Advanced analytics applications empower operational and business decision-makers to leverage insights and adopt profitable strategies for optimizing mining production.
By Mariana Sandin, Seeq
For decades, decision-making in the mining and mineral processing industry was based on synthesizing raw data from numerous locations, requiring manual aggregation and cleansing efforts in spreadsheets to make sense of process information. This effort is time-consuming at best and risky at worst because of the multimillion-dollar decisions informed by the ensuing analysis, which is often difficult to curate for accuracy.
Far too frequently, these critical analyses are passed up altogether because the preceding manual tasks of gathering, cleaning, stitching together and organizing data are highly complex. And the skilled engineers and analysts in charge of these tasks in the past are becoming scarcer.
To solve these and other issues, the industry is beginning to adopt automated solutions that aggregate, cleanse, and analyze data from disparate sources. Advanced analytics applications provide these capabilities, translating live, raw data into digestible insights for subject matter experts (SMEs) and operators in mining environments. By deploying these tools across their enterprises, mining and mineral processing companies are improving recovery yields while simultaneously increasing operational efficiency by consuming less water and energy.
Layered challenges
Most mines are accustomed to lean operations around the clock, with a small number of highly-experienced engineers to solve complicated issues with minimal capital investment. These teams are also in charge of process optimization efforts, such as improving recovery yield despite lower ore grades. This approach can be sustained so long as the experts remain available, but it is impossible to scale operations beyond a certain limit.
Additionally, retaining experts in the current job market is more challenging than it once was. As employees retire or leave jobs they held for many years, companies are left questioning how to scale process knowledge and maintain productivity.
Adding further to the challenge, firefighting mentalities within many organizations tie up already-limited SME resources, reducing the time left for process optimization. And finally, many of the spreadsheets and data sources these experts use for analysis when they have the time are disjointed and cumbersome to work with (Figure 1).
Bascur, Retamal, & Espinosa, 2023. Treating Low Grades Ores using Digital Twins in Mining and Mineral Processing Plants. https://www.researchgate.net/
Figure 1: A common sight when working with spreadsheets.
The shift to intelligent mining
While most mines today still leverage locally-based control systems and data historians to keep operations on track and manage data, traditional means are increasingly transitioning to new environments, like the cloud. Such a shift enables much easier equipping of industrial internet of things (IIoT) smart sensors to provide improved diagnostics and more transparent asset management.
For example, instead of installing hardwired vibration sensors with the required cabling, battery-powered wireless instruments can be attached to rotating equipment to transmit data for viewing vibration profiles in a dashboard online. Or IIoT-enabled methane sensors can be placed in multiple remote areas to detect emissions and measure greenhouse gases.
Yet, the challenge of converting these raw signals into meaningful information still remains, and the act of cleansing, aligning, and stitching the data together must be performed manually. This procedure is tedious, and it takes away valuable time SMEs could be using to uncover insights. Depending on the complexity of the subsequent analysis, these activities can collectively take days or even weeks.
Fortunately for mining companies, advanced analytics applications can automate these and many other tasks, helping create holistic, intelligent mining systems. These applications combine raw data from various sources, aggregating and cleansing it into optimal formats for analysis and insight generation. Many user-friendly tools go along with these implementations, but the greatest benefit to most organizations is freed-up time for process experts. This empowers SMEs to shift their efforts from manual data wrangling and spreadsheet management, focusing instead on insight review and process optimization.
Leveraging advanced analytics applications
Mining and mineral processing operations can leverage advanced analytics applications to perform many types of analyses – from very basic to highly complex – for transforming raw data into insights. These applications connect disparate data sources to a single cloud-based or on-premises central host, bridging real-time data and empowering SMEs to quickly derive reliable insights across all sources with full contextualization.
With this capability, these applications remove data-access barriers, providing SMEs with point-and-click interfaces for descriptive, diagnostic, predictive and prescriptive analytics. These visual tools enable users to quickly recognize the impact of analyses, identify missteps and successes in real time, model and innovate their operations (Figure 2).
Advanced analytics applications also enable organizations to maximize the effectiveness of SMEs – who may work from different sites – by enabling streamlined collaboration, knowledge capture, and reporting. This facilitates sharing best practices for predicting and preventing common failure modes among assets. These practices can then be shared and scaled across multiple sites and used to train new personnel.
Figure 2: Using Seeq’s visual dashboards, it is easy to spot key performance indicators and their impact on production, such as with this graph, which charts online dynamic particle size distribution versus throughput.
Bascur, Retamal, & Espinosa, 2023. Treating Low Grades Ores using Digital Twins in Mining and Mineral Processing Plants. https://www.researchgate.net/
Results: Maximizing copper recovery with adaptive modeling
Many mines around the world struggle with low ore grades, water scarcity, and variable energy demands. Pursuing mitigation of these and other issues, one South American copper mine deployed Seeq, an advanced analytics application, hoping to discover insights to improve operational efficiency. This mining company had only a small group of engineers, broken up into shifts just to maintain production. Hence, the time for manual data wrangling and analysis was severely limited.
The first step for creating insights was implementing live connections to the numerous areas of the process throughout the mine from the advanced analytics application, providing real-time data so SMEs could easily contextualize information and assemble models. Next, using point-and-click tools, the experts quickly assembled reports and dashboards to increase operational awareness with automatically cleansed and conditioned data.
Equipped with a holistic view of operations, the team ran an analysis of copper recovery and production rate versus particle size and percent of solids in the feed, revealing the ideal particle size, solids percent, and feed rate to maximize recovery (Figure 3). For one particular ore type, the algorithm returned a 200–210-micron particle size at a feed rate of 4200 tons per hour (tph) made up of 67% solids. This analysis was conducted for several ore types and feed rates, and it was augmented with dynamic simulators to create operating envelopes for optimal production.
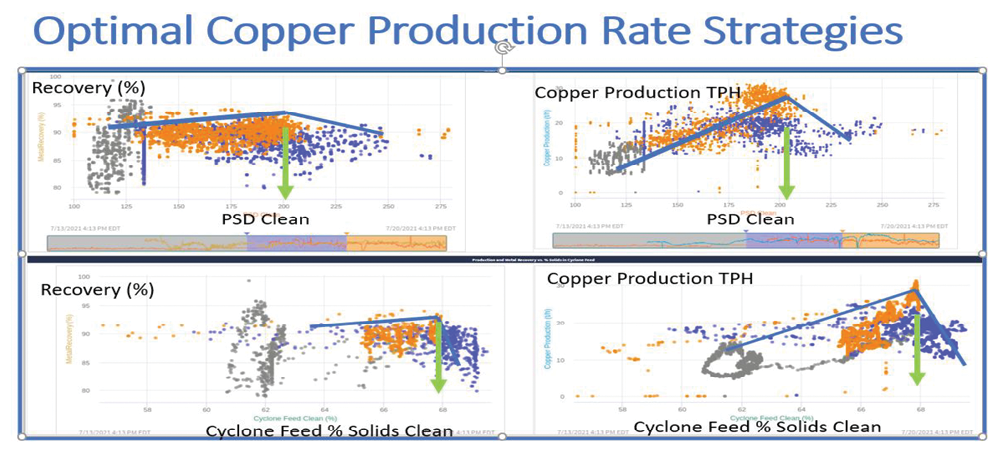
Bascur, Retamal, & Espinosa, 2023. Treating Low Grades Ores using Digital Twins in Mining and Mineral Processing Plants. https://www.researchgate.net/
Next, they superimposed actual water and energy consumption data over the model runs to determine baseline values and begin tracking measures for improvement. These findings, which identified process constraints and hidden losses, were easily summarized in reports and shared with personnel throughout the company, ranging from operators to managers (Figure 4).
Over time, this approach has led to an improved copper recovery rate of more than 4%, along with increased water recovery of 1500 tph in the tailings for diversion to the grinding process.
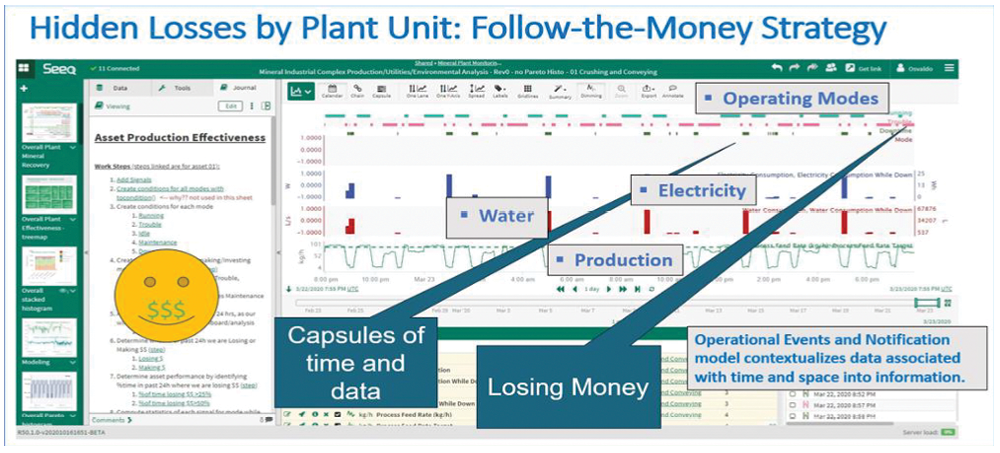
Increasing productivity and efficiency
With innovative tools for collaboration and knowledge sharing throughout an organization, data insights enable teams to increase productivity, remove process and data barriers, and operate more efficiently. Deploying an advanced analytics application pays dividends regardless of where a company is in its digital transformation journey, saving SMEs time, making analyses more reliable, and highlighting areas for process improvements.
These applications cleanse data and create insights, providing SMEs with the tools to investigate a multitude of curiosities, ascertain transformational discoveries, and make informed decisions based on generated insights. These actions can save companies millions of dollars, spare thousands of tons of scarce resources, and increase mining production quantity and quality.
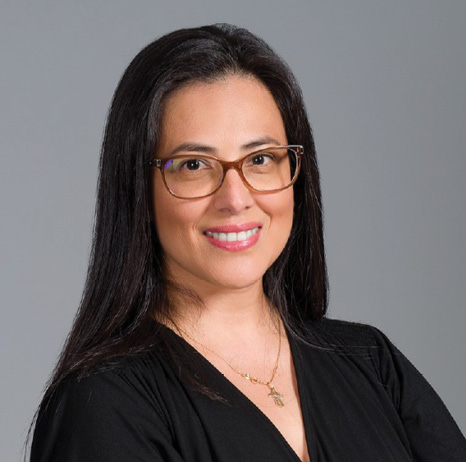
Mariana Sandin has over 15 years of experience in enterprise industrial software and analytics, currently leading the mining, metals and materials practice at Seeq.
About Seeq
Seeq is founded on the premise that many process manufacturing organizations are “Data Rich, Information Poor” (DRIP) and the number will increase with new sensor deployments and higher data creation rates driven by the Industrial Internet of Things (IIoT). Seeq is supported by a broad set of process automation vendor partnerships such as OSIsoft, Honeywell and Siemens, and by system integrator partners for sale licensing and services around the globe.