Comminution Circuits Are The Single Biggest Energy Consumer At Mines. Improving Energy Efficiency Here Is Therefore A Key Part In Improving The Long-Term Financial And Environmental Sustainability Of The Mining Industry.
By Jonathan Rowland
Sustainability is often presented as a challenge for the mining industry – but there are also significant opportunities. The commitment to reduce global greenhouse gas emissions will require mass electrification of transportation systems, for example, while concurrently decarbonization electricity generation via the use of low- and zero-carbon energy. The mining industry is a key enabler of this transformation, which will entail significant consumption of critical outputs of the mining and mineral processing sectors.1
In particular, the decarbonized economy is going to require copper for electricity transmission; lithium, nickel, graphite and cobalt for electric vehicle and grid-support batteries; aluminum for lightweight electric vehicles components; and rare earths for renewable energy plants such as wind turbines. Iron ore will be required for the steel used to construct new infrastructure and support continued urbanization.
The mining industry must also decarbonize, however, if it is to provide these essential elements in a way that does not undermine global efforts to hit sustainability targets. According to one estimate, the mining industry consumes 12EJ per year of energy – or 3.5% of total final global energy consumption.1 The energy intensity of mining is also predicted to increase over time as deposits that are lower quality, deeper and more difficult to extract are mined.
Various routes are available to the mining industry to reduce its energy consumption: Industry 4.0 technologies offer opportunities to control and optimize processes as never before. Of high priority, however, are systems that focus on comminution circuits.
These are typically the single biggest user of electricity at a mine site, accounting for anywhere from 25% to more than 50% of consumption. 1,2 Indeed, comminution in the mining industry may account for 1% to 3% of total final global energy consumption;1,2 in countries where mining accounts for a significant proportion of economic activity, this number is higher.3
Small reductions in the consumption of energy for comminution can therefore have a big impact in overall site energy consumption. Indeed, innovation to reduce energy consumption in comminution is considered significant enough to be the focus of Natural Resources Canada’s Crush It! Challenge, which boasts a top prize of CA$5 million for the team that demonstrates the best energy breakthrough in crushing and grinding. The competition is currently down to six finalists with a winner expected to be announced this summer (Table 1).
More efficient comminution also offers mining companies opportunities to reduce costs and improve overall mine site productivity, providing an economic case for investment in upgrades and new equipment.
Time for Some Joined-Up Thinking
One of the key factors that influences the efficiency and energy consumption of the comminution circuit is the material fed into it. Linking data gained from geological modelling, mine planning and processing plant operations offers the opportunity to track actual flows of ore from extraction to delivery to the processing plant, including data on ore concentration and composition. This creates the opportunity to automate blending to provide the optimum feed to the plant, allowing it to run at peak productivity.
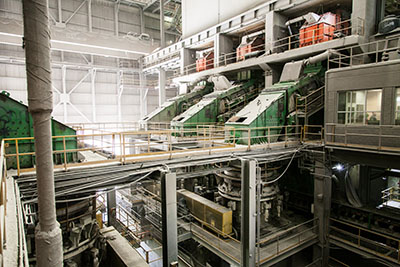
“Consider the flow that an ore body makes through the mine,” said 3ag Systems. “Based on the density of the rock being blasted, the drilling pattern, and a whole host of other factors, there will be a range of rock sizes included in the run of mine (ROM) ore […] The varying proportions of ROM ore sizes and their associated densities create challenges, as the dynamic nature of the ore characteristics has a direct impact on the amount of time each piece of ore spends in each stage of the comminution circuit. In other words, with each new load of ore entering the system, there is a new ‘optimal’ configuration of machine settings for the entire circuit that minimizes energy consumption and maximizes throughput.”⁴
But as 3ag points out, at most mines, blasting, crushing, grinding and maintenance all work independently of each other to achieve their targets and KPIs – a less than ideal situation in a such a dynamic and interrelated operation as a mine. Here lies a big opportunity for improvement.
If “the geological block model can be linked to the mine plan and ultimately a real-time model of the processing plant, which can then be imported to an advanced control system and used to set the control parameters and set points for the plant,” argued engeco in a recent report on energy consumption in mining, “the operation as a whole can be optimised to achieve a set of objectives [with] AI and machine learning […] deployed to enable decision making, or at least decision suggestions, to be made automatically.”⁵
The impact of more data-empowered decision making was seen at Freeport-McMoRan’s copper mine in Arizona, where AI modelling of grinding circuit operations has helped to improve mill productivity by an estimated 20 million lb. per year – an increase that has allowed the company to avoid most of planned $200 million capital expansion.⁶
Blast Smart
Smarter blasting is also an important part of joined-up thinking from mine to mill: increasing rock fragmentation during blasting is generally a less energy-intensive method of size reduction than comminution, although it is partly offset by an increase in explosives cost.
“Chemical energy is cheap as opposed to electrical energy,” explained Suzanne Lynch-Watson, manager of process optimization, performance solutions, at Metso Outotec. “If you can design a blast pattern that maximizes the use of cheap chemical energy in a safe manner, you will have a significant impact on the electrical energy required to complete the size reduction process. Metso has numerous case studies in which changes in drill and blast designs have led to increases in downstream throughput by 5%-20%.”⁷
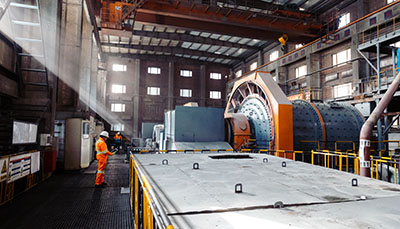
Generally, this will entail generating more fines during blasting, as increasing SAG mill throughput “generally requires feeding it with more fines,” continued Lynch-Watson. “If these can be generated in the blast, then it is a much more cost-effective way of achieving a higher SAG throughput. Generally, the biggest benefits, 10-20% increase in throughput, are seen in the hardest ore.”
Neville Judd of Hexagon agreed: “A correct blast not only optimizes the cost of that blast, it improves the total cost profile of the entire mine. Correct fragmentation means easier digging, reduced shovel cycle times, reduced rework, less oversize causing downtime at the crusher, lower-cost crushing, and improved tons per hour through the processing plant.”⁸
To achieve these benefits, a holistic approach to drill and blast operations is required that includes solutions to improve yield, fragmentation and dilution. “Incorporating technology ranging from blast design and high-precision drilling to post-blast analysis and optimization, also empowers mines to take back the purchasing power on their bulk commodity explosives,” concluded Judd.
Preconcentration Enters the Mix
Focus on preconcentration of ore before it is fed into the comminution circuit is also growing. The argument is simple, as Metso Outotec’s Lynch-Watson succinctly noted: “Rejecting waste rock early is the most direct way to reduce comminution cost. When done properly, preconcentration can actually increase recovery, leading to a real win-win scenario: less power consumption and more metal production.”
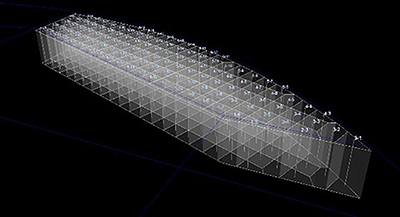
It’s also not a new idea: solutions such as gravity separation, dense media separation, flash flotation and screening are all methods of precontraction. More recent developments include sensor-based ore sorting, such as optical sorting and x-ray sorting. “Conceptually, preconcentration has been used for some time, but concerns around energy consumption/GHG emissions, water use and tailings volumes has renewed interest in this area,” noted the engeco report.⁵
Rejecting waste before it is more finely ground also improves the safety of waste disposal, as “coarser waste material is much less risky to dispose of than the fine particles that make up a normal tails stream in a processing plant.”⁵
A Focus on Equipment
In the comminution circuit itself, advances in new grinding technologies offer further opportunities to reduce energy consumption.
“Advancements in high pressure grinding rolls (HPGR), high intensity grinding and stirred mills/vertical mills mean that traditional semi-autogenous grinding/ball mill circuits could be replaced and the same outcomes achieved – subject to the amenability of the particular ore type and processing requirements,” argued the engeco report. “New grinding technology can, in some instances, be significantly more energy efficient than traditional comminution circuits.”
This is particularly true when dealing with highly competent ores, such as gold, as SAG mills do not process competent rocks particularly well. “Gold is one of the toughest ores out there,” explained Bjorn Dierx, global product manager Enduron HPGR at Weir, requiring “substantial time in grinding mills to produce a suitable particle size for mineral liberation, leading to high consumption of the mill’s liners and grinding media.”9
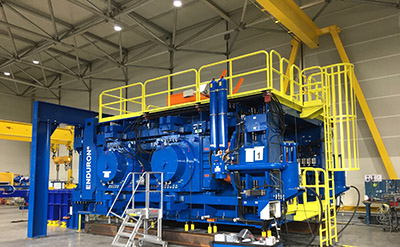
In contrast, “the inter-particle compression of a HPGR is highly effective at reducing competent ores when deployed for tertiary comminution, significantly increases the throughput of downstream mills while reducing the circuit’s overall energy consumption by up to 40%.” As miners excavate deeper ore bodies with higher competency, such benefits will become increasingly important.
“In my early experiences working with gold mines across Australia, the average Bond Work Index I encountered was probably 17 or 18 kWh/t,” concluded Dierx, “but we’re now seeing numerous projects utilising ore with an index of 22-24 kWh/t. As the energy required to reduce each tonne increases, HPGR offers miners an effective way to increase production, while keeping energy costs under control to maintain profitability.”
Another option to help improve comminution efficiency is in-pit crushing and conveying. The advantage here is found in the transportation of ore between mine face and crusher. “Conveyors are more energy efficient that trucks,” explained Metso Outotec’s Lynch-Watson and Alan Boylston, director, process engineering development, sales.10
“Combining mobile and semi-mobile packages and coarse ore sorting – for example by rejecting waste rock after secondary crushing in the pit – can be a game changer. Not only is there a benefit in terms of reduced energy consumption in the mills, but the cost to convey material out of the pit also goes down proportionally to the amount of material rejected. It’s simply a matter of looking at it holistically.”
Boylston and Lynch-Watson cite the example of lifting 1 metric tonne of ore up 100 m. With a truck, you are also required to lift the mass of the haul truck, whereas a conveyor is continuous, so half is always going up, while the other half is coming down. “Consequently, there is no energy consumed by the belt. This shows a conveyor system is significantly more energy efficient by default.”
Improvements in consumables, such as grinding material and wear materials, provide another route to improving comminution efficiency. As just one example, in a study presented at the 12th Mill Operators Conference 2014, Metso’s Sever Ciutina and R.J. Soriano of Mabate gold mine showed how the installation of curved pump filters on the discharge of a fixed speed SAG mill reduced wear issues, increasing wear life and reducing energy consumption – without loss of throughput.11
Conclusion
The opportunities for improving comminution in the mining industry are wide and varied: this article has barely scratched the surface! Ideally, consideration should be given to energy efficiency as part of the design process, as the greatest ability to influence energy consumption comes when it is included early in the planning. Even at brownfield sites, however, achieving “additional throughput in grinding circuits as a result of energy savings unlocking additional energy capacity should form part of the business case when exploring the potential of equipment and circuit changes.”12
References
- Mining Energy Consumption 2021: A High-Level Study into Mining Energy Use for the Key Mineral Commodities of the Future (Engeco; 2021).
- Comminution and Why Smart Companies are Focussing on it (CEEC): https://www.ceecthefuture.org/images/infographic/comminution-infographic.png
- According to a study by Ndhlala, crushing circuits account for 3%-5% of energy consumption in Botswana: Ndhlala, B., Modelling, Simulation and Optimisation of a Crushing Plant (July 1017), p. 1.
- Mining comminution – crusher, ball mill and advanced analytics? (3ag Systems; 20 February 2019): https://www.3agsystems.com/blog/mining-comminution-crusher-ball-mill-advanced-analytics
- Mining Energy Consumption 2021, p. 38.
- Conger, R., Robinson, H., and Sellschoop, R., “Inside a Mining Company’s AI Transformation” (McKinsey; 5 February 2020): https://www.mckinsey.com/industries/metals-and-mining/how-we-help-clients/inside-a-mining-companys-ai-transformation
- Lynch-Watson, S., “How to Ensure Energy Efficiency in Mining 2/4: Process Optimization” (Metso: Outotec; 10 December 2010): https://www.mogroup.com/insights/blog/mining-and-metals/how-to-ensure-energy-efficiency-in-mining-part-two/
- Judd, N., “An Integrated Approach to the Drill and Blast Process” (Hexagon; 21 August 2020): https://blog.hexagonmining.com/an-integrated-approach-to-the-drill-and-blast-process/
- Dierx, B., “Why Gold Mines are Adopting HPGRs to Increase Production and Improve Recovery”, (Weir; 2 February 2021): https://www.global.weir/newsroom/news-articles/why-gold-mines-are-adopting-hpgrs-to-increase-production-and-improve-recovery/
- Boyston, A. and Lunch-Watson, S., “How to Ensure Energy Efficiency in Mining 4/4: Efficient In-Pit Crushing and Conveying”, (Metso Outotec; 11 January 2019): https://www.mogroup.com/insights/blog/mining-and-metals/how-to-ensure-energy-efficiency-in-mining-44-efficient-in-pit-crushing-and-screening/
- Ciutina, S. and Soriano, R.J., “Curved Pulp Lifters – Can They Save Energy”, Proceedings of the 12th AUSIMM Mill Operators’ Conference 2014 (AUSIMM; 2014), pp.109-116, cited by Lynch-Watson, “How to Ensure Energy Efficiency in Mining 2/4”.
- Mining Energy Consumption 2021, p. 37.