Heavy mobile equipment operating in the confined spaces of an underground mine poses a serious safety hazard. Proximity detection and collision avoidance systems can play an important role in mitigating that risk.
By Jonathan Rowland
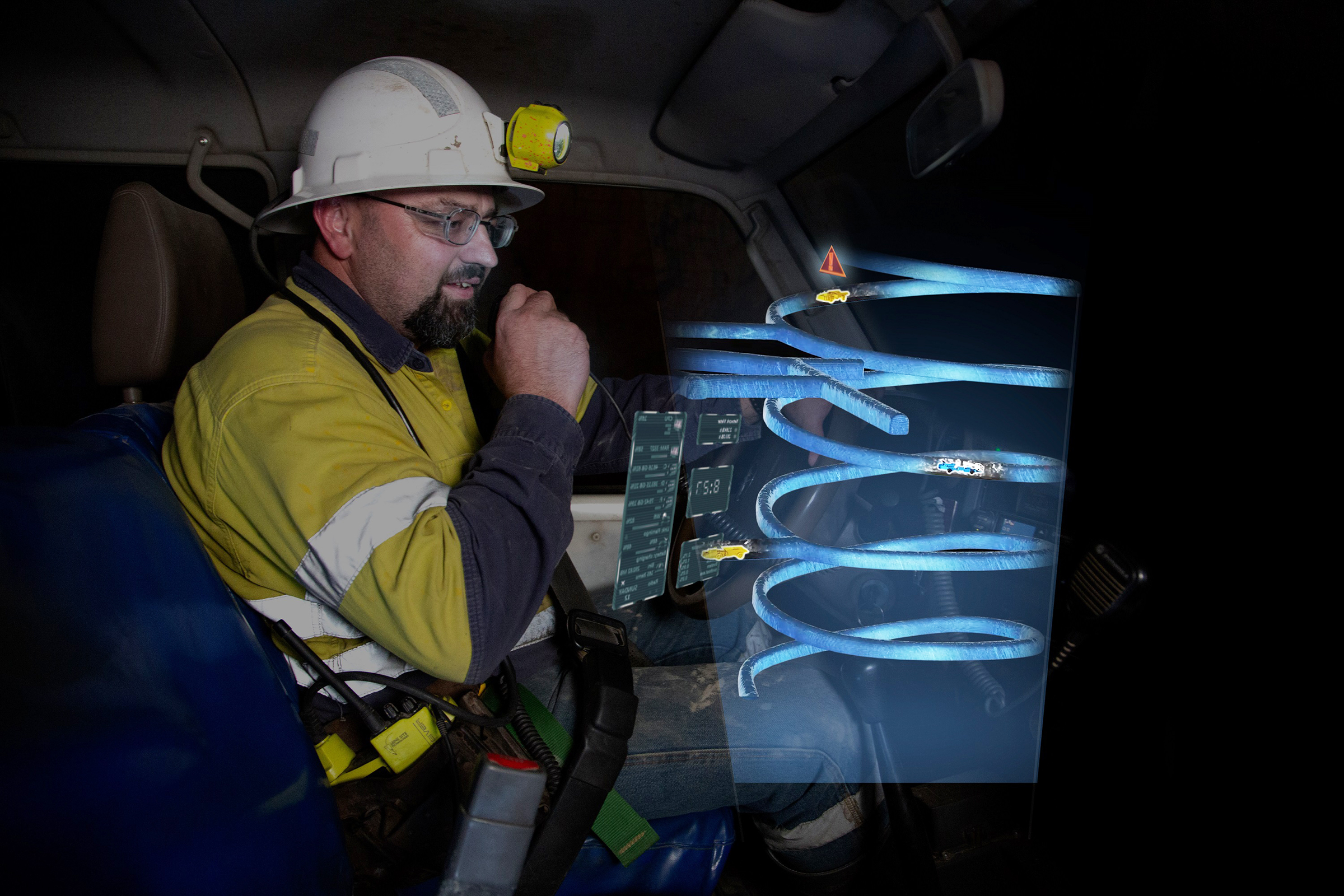
One of the biggest safety risks in an underground mining operation is the interaction between mobile assets and personnel. “The risk exposure in this area is significant, as vehicles and people continually use the same working spaces,” Caterpillar told North American Mining. “These spaces are also themselves intrinsically hazardous environments in which reduced visibility and changes to the operating context are the norm.”
Proximity detection systems (PDS) and collision avoidance systems (CAS) address these risks by targeting unwanted and dangerous machine-to-machine or machine-to-person interactions. Traditionally, PDS refers to “the tracking of remote objects around a local object, giving the operator of that local object an awareness of their surroundings, while also eliminating blind spots,” explained Florent Garin, product manager, Underground Safety, Hexagon’s Mining division. “Collision avoidance is the next step up and consists of warning the operator of the local object that a danger is imminent, empowering them to act.”
In the parlance of the Earth Moving Equipment Safety Round Table (EMESRT) – a global initiative of major mining companies to facilitate improved vehicle interaction control – PDS will generally fall under EMESRT Level 7, Operator Awareness, while CAS falls under EMESRT Level 8, Advisory Controls. At the top level – EMESRT Level 9, Intervention Controls – systems will automatically intervene to prevent hazardous interactions, e.g., through vehicle start-up prevention, slow-stop, rollback and retarder systems.
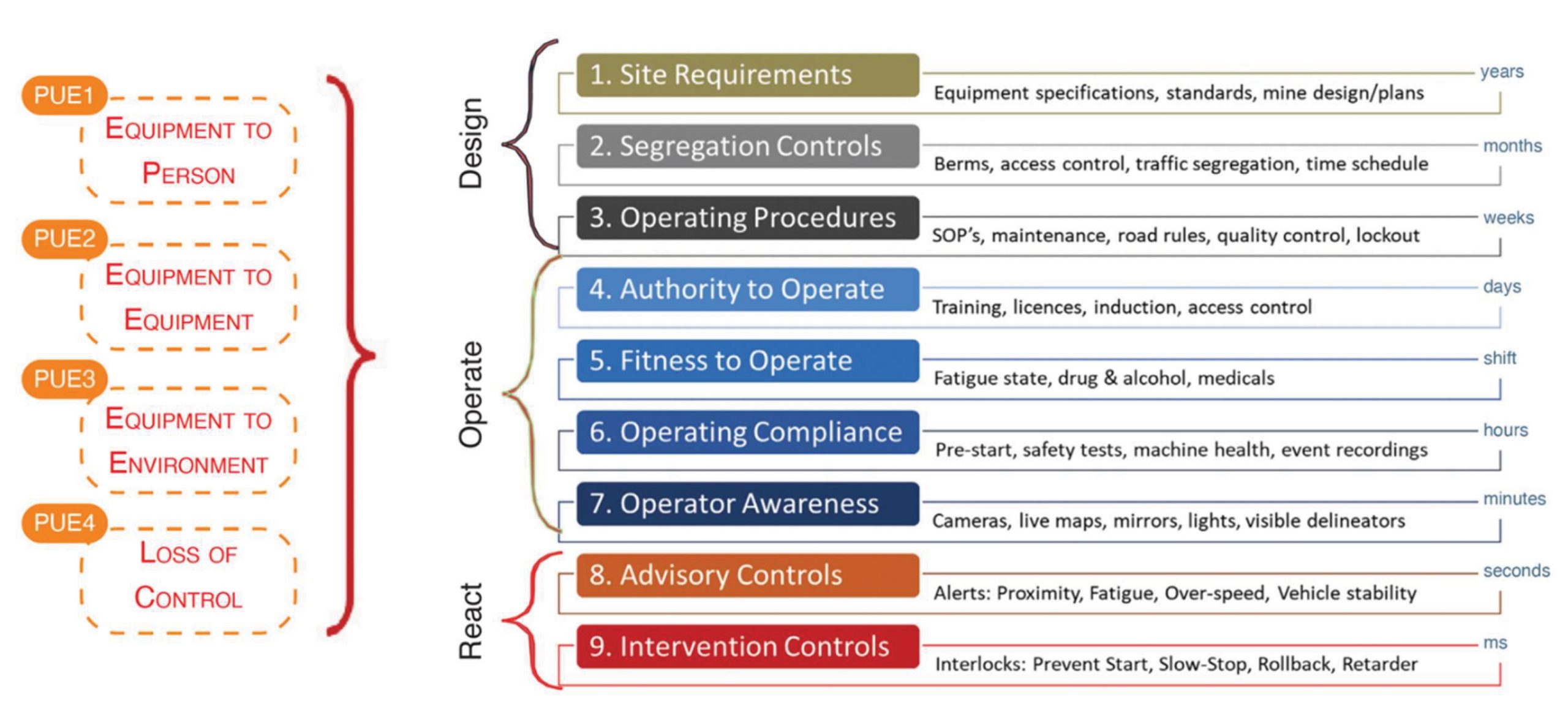
“The goal of a PDS is to decrease critical interactions,” added Mateus Quintela Chaves, head of Product, Underground Mining, Hexagon. “To achieve this, operators need the right level of information at the right time. Mines rely on technologies that are capable of accurate and precise tracking, combined with contextual information, to provide this information.”
The main technologies used to achieve this in underground mine environments are electromagnetic systems, radar, and radio-frequency identification (RFID), noted Mike Walling, president of Strata Worldwide Americas.
- Electromagnetic systems generate warning zones around machinery. Receivers worn by people and installed on machinery detect these zones and emit warning alarms. Because electromagnetic systems enable the identification of different levels of safety zones, based on distance from the machine, they have the potential to meet EMERST Level 9 capabilities for automatic slowing and stopping without operator intervention. Electromagnetic systems are also unaffected by their environment and can easily penetrate coal, rock, construction barriers, stoppings, and ventilation curtains. It warns both equipment operators and personnel-on-foot simultaneously.
- Radar systems work with sensors that send out pulse waves and detect reflections or shifts in frequency. Such an indicator represents the presence of an object or person, and an alarm is triggered. No receiver/tag is required. However, since radar is subject to alarm triggers when any object enters its field, benign objects may cause false detects and nuisance alarms. This lack of object discernment means radar is less suitable for Level 9 autonomous braking and tends to be alarm-only. Only the equipment operator is warned.
- Radio Frequency Identification (RFID) systems work by using an activator installed on machinery and small battery-powered tags worn by people. The activator sends out RF pulses to create a ‘read field’ around the machine; any tag that comes within range is activated. When this happens, the tag sends out a location signal to alert of its presence and trigger a warning alarm to the machine operator. RFID is a highly versatile and readily available technology, but it can be susceptible to interference, and the radio waves can be easily blocked.
Whatever the system or technology being used, it “must be engineered and built to withstand the different harsh conditions and elements within the underground mine environment, including water, heat, rockfalls, machine-to-machine contact, and heavy vibrations from machinery,” continued Walling. “For example, Strata products are IP67 rated, which means they are dust tight and able to withstand immersion in water for up to 30 minutes.”
The “main challenges of PDS and CAS in underground mining environments relate to the hardware,” agreed Hexagon’s Quintela Chaves. “In addition to harsh operating conditions, solutions must withstand other environmental factors, such as operating in polymetallic deposits or around ground support mesh, or the presence of other technologies in the area, such as Wi-Fi and two-way radios.”
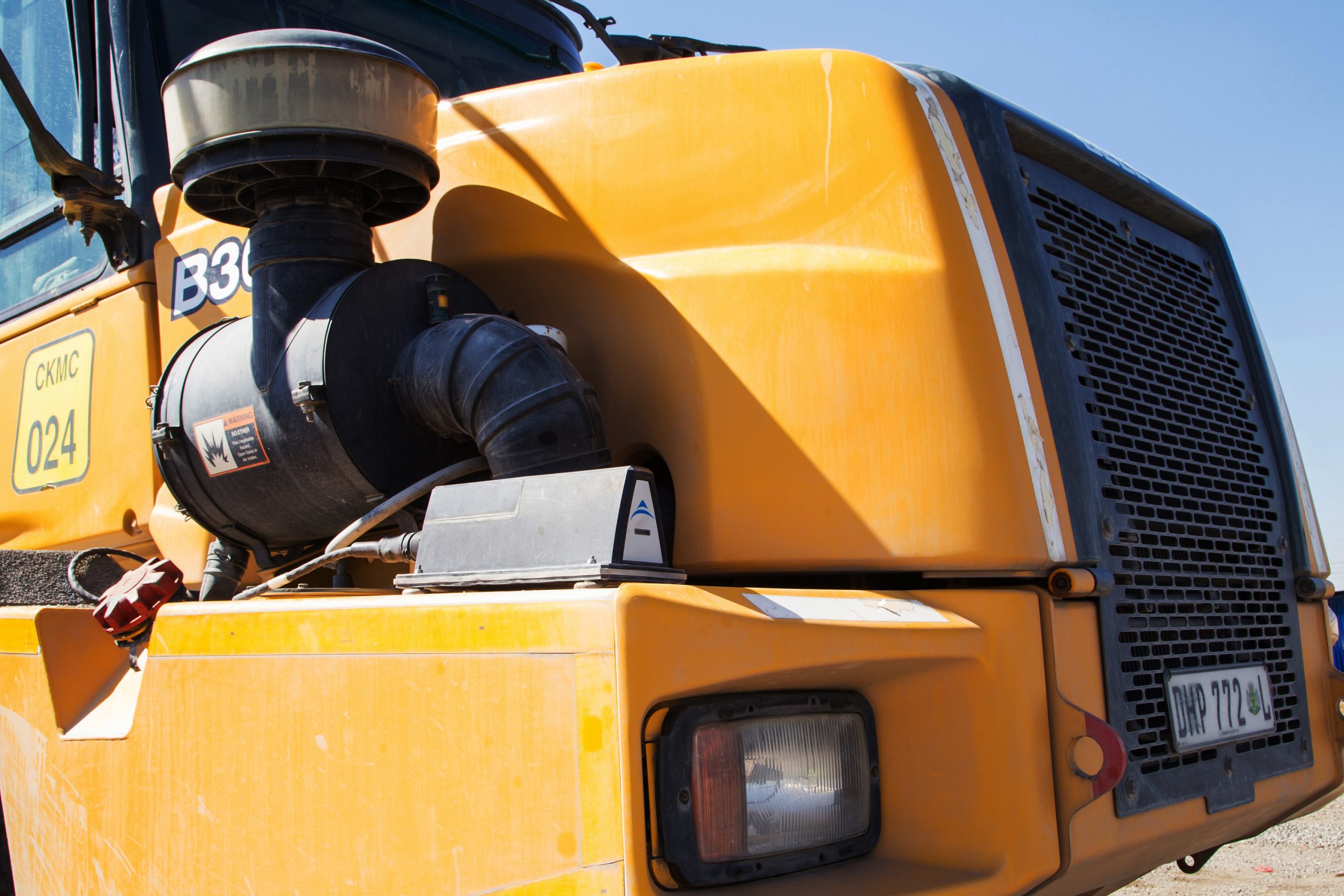
installation, but also available for underground applications) is an electromagnetic system with EMERST Level 9 capabilities.
MANDATING PDS/CAS FOR UNDERGROUND ENVIRONMENTS
Another challenge relates to the approvals and certifications required. “In the U.S., PDS must comply with Mine Safety and Health Administration (MSHA) regulations and all RF-enabled components must be certified,” said Hexagon’s Garin.
The challenge is greater for equipment designed to be used in environments where methane may be present, such as underground coal mines. Here, equipment must either be explosion proof or intrinsically safe, noted Strata’s Walling. It’s an important point to note as, in the U.S., coal mines are the only mine environment where PDS are mandated by MSHA.
“In U.S. coal mines, proximity detection is required on all continuous miners,” explained Walling. “These systems are required to automatically stop the machine before contact with a miner/operator, including stopping both the tramming of the machine and the movement of the conveyor boom. Beyond this, there are no other mandated uses of PDS or CAS in the U.S. or Canada, although many companies deploy these systems as proactive safety measures, knowing they have the capability to reduce incidents.”
This is in contrast with South Africa, which leads the world when it comes to mandating PDS and CAS in mining environments. As of December 2022, the country’s Department of Mineral Resources and Energy brought into law a mandate for Level 9 CAS to be installed on all diesel-powered mobile equipment in both underground and surface mines.
OPERATING ISSUES
Of course, however good the equipment, the “system will only work as well as it is installed and operated,” continued Walling. “Installation requires proper mounting and guarding of the hardware. Helping personnel understand the benefits and the limitations, and providing proper training is another critical element in success.”
Proximity detection and collision avoidance systems “don’t take care of the challenge alone,” added Hexagon’s Garin. “Installing the system and ‘walking away’ is the biggest mistake, and this applies to both miners and vendors. These systems impact the mining operation and must be socialized with all relevant stakeholders: the technology group, IT, operations, maintenance, training, and so on. Failure to have the whole team embrace the PDS/CAS system will inevitably result in poor acceptance and, therefore, poor performance. Technology is just another layer of safety, so to deliver the full potential of these systems, the context in which they are deployed must be well understood.”
This point was emphasized by Hexagon’s Quintela Chaves. “Effective change management is so important for the successful implementation of any new technology. It’s absolutely critical to have support from all stakeholders in order for PDS/CAS to work to its fullest potential to get miners home safely – which is what we all want.”
“There is no technology in the world, in any industry, that can solve every issue or prevent 100% of incidents from occurring,” concluded Walling on this point. “Technology is technology and it has its limitations. However, collision avoidance technology in mining has been proven to reduce incidents by more than 70%. It should therefore be considered a must-have for all operations looking to increase safety.”
LOOKING TO THE FUTURE
Where then will the technology go next? According to Strata’s Walling, it’s likely that technologies will begin to be used in combination.
“I see the potential for multiple technologies – radar, electromagnetic, laser, ultra-wide band, etc. – to be rolled into one system. Right now, there are cost limitations with this concept, as an all-in-one product would be too expensive. But as technology evolves and systems become more affordable, I expect to see the development of more multi-capable solutions.”
It’s a vision shared by Hexagon. “Rather than providing point solutions that only provide PDS and last resort safety nets, PDS/CAS will move towards more contextual, scalable, and integrated systems that will be leveraged to increase productivity through traffic management,” Quintela Chaves predicted.
BEYOND SAFETY
In addition to enhancing the safety of mine personnel and equipment, the improved site awareness being made possible by advanced PDS/CAS systems can help improve productivity and performance. According to Caterpillar, “with better site awareness, operators can run their equipment with more confidence. Cycle times can also be improved when operators know that loading and dumping areas are clear as they get ready to pull away, allowing them work more smoothly and efficiently.” Specific benefits include:
- Reduced traffic congestion for improved safety and reduced truck load and idle times.
- Insight into vehicle locations on major access ways, which can be used to reduce the number of times haul vehicles need to stop for light vehicles of other low priority assets.
- Monitoring of the load and haul activities, adding greater consistency in material handling and grade control.
- Dynamic instruction of operators to perform specific tasks based on their proximity to different areas, such as fuel bays and park-up locations.
- Locate idle or parked-up equipment throughout the mine, significantly reducing search times at shift times and maintenance cycles.
- Assets can also be safely monitored around areas of interest, including declines, production levels, crusher tipples, ore passes and stockpiles, workshops, and refuge chambers.