North American Mining spoke to Penn State’s Prof. Barbara Arnold about the current state and future of coal preparation in the U.S.
By Jonathan Rowland
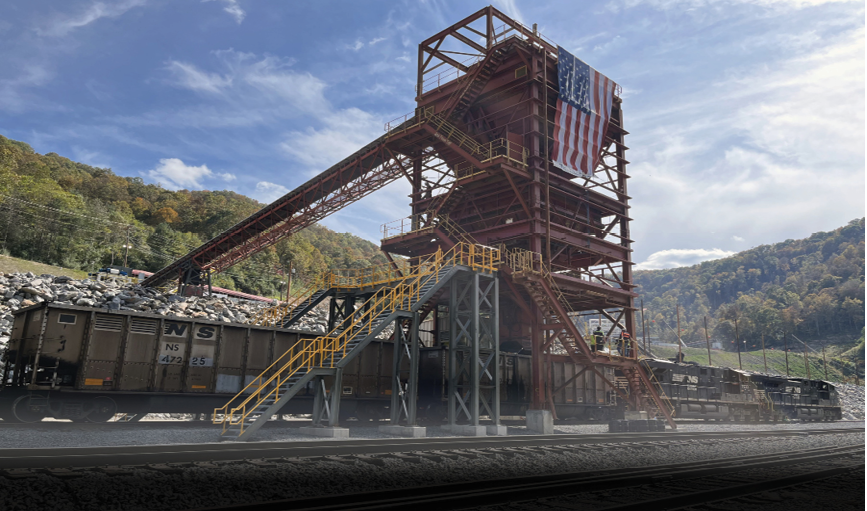
There are 154 coal preparation plants active in the U.S. with a further 73 idled. That is still a “decent number,” according to Barbara Arnold, who has spent over three decades involved in the coal preparation industry and is currently professor of practice in mining engineering at Penn State. “It is the metallurgical coal plants that are getting more attention and are likely to drive any expansion,” Arnold continued, highlighting the example of CONSOL Energy’s Itmann preparation plant.
Located in Wyoming County, W.Va., and commissioned in late September 2022, this $100 million plant processes low-vol metallurgical coking coal from the company’s Itmann No. 5 mine. When fully operational, the mine is expected to produce about 0.9 million tons for domestic and international steel markets. However, the preparation plant has capacity to process roughly double that, which “provides additional upside for third-party processing and blending,” the company said in a 2022 press release.
It illustrates an important point when discussing coal: there is coal and then there is coal. Metallurgical coal was described as the commodity world’s “quiet performer” in a February 2024 Reuters column and has been a top performer among energy commodities in recent months. Although the export market is dominated by Australia, the U.S. is second on the list and – unlike the Aussies – has a substantial domestic steel-making market to support demand.
On the other hand, thermal coal “faces some headwinds,” said Arnold, with a degree of understatement.
The bête noire of the environmental movement, all major pathways to net zero call for the phasing out of coal as quickly as possible. For all the rhetoric, this is a challenge. As the International Energy Agency noted in a 2022 report on the place of coal in net zero transitions: “coal demand – far from declining – has been hovering at near‐record highs for the past decade [with] more than 95% of current global coal consumption occur[ing] in countries that have pledged to achieve net-zero emissions.”
This includes the U.S., which has pledged to achieve net-zero emissions by 2050. Whether that goal survives this year’s presidential election is yet to be seen: what is apparent is that phasing out coal is not as easy as issuing a press release or catchy soundbite. “Until there is a replacement, you cannot just turn off coal plants,” said Arnold – stating an obvious but oft-ignored truth. “There has to be a transition, and that transition may well take longer than people think.”
As one example: in February 2024, FirstEnergy Corp. admitted it was abandoning targets to cut greenhouse gas emissions by 2030 because of challenges around retiring two of its coal-fired power plants in West Virginia, which represent about 1.5% of coal-fired power capacity in the U.S. A month earlier, grid operator PJM had requested another operator, Talen Energy, delay the retirement of two coal-fired units in Maryland due to reliability concerns.
“Take all of the above, and the need for coal preparation plants – both thermal and metallurgical – will continue for a good while yet,” concluded Arnold. “But we are also using coal for so much more now.”
New opportunities in coal
“Coals and coal-waste products are increasingly being looked at as an economic source of critical minerals, including rare earth elements (REEs),” continued Arnold. “These minerals are essential to – among other things – the net zero transition, so it may be an irony of history that a resource as pilloried by the environmental movement as coal may ultimately end up being essential to its success.”
One of the major announcements in this area came last year with the discovery of significant magnetic REE deposits at Ramaco’s Brook coal mine site in Wyoming, which is estimated to hold between 181,000 tons and 226,000 tons of magnetic rare earth oxide, making it one of the most promising REE deposits globally.
According to geologists at mining consultancy, Weir International, the “coal seams [at the Brook property] can contain significant quantities of REEs, making the coal seams an attractive source for these valuable minerals on an ash-basis. The REEs are believed to have been incorporated into the coal during its formation and are found in association with clay minerals and organic matter in the coal seams. Interburden between the coal seams also contain elevated levels of REEs, primarily in clays, carbonaceous clays and siltstones, and not necessarily associated to the coal seams.”
Elsewhere, the U.S. Department of Energy CORE-CM projects are assessing the viability of coal and coal waste streams as sources of REEs and other critical minerals, as well as non-fuel carbon products, such as graphite. Phase I of the project is focused on data collection to assess potential resources across 13 basins, with Arnold and Penn State involved in mapping the Northern Appalachian basin, which covers Maryland, Ohio, Pennsylvania, and northern West Virginia.
“As part of this, we are looking into a range of coal waste products,” Arnold explained. “For example, we have been assessing deposits of fluidized bed combustion ash and finding elevated levels of critical minerals. We are also looking at acid mine drainage (AMD) as a potential resource. The benefit there is that it has already been leached, which is one of the major steps for recovering these valuable minerals. With AMD, Mother Nature has already done that for us.”
Coal and coal waste products are also a potential source of carbon-based products. “There is current research into the production of quantum dots from anthracite,” added Arnold. “You can also potentially make graphite – a key ingredient in electric vehicle batteries – from coal. And there is research into making carbon fibers from bituminous coal pitch.”
There is then a good more to coal than coal. But to make the most of these opportunities, “we need people who understand the properties of coal and how to work with it,” concluded Arnold. And that could be where the real challenge lies.
Training the next generation of coal workers
“Skills are a huge issue,” said Arnold. “Over the next six years, we are facing a ‘grey tsunami’ as more than half of our mining workforce in the U.S. retires.” It is a multi-faceted issue. At the undergraduate level, “we need more students through the doors of our mining schools. But we also need to be teaching coal preparation at those schools.”
Arnold covers that gap by using coal data when teaching her Mineral Processing 401 class because “if you can do it for coal, you can do it for any other mineral, and it is the engineering knowledge that is going to be critical. We need people who understand how to design and engineer a new preparation plant, as well as those who can walk the plant to identify problems and opportunities for optimization.”
There is also a dearth of graduate and doctoral students focused on coal, and of more specific skills, such as coal petrologists. “I can still look under a microscope, identify the macerals, and analyze their impact; Maria Holuszko at University of British Columbia can too,” Arnold said. “But neither of us are getting any younger and there is no one stepping into our shoes. Yet this sort of analysis is important not just for your standard coal preparation activities, but for all those new applications for coal that we discussed earlier.”
Recruiting and training skilled labor is another challenge. “Many of our coal mining communities are still battling significant issues with fentanyl addictions; these communities have also experienced population decline and demographic shifts as coal mining jobs have been lost. Beyond that, there is an issue around the availability of training for the next generation of coal prep plant workers.”
Stepping into that gap, the Coal Preparation Society of America (CPSA) is now running Coal Prep 101 workshops, facilitated by Dr. Rick Honaker of the University of Kentucky – a familiar name to anyone involved in the U.S. coal prep industry. “We ran a couple of workshops last year and they sold out; we are continuing them this year,” said Arnold, who also sits on the board of the CPSA. “The CPSA will also be at CoalProTec 2024, where we are holding a workshop on magnetite and heavy media separation, as well as presenting a number of papers. It is a great training opportunity, not only for engineers, but skilled labor – the plant foremen and superintendents.”
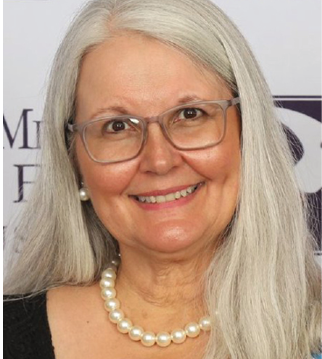
Coal will be here awhile yet
Arnold concluded by underscoring what may be an uncomfortable reality for some – but cannot be ignored either. “Coal preparation is not going away! We have to do it better. And to do that, we must have the skills at all levels to ensure we can make the most of new opportunities and applications for coal.”