In the daily dash to hit production targets, mines can often overlook the value of reconciliation. Yet when done well and integrated into day-to-day operations, this technically challenging task will highlight key opportunities to deliver operating, financial, and sustainability improvements. North American Mining took a deep dive into this critical topic, guided by a group of the world’s leading experts.
By Jonathan Rowland
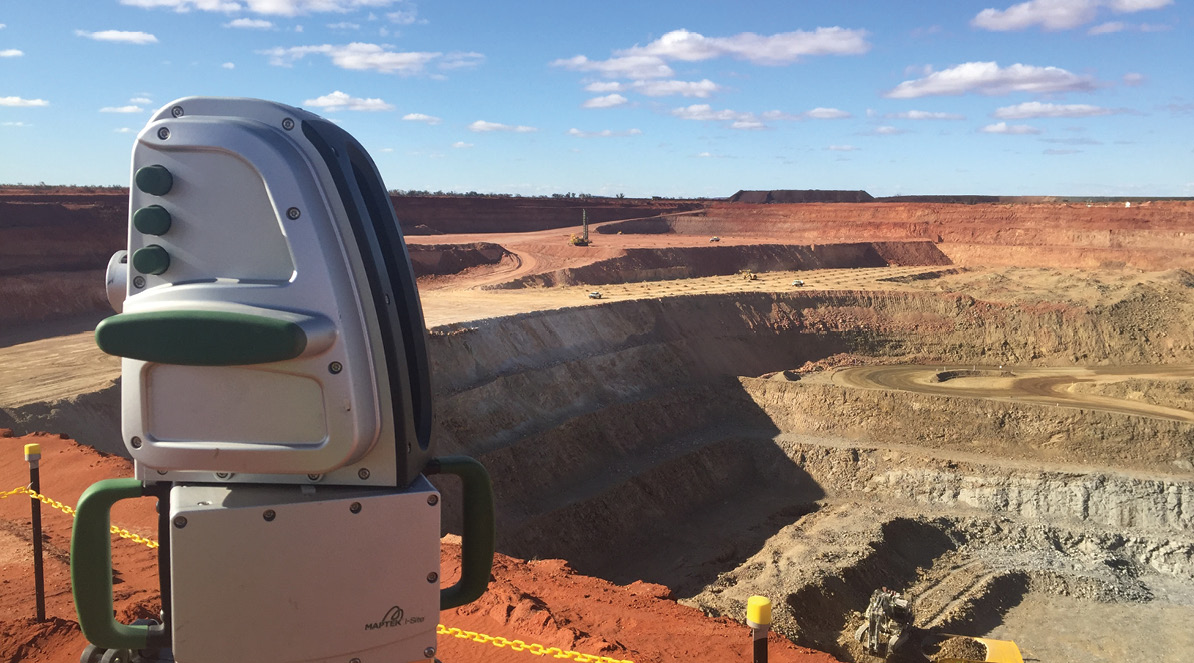
Mining reconciliation involves identifying, analyzing, and managing variation between predicted ore quantities and grades, as provided in resource/reserve models and ore grade control information, and the measured production, usually from a processing or treatment plant. The aim is to “highlight opportunities to improve a mine or a company’s performance,” Craig Morley, executive consultant and expert in mine geology and reconciliation at Snowden Optiro, an independent mining and geology advisory and training business within the Datamine Software Group, told North American Mining.
It is a multi-disciplinary process, with “data sourced across departments, including geology, mining engineering, operations, and metallurgy, to deliver benefits throughout the mining value chain,” continued Morley. “Recently the addition of other data has enhanced reconciliation. For example, the inclusion of geometallurgical data into models has gained focus in planning, and also for reconciliation, as it is important to ensure the accuracy of assumptions on rock characteristics, as they appear in mine plans, and to measure the impact on plant throughput and recovery, if those plans are to achieve their goals.”
“We typically split reconciliation into two categories,” added Nathan Flesher, a partner and mining practice leader at McKinsey. “Geological reconciliation is concerned with ‘Did we extract what we expected?’ and compares the volumes, grades, qualities, and spatial compliance of the geological model to the actual extracted values. Operational reconciliation is concerned with ‘Did we hit the rates we anticipated in the places we planned?’ and compares the operating parameters (e.g., OEE, spatial compliance) used in building a mine plan to actual performance. The outputs indicate how efficient or inefficient the planning and production processes are. Mines can use this information to continually refine and improve performance.”
Another facet of reconciliation is expectation management, of both company management, and of shareholders and potential investors, noted Ian Glacken, executive consultant with Snowden Optiro’s geology advisory services. “Various predictions inherent in the mine value chain are in the public domain. For example, reporting codes ask companies to disclose their resource and ore reserve reconciliations on an annual basis. Mining companies must also clearly report their fiscal mining and metal recovery performance by deposit; they need a reconciliation process to verify and validate this information.”
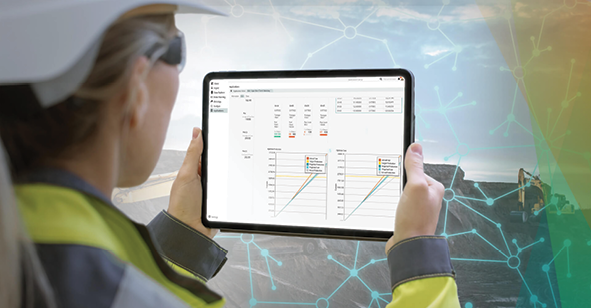
Hugely important
The importance of reconciliation to mining operations and businesses derives from the fact that “mining operations – and the investments that enable them – are largely based on assumptions,” explained Peter Johnson, chair of mining software company, Maptek. “These include assumptions about orebody quality, size, and shape; about the structure and geotechnical characteristics of the rock; about economic conditions in the future; about equipment performance and any number of other variables that cannot be locked in when the decision to mine is made. That decision is based on the best possible plan at the time, bearing in mind all those assumptions, which means it is not perfect.”
“Assumptions are notorious for causing problems,” Johnson continued. “Mining operations rarely run exactly to plan, usually due to variation from the assumed data used in the mine plan. Accurate reconciliation is an effective way to measure and understand this variation and to identify its sources and probable causes. Mines can then adjust assumptions during the planning cycle for more accurate mine planning in the future.”
Accurate reconciliation is “hugely important,” agreed McKinsey’s Flesher. “It is a fundamental requirement for a well-functioning mine, enabling companies to develop effective production plans and budgets and to provide accurate production guidance to shareholders. If this is unreliable, credibility suffers, which can impact the allocation of resources, such as equipment and capital. Poor reconciliation, leading to subpar performance, also drives destructive short-term operational behaviors to catch up production, such as high-grading or mining out of sequence.”
“Metal and value loss, linked to poor operational planning and execution, highlighted by reconciliation, remains a widespread problem across the mineral sector,” added Snowden Optiro’s Glacken. “With an ever-increasing drive for cost reduction and/or mine optimization, there is growing industry acceptance that the greatest untapped potential for profit improvement lies with enhanced mine-to-mill planning, execution, and reconciliation.”
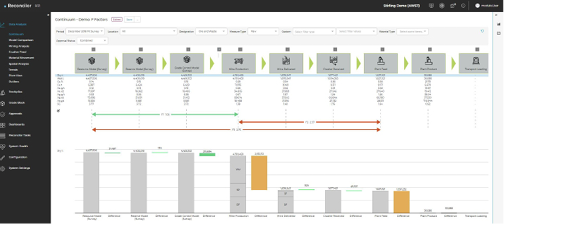
Reconciliation gone wrong
For all its importance, reconciliation is a complex process that can easily go wrong. And even when done right, mining companies may not put the lessons learned to effective use. “Geologists, engineers, and metallurgists often face contradictory information while attempting to balance metal, independently or collectively, for virtually all selected time intervals, from weekly to annually,” Glacken continued. “A process that is meant to quantify and resolve differences between resource and reserve depletion, together with mill production, is often opaque at the mine site level.”
“The most common poor practices are lack of transparency in how the data is collected, how the calculations are done and, most importantly, how the results are communicated and used to drive change,” agreed Patrick McCann, senior expert with McKinsey’s mining business. “Organizations often use reconciliation to justify why they missed the plan, but then they move on and continue to make deficient plans instead of updating their processes, assumptions, and execution to drive continuous improvement.”
“It is also common for Resource and Reserve estimates to be completed by a team remote from the mine,” added Snowden Optiro’s Morley, “while a completely different team is responsible for the short-term mine plan, which is built on updated data and geological models informed by mining.”
Reconciliation between these plans may be “routinely carried out, but no actions taken,” Morley continued. “When it comes to execution, the mining team often only focuses on a ton target, rather than delivering a quality feed to the processing plant. This impacts throughput and recovery, leading to off-spec product. Reconciliation will quantify these issues in a report, but often companies will still pay bonuses for hitting targeted tons moved. There is thus no incentive to learn from reconciliation, even as targets are missed, and value lost.”
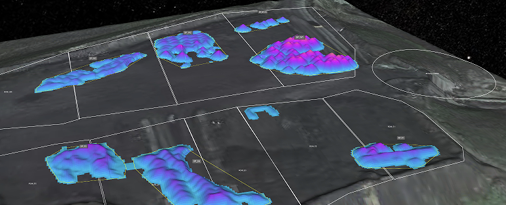
reconciliation that improves mining operations.
Thinking spatially
Beyond this disconnect between technical and operational processes, one must also remember that “mining is a spatial industry,” as Maptek’s Johnson pointed out. “The shape, volume, size, and location of all activities onsite are critical to execution of the business model. The inability to locate and measure tasks spatially, in an accurate and timely manner, is thus a key source of poor reconciliation outcomes.”
Examples here might include blasting practices that do not accurately measure the shape of the blast bench, locate drilling and charging tasks, or record post blast shapes. Another common source of error is incorrect dumping locations (waste to ore stockpiles, or ore to waste dumps). “Fleet management does not solve this problem, as there is no spatial awareness of the mine plan, and no real-time solution to identifying and tracking deviation from plan,” added Johnson.
There is also the issue of when reconciliation takes place. “All mines undertake reconciliation,” explained Rudy Moctezuma, chief business relations officer at Eclipse Mining Technologies. “The problem is they do it after the fact, and not when these issues are happening. Ideally, mines would capture technical data in near real time, as the earlier you have the information – and the more information you have identifying the issue – the sooner you can make decisions, and the better those decisions will be. Too many mines use reports that provide information after mining has occurred, after the shift, by which time it is too late.”
Embracing digitalization and automation
“For those involved in mining reconciliation, it is well-known that spreadsheets are ubiquitous and deeply ingrained in mining operations worldwide,” noted Rayleen Hargreaves, principal consultant, and product owner of Datamine Software Group’s Reconcilor software. “Spreadsheets have a proven, albeit sometimes debated, value in reconciliation processes. However, mismanagement of spreadsheets, whether accidental or intentional, can have potentially disastrous consequences on an operation. Over the past two decades, advancements in information technology have heightened awareness of these issues, prompting operations to seek automation in data management. This shift aims to mitigate risks and prevent errors that could lead to poor decision-making.”
Specialist digital and software provide the tools for accurate data management (reducing the risk of human error); they also enable real-time monitoring and provide actionable intelligence for faster and better operational decision-making, leading to improved regulatory compliance, cost efficiency, and sustainable mining practices. Key features of these solutions include:
- Automated data capture, integration, validation, and analysis:
- Integrating data from various sources (geological models, mine planning, production records).
- Rigorous data validation and quality control to ensure data accuracy and consistency.
- Data visualization and analytics (including AI) to gain actionable insights and identify trends
- Standardized workflows and procedures for reconciliation activities across all mine sites, clearly defining roles, responsibilities, and timelines for each step.
- Regular, comprehensive, and timely reporting to identify discrepancies and anomalies, and provide insights into production volumes, grades, inventory balances.
- Enhanced decision-making supported by access to accurate and up-to-date information, regular reviews, and audits to identify areas for improvement, and continuous learning, training, and upskilling to enhance reconciliation expertise.
- Transparency of the data and calculations used, and repeatability of the reported results.
With the development of such integrated digital tools and centralized data platforms, “mine plan reconciliation has the potential to become less of a distinct event and more of a continuous process, shortening the cycle between the emergence of deviations to the mine plan and their correction,” concluded Karilyn Farmer, practice expert at McKinsey.
Other benefits of enhanced reconciliation
The ability to identify and react to challenges more quickly also helps mining operations adapt to “increasingly complex mining methods and safety issues, as well as higher production costs, due to declining and more complex ore grades,” said Eclipse Mining’s Moctezuma. “This requires solutions that go beyond centralizing data to create relationships between the original data and the new data, allowing the system to ‘understand’, as you mine, when parameters are changing from the original plan and that, as they do, it may affect areas such as blasting and processing.”
A “superior mine reconciliation approach can also support the sustainability of mining operations,” added Farmer. “The mine planning, execution, and reconciliation cycle can help ensure that the mine is minimizing emissions and efficiently using inputs such as water and fuel. It can also help to identify further sustainability opportunities that may require alternative approaches to mining or implementation of innovative technologies.”
Failure to reconcile; reconcile to failure
For all the benefits, adapting to new ways of working is always a challenge in an industry still so wedded to its spreadsheets. Communication again is an issue here. “With mines still working in siloed departments, the communication required to integrate data across the mine value chain can be problematic,” said Datamine’s Hargreaves. “Typically, this silo mentality is at its most pronounced between the mine and the processing sections, and it is often (but not always!) a challenge to break down.”
And then there is cost, as Snowden Optiro’s Morley noted. Cost is always problematic when trying to change processes or bring new software onto a site. But “as geologists and specialists in reconciliation, we need improve our ability to identify value added and report the dollars that reconciliation adds to an operation. This justifies the work and the spend and enables continuous improvement.”
“It is much easier to reconcile on a short-term basis – number of truck trips for ore, number for waste, tons, grade, recovery,” concluded Maptek’s Peter Johnson. “Month by month, mines can manage these numbers to achieve short-term goals; however, in the longer term, these decisions may not be correct. Reconciling against longer-term goals and plans is thus also important. Practices such as high grading, short hauling, or stockpile raiding to meet short-term targets can sterilize an orebody, or seriously impact the likelihood of meeting future targets. Reconciliation against a range of time periods allows engineers to avoid such mistakes and make decisions that balance near term objectives with the longer-term viability of the mine business.”
“Ultimately, mines operate over many years, while being expected to be profitable for the entire mine life,” said Johnson. “Mines that close before the planned end of life have usually failed at some point to reconcile variations between the mine plan and the actual performance.”