North American Mining speaks to a number of companies to get their views on how the digital drill and blast ecosphere is developing.
By Jonathan Rowland
As in other areas of the mine, digital technologies are transforming how mines manage their drill and blast operations – with a long list of benefits. In doing so, these technologies are opening up gains through the mining chain. North American Mining asked a number of companies working within this space for their views on how things currently stand, and how they might develop in future. The discussion began with those benefits.
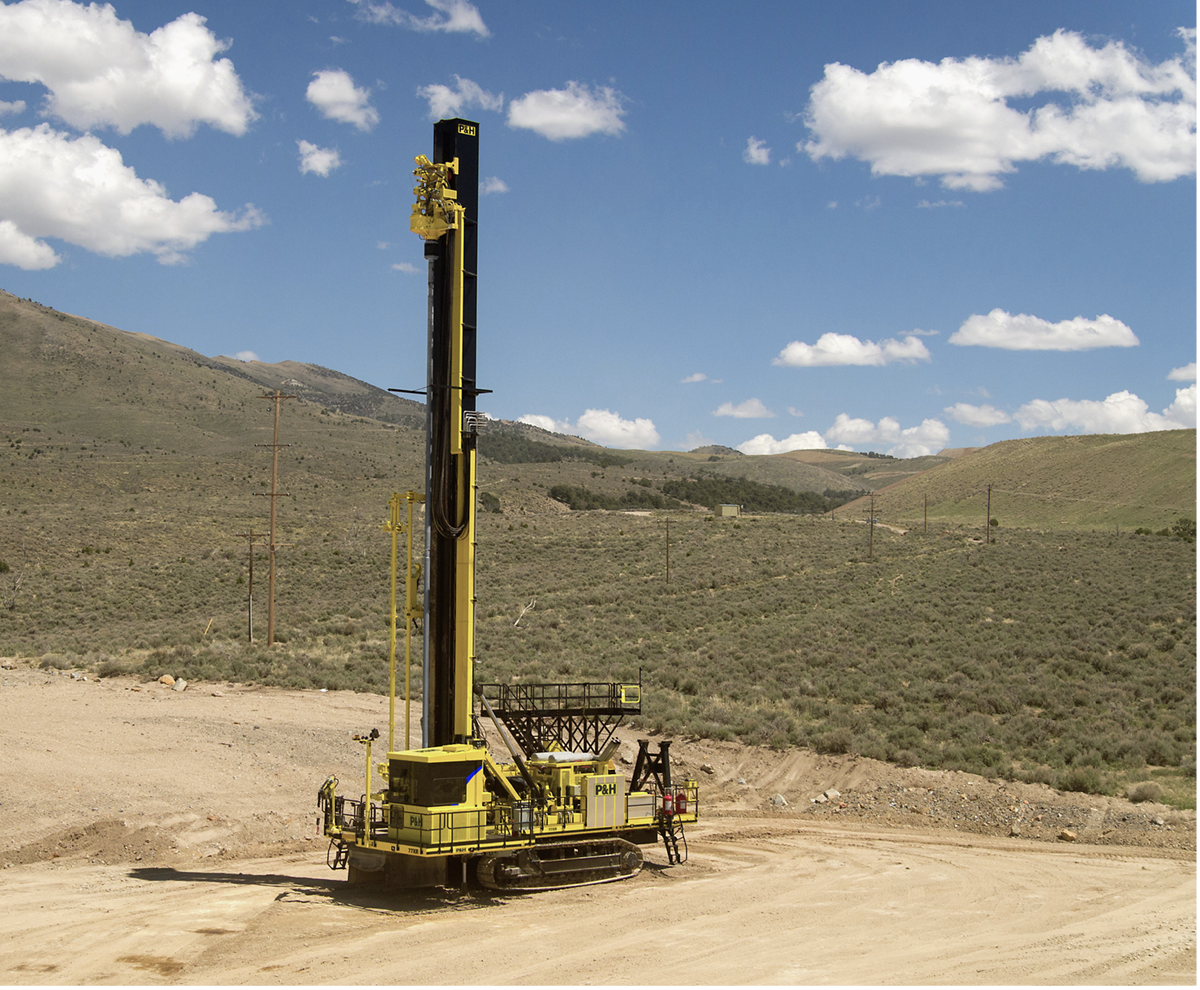
Why automate?
Supporting mine safety is “one of the biggest benefits” of automating drill and blast operations, said Ravi Sahu, founder and CEO of mining AI specialist Strayos. “Automating operations like surveying, marking out holes, drilling, and fragmentation analysis, removes teammates from hazardous situations on the bench or in the pit.”
Or as Wesley Taylor, product manager for automation at Komatsu, summarized: “the automated drill and blast ecosystem allows the drill operator to be relocated off the drill, while maintaining the same level of functionality and accuracy.”
A related benefit is that drilling operations are uncoupled from human factors – for example, the need to periodically relieve operators. Taylor was again succinct in noting that “automated drilling allows operations to continue over shift changes.” Consistency and measurability are also improved when humans are taken out of equation.
As Sahu added, “automation provides much tighter operational control by removing judgement and human error. This helps address issues caused by distraction, exhaustion, even poor penmanship.”
A final point here, this one picked up by James Dampney, vice president of MineMeasure at Hexagon’s mining division, is the ability to compensate for different levels of experience and skill on the part of the blast planners.
“Whatever constitutes optimal drill and blast outcomes – and will vary from mine to mine, it all begins with the plan,” said Dampney. “But drill and blast design is typically carried out by engineers with varying experience, depending on the mine, location, size of operation and company, etc., which can lead to varying outcomes. An automated drill and blast ecosystem can help remove such variation and truly optimize design with outcomes.”
Blast administration and analysis
Another – often overlooked – benefit relates to administrative and analytical efficiency. “By automating recordkeeping, for example via digital drill logs, blast designs and post-blast analyses, data capture is standardized, consistent, accurate, organized and preserved,” explained Sahu. “This data can also be sifted through and analyzed to find insights that traditionally would have required too much effort to uncover.”
“Imagine not having to remember to turn in reports (or wait for them!),” continued the Strayos executive. “Automation can help eliminate some of the dull parts of the job, allowing workers to focus on tasks that make the company money.” This may sound mundane stuff, but it can be a gamechanger – especially at mines who lack the in-house subject matter or business intelligence expertise to regularly deliver effective reports.
Even at mines with good reporting procedures, bringing together all of the data in one place is a powerful tool. In 2021, Maptek collaborated with BMA, an Australian coal mining company, alongside consultants at MEC Mining and data analytics specialists at Insight, to develop the Power BI dashboard for the Cavel Ridge mine in Queensland. The Power BI dashboard provides a “one-stop-shop for all field data reconciliations, reports and comparisons with design,” said Mark Roberts, global product strategy manager at Maptek. “This enables the mine to drive operational and engineering improvements based on past learnings.”
A similar objective is at work behind the HxGN MineMeasure: “no two mines are the same,” explained James Dampney. “The key is enabling customers to integrate their specific drill and blast needs with desired business goals. Our focus now is all around interconnectivity and streamlining customer workflows. Putting the pieces together not only adds value through drill and blast optimization; it also creates a feedback loop that enables the drill and automation that customers are yearning for.”
The age of open data
This brought the discussion around to data, and specifically the need for interoperability and interconnectivity. As Maptek’s Roberts put it: “modern data platforms should help eliminate data/information silos across business units and teams.” It’s a point that was picked up by all of our panel.
“While Hexagon is able to provide all of the necessary technology for a holistic end-to-end drill and blast solution, we recognize that some customers may use technology from other OEMs/OTMs within this space,” said Hexagon’s James Dampney. “This is why we have gone with a platform approach to allow customers to plug in their own data and customize their workflow and analytics to suit their needs.”
Dampney then zoomed out to provide a macro perspective: “It’s also important to note that the drill and blast process touches nearly every other workflow within the mine, from grade control to mining safety, material movement and fleet management through to plant efficiency. We are already working on this interoperability to extrapolate the benefits of automated drill and blast to the entire mine. Customers should expect a lot more autonomy and interoperability on the horizon!”
Integrate, integrate, integrate
Maptek’s Roberts agreed: “Consistent with trends across the mining industry, technologies that integrate across third-party systems are emerging as one of the biggest drivers for improving drill and blast business processes. These solutions help to meet the need for mines to be armed with better systems that support the scale of modern operations and enable increasing coordination across functional departments so the entire mining value chain can be optimized.”
Specific to integration, “Maptek views partnerships between technology providers and OEMS as necessary to deliver an end-to-end digitization solution for drill and blast,” said Roberts. “In this regard, a key focus is exploring how we can expand our integration footprint with like-minded businesses in a way that will maximize value for our mutual customers.”
An example of this is the recording, processing and modeling of measurement-while-drilling (MWD) data so it can reliably and repeatedly be used in routine functions, such as drill and blast, grade control and geotechnical analysis. Another is connecting blast design and reconciliation software with explosives delivery systems, to provide more accurate charge placement for every hole, specific to its current condition.
“We pride ourselves on our data integration ability,” said Strayos CEO, Ravi Sahu, picking up the theme. “In Strayos, you can collect data from drones, smart drills, drill logs, borehole deviation measurement devices, fragmentation cameras, seismographs and a variety of edge devices.
We can also integrate data from OEM/OTM sources. This data is then pooled, analyzed and used to empower and optimize operations, both downstream and upstream.”
“We too understand that the largest part of the value in improving drill and blast operations is improving downstream process,” Sahu continued. “Our platform allows the integration of modules to measure loading performance (e.g., instantaneous dig rates through the muckpile), hauling performance (e.g., truck fuel burn along each haul road) and crusher performance (e.g., throughput rates and power draw) over time.”
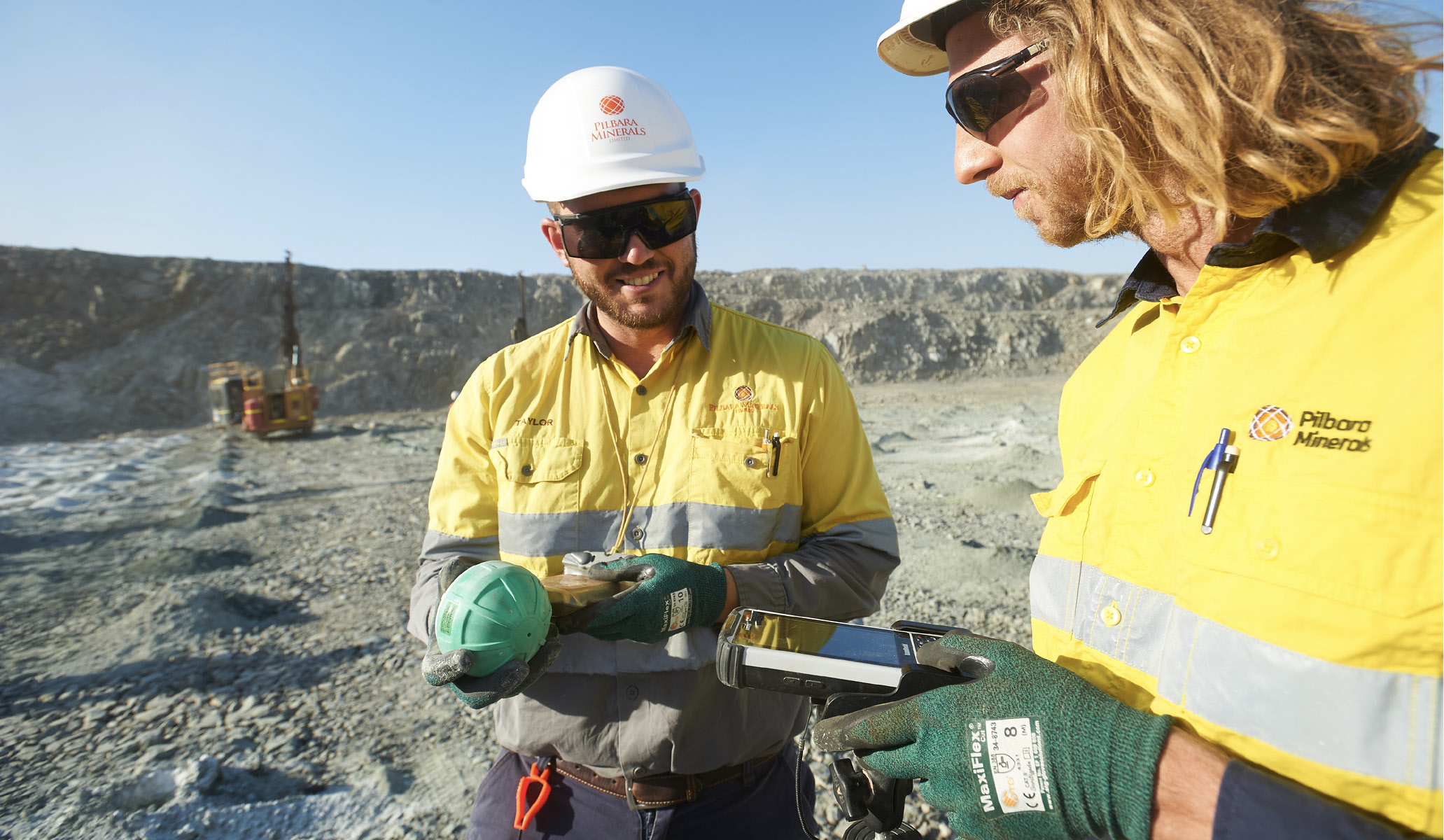
The view of the OEMs
Not to be left out, the equipment manufacturers are also recognizing the need for data integration and interoperability.
“Komatsu drills contain support for an analytics ecosystem,” explained Wesley Taylor of Komatsu. “They give the mine operators access to an open environment, where data captured on the machine can be integrated with and processed by key functions. This includes not only our systems, such as DISPATCH fleet management and ProVision machine guidance, but complementary third-party technologies. Komatsu drill data is also available for other OEM/OTM interfaces for connectivity to other mining ecosystems.”
Caterpillar’s Terrain for drills is another case in point. “Once the blast pattern is designed, it can be uploaded to the machine via Terrain for drills, and then results after drilling sent to the back office,” said Jason H. Anderson, global product marketing consultant at Caterpillar’s Mining Center of Excellence.
Automated drill and blast: a case study
Some of the benefits of digital and automated drill and blast technologies were outlined in a case study provided by Maptek’s Mark Roberts, who explained how “going digital with drill and blast” at Exxaro’s Grootegeluk coal mine in South Africa reduced manual data entry and eliminated data errors, ensuring the mine has access to high-fidelity data with which to identify and pre-empty issues. Initial targets for the project were to improve drill navigation through greater ability to visualize drilling compliance, and integration with smart trucks.
“This has allowed the operation to close the loop on the compliance to plan, reduce dilution and increase recovery, and improve site safety,” explained Roberts, by:
- Enabling drillhole validation in real time to monitor how the as-built holes are complying to design. A direct interface between Maptek’s BlastLogic software and the drill navigation systems allows automated live import of as-built drillhole data for analysis.
- Enabling the flagging of calibration errors and functionality issues on the drill navigation system. In this case, Grootegeluk used it as a trigger to upgrade their drill navigation system: using Epiroc with BlastLogic allows MWD data to be used to quickly derive quality and density information geological and production drilling.
- Providing the mine with better knowledge of the geology. Engineers must take into account geological structures such as faults and dolerite intrusions when planning drill and blast activities. It is therefore important to track variations in coal density across the different benches in the massive deposit. Better data helps Exxaro to mitigate potential dilution and leads to improved safety.
“Major benefits include central record-keeping, drill and charge validation, floor projection and fragmentation prediction,” concluded Roberts.
What lies ahead?
Artificial intelligence
“While the drill and blast process is complex in rapidly changing geological and production environments, we will achieve semi-autonomous blast design in the very near future,” said Hexagon’s James Dampney. “With an appropriate technology stack, and accurate data collection at every step of the process, AI and machine learning will enable an informative feedback loop for pattern design, loading instructions and timing recommendations to achieve optimal outcomes – whatever those may be for a specific customer.”
Some of this is already happening. For example, Strayos uses artificial intelligence (AI) to inform blast design – from optimal burden design to fragmentation prediction, muck pile shape prediction to reduce cycle time for on-site machinery, and vibration and air blast prediction.
“Using historical blast design data, plus-post blast analysis the AI can be trained to site specific performance improvements; for example, how local geology effects fragmentation,” explained Strayos’ Ravi Sahu. “Or to optimize explosive use based on site specific characteristics, such as needing to significantly reduce vibration because the site is close to homes.”
AI is also able to derive insights from much larger data sets. “It can find patterns from sites with similar characteristics that may be owned by different parties,” continued Sahu. “This enables optimization not only at a site level, but also on a macro level; essentially sites can take advantage of best processes from a huge data set that no single company could possibly produce on its own. The AI is trained on data sets to identify patterns, so no customer data is ever shared or made public; the AI just learns that a specific geology coupled with a specific design typically produces a specific fragmentation.”
Automation
Automation of on-bench activities is also already happening with autonomous and remotely-operated drills. But the industry should expect this technology both to expand beyond the major mining sites to smaller operations that have traditionally been less digitally mature, said Sahu, and to a wider set of equipment and processes, said Maptek’s Mark Roberts, including:
- Explosives trucks.
- Wireless initiation systems to enable this for laying boosters and detonators in the holes (priming holes).
- Measuring hole characteristics like changes in depth,
water, and temperature.
Also on the automation front, Maptek has been working on a solution that uses generic algorithms to generate optimized blast designs, which integrate with the company’s current tools for fine adjustment, and reconciliation of implementation and blast performance. “This capability provides an alternative to the traditional, engineering-intensive design tools, and provides options for designs to be performed remotely to the mine operation and incorporated much earlier in the mine planning process,” said Roberts.
For Sahu, the near-term development will be in automating performance improvement processes. “Capturing and analysing data with techniques like drone photogrammetry and fragmentation AI will give engineers a much greater understanding of the impacts of design changes on blast results. Integrating design and performance data into a single platform, such as Strayos, will then also mean that users can instantly identify the best design changes to make without having to do the manual analysis themselves. Automating these performance improvement processes will be a huge quick win for blasting operations.”
Optimizing through multiple constraints
It was left to Komatsu’s Welsey Taylor to sum up the discussion: “The drill and blast ecosystem in the future will allow mine operators to optimize the drill and blast operation over multiple constraints, such as balancing fragmentation, consumable wear or blasting cost. Utilizing data-driven understandings of the constraints gives more visibility and control to optimize more accurately and strike the appropriate balance of potentially opposing requirements.”
Our expert panel
Jason H. Anderson, global product marketing consultant, Mining Center of Excellence at Caterpillar.
James Dampney, vice president MineMeasure at Hexagon’s mining division.
Mark Roberts, global product strategy manager at Maptek.
Ravi Sahu, founder and CEO at Strayos.
Wesley Taylor, product manager – Automation at Komatsu.
The benefits of automated drill and blast
Supporting mine safety:
- Vibration modelling and control.
- Hole quality monitoring and control.
- Accurate blast control.
Improving operational performance:
- Real-time optimization of blast plans.
- The elimination of overdrilling/underdrilling and blasting errors.
- Slope optimization.
- Improved digability and optimized downstream processes (e.g., crushers).
- Integration of drill and blast operations with business goals.
- Optimized use of explosives.
Reducing environmental impact:
- Reduced energy consumption at the mill and downstream ore processing.
- Lower consumption of explosives.
- Optimized rig operations to lower fuel consumptions.
- Increasing resource availability by allowing miners to exploit harder-to- access resources.