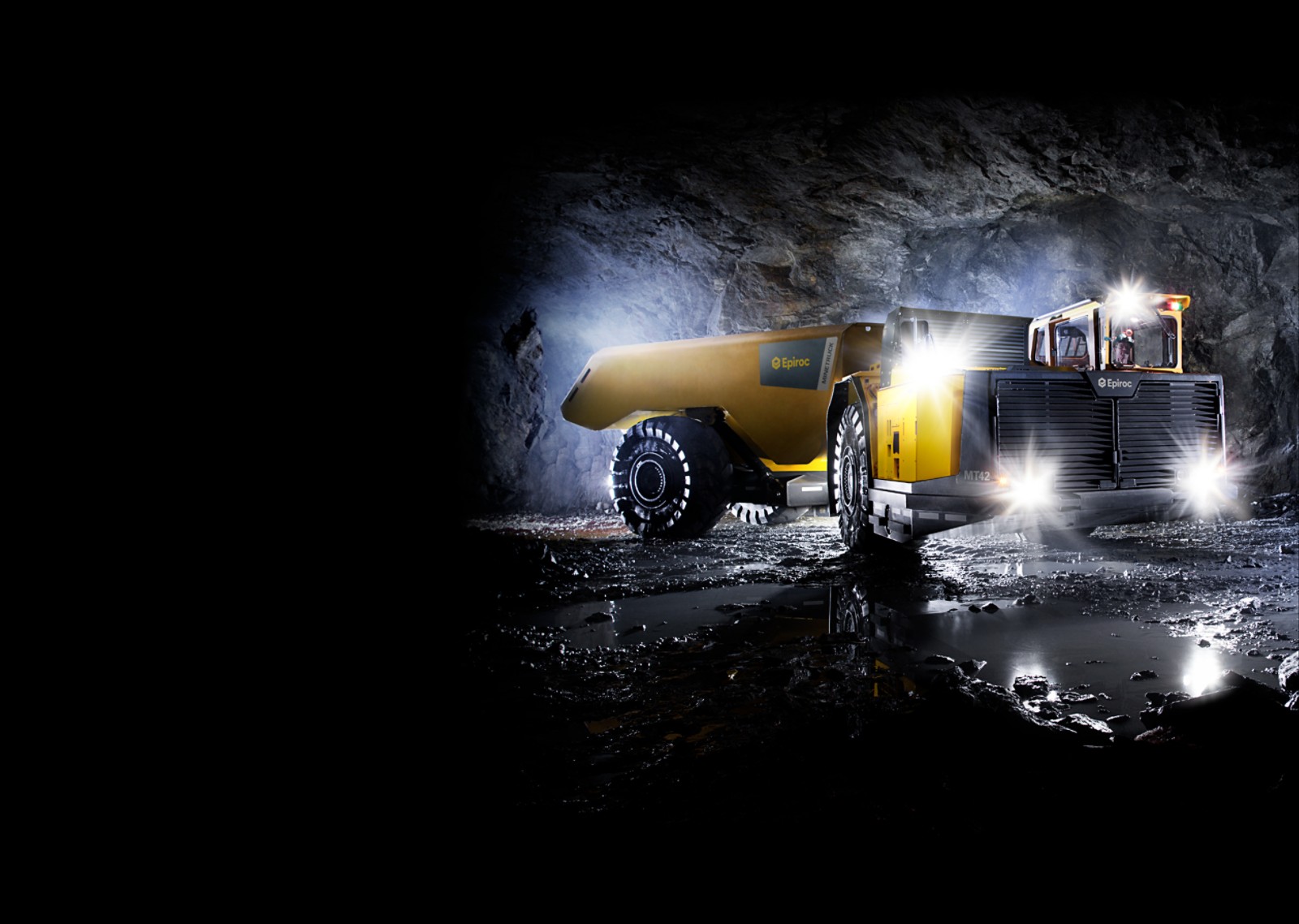
But what about existing mines?
Both Onaping Depth and McIlvenna projects are new developments. Existing underground mines have far less flexibility to adapt to new electric technologies. Bringing the benefits of electrification to these operations is a challenge.
“The all-electric mine demands a completely different environment, layout and infrastructure from a conventional mine design, and this is the challenge of our time,” explained Mehrzad Ashnagaran, global product line manager – Electrification and Composite Plant at ABB. “Successful battery charging and its management – without lengthy operational delays – are core to electrical design for BEV-operated mines. Supporting infrastructure, including all electrical substations, control systems and other assets, must be designed to match to this requirement. But an existing mine is not necessarily ready-made to work with a system that is fully electrified, and all stakeholders must understand this. It can take significant effort in site redesign with operational implications for strategy, scheduling and the skill sets of people involved.”
“There is quite an extensive list of factors and variables that must be considered when switching to electric,” added Anthony Griffiths, senior product manager – Fleet Electrification at MacLean Engineering. “These include required duty cycle, travel distances, grade of ramps, ambient underground temperature, access to the electric grid, price and supply logistics for diesel, and location of the mine. The workforce also needs to be capable of servicing and operating BEV units – so upfront training and preparation is required. There is the question of whether the mine is serviced by a cage or ramp/portal, which will impact duty cycles.”
You must also consider that the energy density of batteries is less than that of diesel – a fact that “cannot be overlooked,” continued Griffiths. “To overcome this challenge, several solutions can be brought to the table. Opportunity charging, fast charging and regenerative energy need to be fully understood and applied to reduce the run time to charge ratio. In our class of vehicles, understanding these three charging options can provide an economical solution or replacement for diesel-powered vehicles.”
MacLean Engineering’s electric vehicle program has been running since 2015. From three original prototypes (all of which are still running), the company now has a fleet of 56 units in operation with another 20 units sold and scheduled to enter service in 2023. “We are really starting to see a spread in the adoption of BEVs,” said Griffiths. “We are also now seeing fleet orders, as opposed to individual orders, as customers see the real benefits and value of BEV units. There has also been a change in attitudes from mining companies. When we started, requests for proposals or quotations were based primarily on diesel, with EV units included as an acceptable alternative. Now customers are asking for BEV only. In only seven years, BEVs has gone from the alternative option to the required option.”
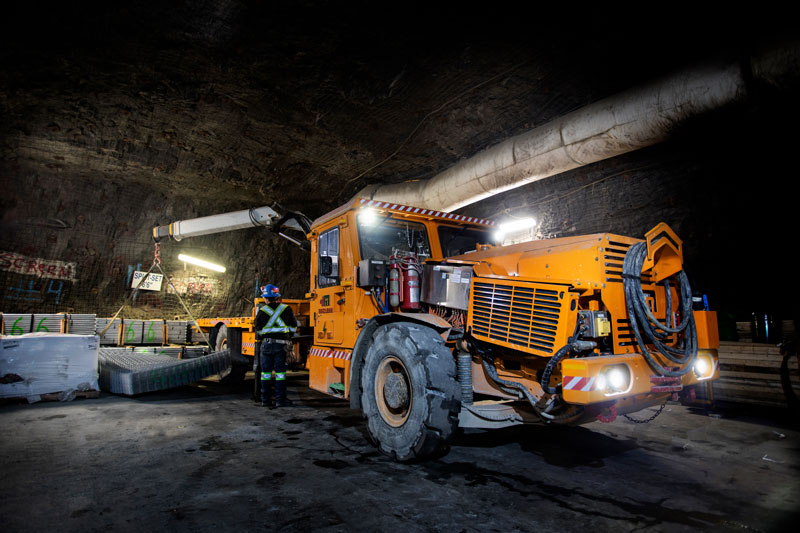
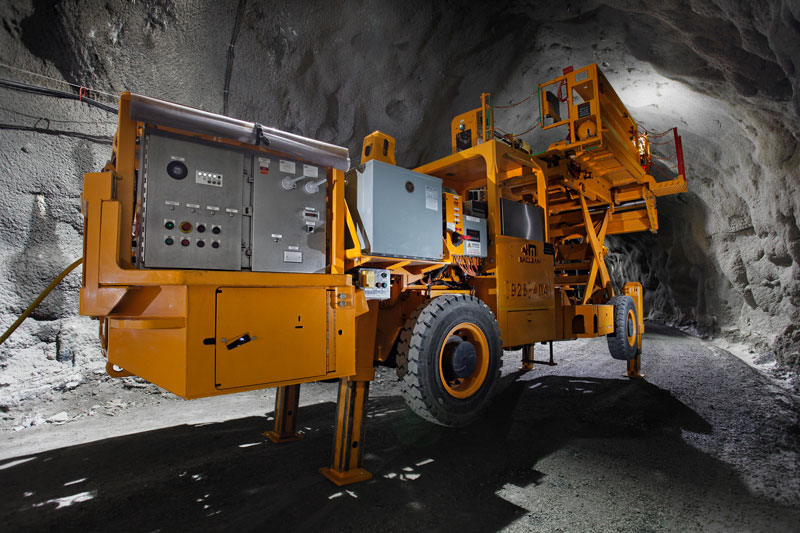
Know the mine
“Brownfield applications may not be able to capitalize on all the benefits of electrification, e.g., if a mine cannot take advantage of a reduction in ventilation requirements for whatever reason,” said Andre Barriault, product and application specialist – Electrification at Epiroc. “There are also certain mine design aspects that are advantageous to BEVs that cannot be implemented after the fact, such as designing stopes and dump points to be able to haul downhill when loaded.”
Despite these caveats, introducing BEVs into an existing operation “can be done relatively smoothly,” Barriault continued. “The most important part is to educate all those involved to alleviate any concerns and apprehension around the introduction of new technology.”
There is also the question of what to do with existing diesel-powered vehicles. Several companies offer rebuild and remanufacturing services to convert diesel or tethered vehicles to BEV. “Transitioning to battery equipment always requires both mechanical and electrical changes,” explained Kenny Boles, vice president of Market Development, at one such company, Saminco. “This includes weight distribution, thermal management, cable/motor access, etc. We also need to understand whether the system will need to go inside an MSHA-approved explosion proof box or is for non-explosive area applications. The first step is learning the production plan of the mine, including machine size, grades encountered, entry width/height, budget, and power infrastructure, etc. From this, we can offer the whole package – from batteries to drives and motors, as well as the labour to install, commission and troubleshoot, and train operators and maintenance personnel.”
Ultimately, implementing the switch to BEVs is about knowing the mine. “Each mining company is at a different stage and the design should be managed holistically for maximum benefits,” concluded ABB’s Ashnagaran. “BEV roll-out strategies need to match up with life-of-mine plans. These in turn need to be considered on the infrastructure side. In brownfields, the challenge is that you cannot design everything from A to Z. You already have existing infrastructure that has not, by default, been designed to consider BEVs. It means electrification of existing mines can be a highly complex process. We therefore foresee any serious large-scale electrification project will need a proper FEED stage to have alignment between the overall mine plan, BEVs and infrastructure design from the beginning of process.”
It is this wholistic approach that has driven recent M&A activity in this area. Notably, Epiroc recently acquired Australia-based JTMEC and Meglab in Canada as Barriault explained. “The acquisitions are very important for us in that they bring knowledge from the power infrastructure, charging and design side. Both suppliers have experience in the infrastructure required for BEVs and have already been working with mine sites on the implementation of digital solutions and BEVs for several years. This experience is valuable for expanding our understanding of how to implement BEVs in the best way possible for our customers. In fact, we are already seeing customers asking for information about a complete BEV solution, and we only see this requirement growing.”
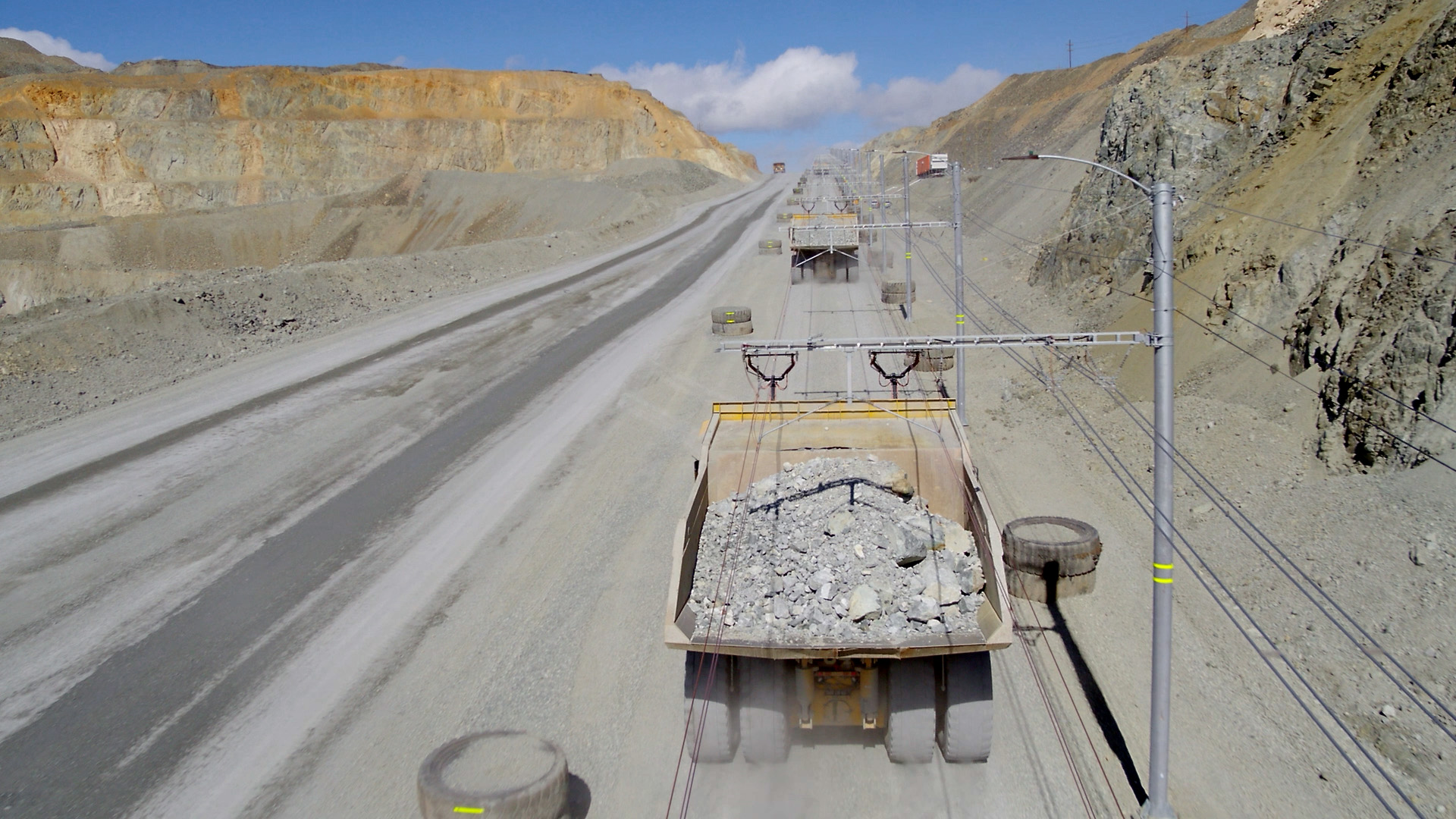
Managing skills in the (rapid) transition
“The BEV sector has emerged quickly and continues to pick up speed,” said Griffiths. “With this, mining companies, equipment OEMs, and suppliers all require a new set of skills. Our approach has been to provide training, both internally and externally, for our staff and customers. But we have also teamed up with a local educational institution Cambrian College in Sudbury, Ontario, to co-develop a training course specifically for those that want or need to develop these skills and experience. This training is not just classroom based; we have an underground test facility where students can develop hands on experience with our BEV product line.”
Epiroc is another company that is working with education institutions to “sharpen the skills of the next generation of technicians,” said Barriault. The company has also developed a Batteries as a Service business model to enable customers to make the leap from diesel to electric. “With this service, we take on the responsibility of battery maintenance and repair, keeping battery availability up. Customers can concentrate on mining, while we ensure the batteries are running as they should.”
Battery safety and supply
Other issues when it comes to the electrification transition relate to the safety and supply of the batteries themselves.
“As with any technology that stores energy, there is always a chance that an event could present itself, and this is not something that we take lightly,” explained Griffiths. “Our approach has been on several different levels, all starting with the design and the selection of components and suppliers. We go through extensive risk and hazard reviews, beginning at the battery cell level right up the entire unit, and the interaction between all components. All our BEVs also come with a battery management system (BMS) and vehicle management system (VMS) options that allow us to monitor and manage every aspect of battery operations, right down the battery cells themselves. This allows us to ‘see’ what is going on inside the vehicle and provides the final piece to our safety process.”
“Whether it is hydrogen gas produced during lead acid charging or potential thermal runaway situations with lithium, strict design measures are used to protect people and property,” agreed Saminco’s Boles. “Our battery management systems (BMS) are also designed to pick up on warning signs from the batteries and to send signals to the vehicle operator of an impending situation. And we spend a significant amount of time engineering weight distribution balance, cooling system efficiency and operator/passenger safety into the layout of the machine.”
“By implementing a safety system with active and passive features at every level, from inside individual cells and at every step out to old fashion robustness, we are confident that the introduction of an Epiroc BEV to an equipment fleet brings lower fire risk than a diesel machine,” said Barriault, who also brought the conversation back to training and education. “That is not to say there are no risks, or that they are the same as those presented with a piece of diesel equipment. The best way to address safety concerns is through education and collaboration. By participating in group discussions, in depth risk assessments or management-of-change discussions, we can alleviate concerns and, more importantly, identify gaps and address them. We believe knowledge is power.”
It is also true that some mining environments pose greater challenges than others: “Getting new products approved by MSHA for coal mines is particularly arduous in time and cost; hard rock mines seem more open to the newer technologies,” noted Boles.
And on battery supply? “The supply chain right now is certainly a challenge, not just for battery or electric vehicle components, but across the whole supply chain,” said Griffiths. “So, the supply of batteries and components could become an issue, based on increasing demand, but all the suppliers we speak with are looking at ways to increase supply and capacity, so it is not an unseen challenge.”
Meanwhile, Epiroc has partnered with European battery supplier, Northvolt, as one of its first customers. “We have worked with them to ensure we will have a steady supply of sustainable batteries for our equipment for the foreseeable future,” said Barriault. The company is also transitioning to becoming a battery pack provider using cells and modules from Northvolt.
For its part, Saminco is betting on versatility, explained Boles: “We have been working with battery-powered mining equipment since 1992, and have supplied thousands of systems to OEM and rebuilders over those past three decades. During that time, we have gained experience working with several types of battery chemistry – lead, sodium-nickel, lithium, etc. Today, using parameters built into our software, we can adjust our drives to various battery systems, with more configurations coming. Even with the supply chain issues, we have been able to source confidently.”
Conclusion
The move to BEVs at existing underground mines raises significant considerations. The technology is advancing quickly, however, and as recent orders are showing, the demand is also there. Knowledge may therefore be the major bottleneck. The skills and experience of companies like those who spoke to North American Mining for this article will therefore be vital. As ABB’s Ashnagaran concluded: “Trusted engineering and technology partners are required in the mining industry and should be involved at the early stages of mine systems upgrade.”
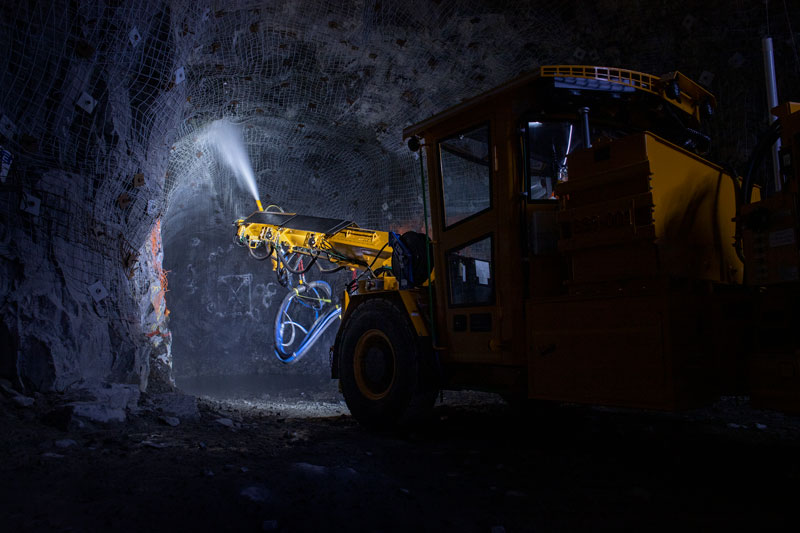