Mining tires represent a significant investment; they are also an opportunity to improve not only the efficiency of a mining operation, but also its sustainability. So how can a mine ensure it gets the most economic and environmental benefit from its tires?
By Jonathan Rowland
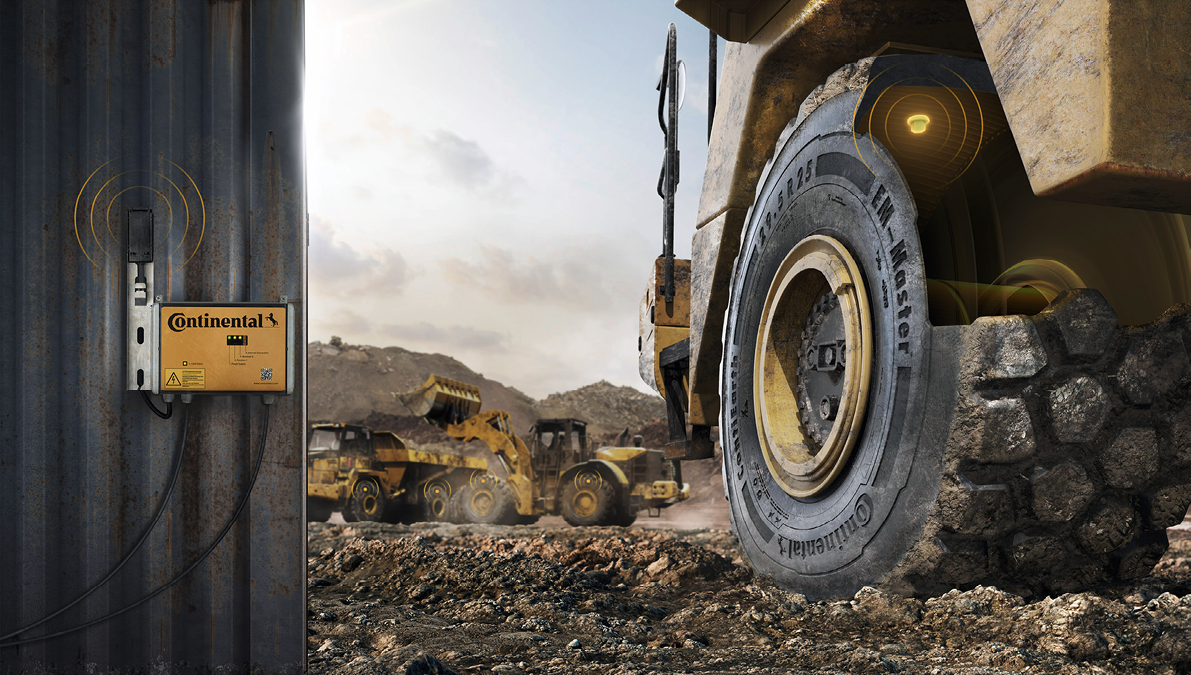
Even under the best of circumstances, tires wear out. But mining is about the most challenging environment to which a tire can be exposed: the industry generates huge tonnages of used tires every year as a result.
In Australia alone, the industry was responsible for 68,000 tonnes of used tires in 2019, according to Tire Stewardship Australia, an organization formed to promote the development of viable markets for end-of-life tires. The vast majority of these were disposed of on-site.
However, on-site disposal creates ESG risks. “The biggest and most catastrophic threat is fire,” explained Dave Allan, vice president Canada at Kal Tire’s Mining Tire Group. Although tire fires are uncommon, when they do occur “people notice, and they notice for a long time, as tire fires are very difficult to extinguish quickly.”
Another risk, particularly with large mining tires, is space. “On a mine site, space is often a valuable commodity: a commodity that stockpiling used tires consumes,” continued Allan. “Tires can also collect unwanted things inside of them. Whether this is burrowing animals or standing water that may act as a breeding ground for disease-bearing insects – which can pose safety risks for individuals who eventually have to move them – stockpiled tires are not something that mines should really want to keep around for longer than needed.”
Of course, end-of-life tires must also be replaced, and this is where ESG issues start to snowball. “While tire dealers and manufacturers work together to dispose and recycle tires properly, each new tire consumes a tremendous number of resources – from manufacturing to supply chain – increasing the ESG-related costs,” said Matt Johnson, vice president of MAXAM Mining Group, the dedicated mining segment of MAXAM Tire.
“For mining tires, it is important to improve the cradle-to-grave environmental impact,” agreed Adam Murphy, senior vice president, Michelin Mining. This includes “what raw materials are extracted and used in the design and production of tires, how energy efficient they are while in use, and what happens to those tires at the end of life.”
Tires can also play a role in tackling some of the major macro challenges facing the industry. For example, they can improve the efficiency of a mining operation by delivering greater durability or allowing faster speeds or higher payloads, explained Rob Seibert, president, Off-the-Road, U.S. and Canada at Bridgestone Americas. “That increased production can translate to impactful financial savings for an operation.”
“The responsible tire industry – and specifically the mining tire industry – has to face the challenge to move toward to more efficient, more sustainable vehicles, products and processes, with more sustainable materials,” added Reinhard Klant, product manager for earthmover tires at Continental. This includes embracing and providing solutions for trends like electrification and digitalization. “To efficiently shape the tire-use phase with our customers is of major importance. End users are seeing the powerful influence of these trends on sustainable operations.”
Mining tires are thus a mixed bag of ESG risks and opportunities that spiral out to influence the wider mine environment. However, what is clear is that you overlook a tire at your peril: careful consideration and management across the complete tire lifecycle is needed to reduce the risks and make the most of the opportunities.
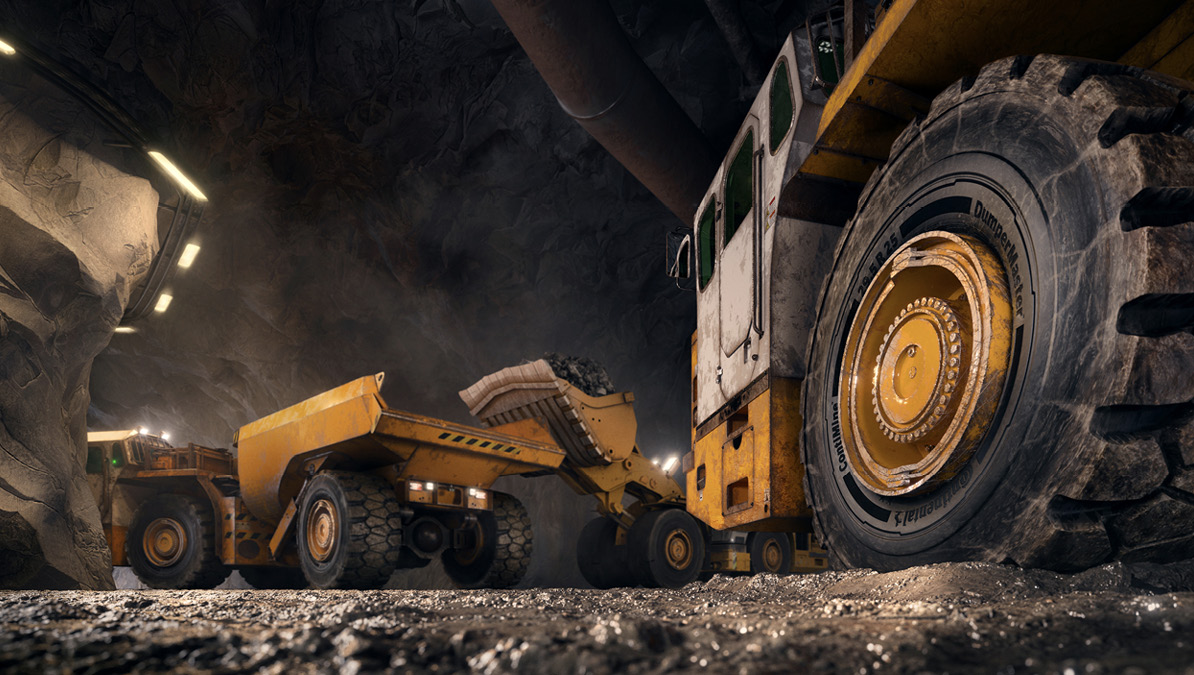
THE FIRST STEP: TIRE SOURCING
“Quality input means quality output,” said Eric Matson, manager of Global Field Engineering, OTR, at The Goodyear Tire & Rubber Co. “A high-quality premium product will have the lowest total cost of ownership over time and allow for more sustainable choices over the life of the tire, such as re-treading.”
Continental’s Matthew Futrelle, head of business field Earthmover Tires, agreed: “Mine operators are trying to get the most saleable ore from their operations, at the lowest cost possible, to maximize and protect their value. When it comes to tires, premium quality products, with a long operating life, optimize resources by minimizing the total cost of ownership.” A key part of this is “using the right tire for the application. An application analysis and enhanced consultancy can make a decisive difference here.”
Matt Johnson of MAXAM Tire also raised the importance of site conditions when sourcing a sustainable tire solution. “Some of the most common issues we see when visiting mines to diagnose problems is customers not using the right compound in their OTR tires. To optimize sustainability – especially when dealing with haul truck tires – it is critical for the site to commission a site analysis from either the tire dealer or the manufacturer. This will help ensure selection of an appropriate tire compound for the road conditions and haul applications.”
Johnson went on to provide the example of a site that runs at higher speeds, with little debris on its haul roads, where MAXAM Tire “would recommend a tire that contains a heat-resistant compound, because these evacuate heat.” However, such tires would not be appropriate on abrasive surfaces that have higher tonne kilometers per hour (TKPH) conditions. “It is therefore critical for a mine to understand the site conditions its tires will operate in and source from there.”
When it comes to placing tires within the wider issue of mine sustainability, “life cycle assessments (LCAs) are useful for understanding the environmental impacts of products, services, and solutions,” explained Michelin’s Adam Murphy. For example, Michelin assesses each stage of a tire’s life cycle against 16 environmental impacts, measuring health, climate change, use of fossil resources, and biodiversity. “From these analyses, the most significant environmental impact occurs when tires are in use: a tire’s energy efficiency – its rolling and motion resistance – is key to helping mines reduce CO2 emissions.”
MAKING A SUSTAINABLE TIRE
The second most significant impact is raw materials, continued Murphy. “The use of renewable and recyclable materials in mining tires minimizes the impact of natural resources.” For example, Michelin is working to progressively integrate sustainable materials into tires with the goal of achieving 100% sustainable materials by 2050. The company is also working with customers to develop end-of-life tire recycling solutions that eliminate waste at mines and increase circularity.
Other manufacturers are working toward similar goals:
- Bridgestone is working to achieve 40% renewable material
in its full tire portfolio by 2030, said Rob Siebert. “Our OTR
business has been ticking off major self-mandated milestones in an effort to reduce our impact and increase sustainability of the raw materials we need to make our tires.” - Sustainability is an “integral part of our Vision 2030 strategy
for the tires group sector,” explained Continental’s Klant. “We follow a holistic sustainability approach that takes into account all phases of a tire’s value chain and continuously invest in R&D into alternative and sustainable materials, as well as environmentally-friendly production processes. By 2030, our flagship tire products will contain 60% sustainable materials.” - MAXAM Tire “works with dealers to sustainably dispose of
tires, as well as targeting our manufacturing processes,” said Johnson. Its latest tire compounding technology, for
example, enables “optimum mixing uniformity” during production, which not only improves performance and durability, but also “represents a breakthrough in green and low-carbon tire development.”
Sustainability also means taking aim at the carbon emitted during tire production. For example, Bridgestone is working to achieve a 50% reduction in CO2 emissions by 2030 from a 2011 baseline, said Siebert. “Our Aiken County plant in South Carolina has taken tremendous strides in reducing its Scope 1 and 2 emissions. This is achieved by minimizing material waste, leveraging rail transportation, and being mindful of emissions from purchased energy.”
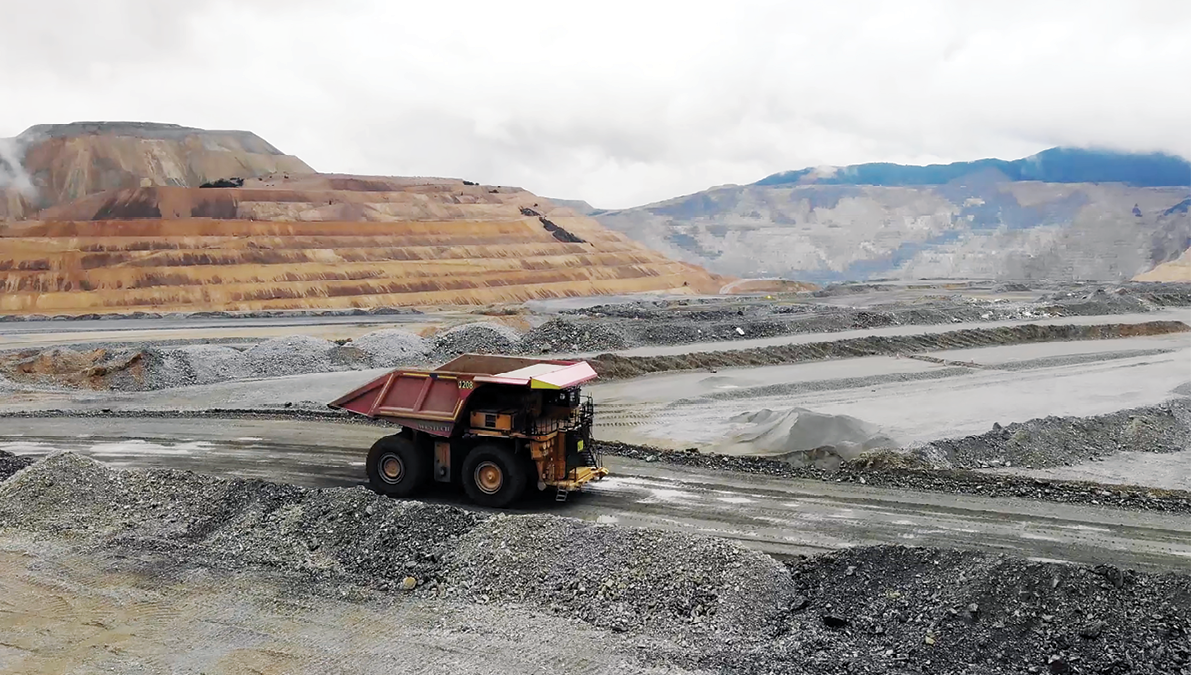
STEP TWO: TIRE MANAGEMENT AND MAINTENANCE
Progressive tire management is the next step in achieving a sustainable tire life cycle. This begins by “understanding the times when more (or fewer) tires are needed due to seasonality,” said Kal Tire’s Dave Allan. “Ordering more than you need for spring break-up – in cold Canadian conditions, for example – and fewer tires through winter months not only helps budgets, but also helps with ESG issues.”
When it comes to maintaining an operating tire, the expert consensus was clear: know your tires. “Tires are a significant investment,” explained Goodyear’s Eric Matson, “so it makes sense to take steps to optimize their performance and longevity. Since the needs vary from customer to customer and site to site, a tailored tire maintenance program is needed, including tire inspection, performance tracking, and data analysis for actionable insights and reporting.”
TIRE INSPECTION
Daily inspection of tire inflation and wear “should be the cornerstone of any maintenance program,” continued Matson. “Maintaining proper inflation levels is one of the most effective practices that a mining operation can employ to achieve enhanced tire performance and longer service life. Including an automated tire pressure monitoring system can help maintain inflation and increase energy efficiency, which has an impact on fuel cost and carbon emissions.”
A pre-shift inspection is “easy enough to conduct and makes a significant difference in increasing uptime and safety,” agreed MAXAM Tire’s Matt Johnson, who also stressed the importance of tire pressure monitoring. “The difference between cold and hot pressures should be established every season, for every cycle and wheel position separately. This can be set by adjusting cold pressures on a vehicle after servicing in the workshop and repeating the operation immediately after at least four hours of constant operations.”
According to Continental’s Klant, if tire pressure is optimized, an operator can save 15 minutes per vehicle (195 hours per year) on inspection, increase fuel efficiency by 1%, and gain 15% longer tread life on average, compared to a tire that is 10% underinflated. In short, “an incorrect tire pressure means significantly higher fuel consumption – and thus, depending on the fuel, higher carbon emissions – as well as a huge waste of resources and money.”
Inspections should also “watch for deep cuts to the steel, bubbles in the sidewall, and severe tread damage,” continued Johnson, which may indicate overloading or debris on the haul roads that is causing damage. “Finally, always check wheels to establish tire and/or rim damage, as bent or cracked rims may cause air pressure loss, resulting in under-inflation and overloaded conditions. In severe cases, this can result in structural damage and even tire explosion.”
In addition to visual inspections by human operators, AI-powered autonomic tire inspection stations are now available, utilizing thermal imaging cameras to determine tire condition, added Kal Tire’s Allan.
Once inspections are made, priority workorders should be made through a tire operations program to tell technicians about the issues and their severity. “Working with AI has made this even more encompassing,” continued Allan, “as this can now be done while the trucks are moving, with workorders created automatically, so technicians can prepare for the change or work.”
PERFORMANCE TRACKING AND DATA ANALYSIS
This brings us to the intersection between tires and that other key meta theme within the mining industry: digitalization. “We continue to see how today’s customer values data and insights more than ever,” said Bridgestone’s Siebert. “Customers today want innovative solutions that deliver real-time updates on every aspect of their operation, with safe and reliable equipment for the site. They also want this in the palm of their hand. Of course, this all ties back to sustainability: getting the most of out of your operations.”
Connected tire management systems “equip mines with mission-critical information to help the mines operate more safely, more intelligently, and more sustainably,” said Michelin’s Adam Murphy. In their infancy, these systems merely gave mines information on tire pressure and temperature to help prevent premature wear and failure. Today, they are “much more sophisticated, using technology like GPS and geofencing, to monitor position, speeds, and routes that may contribute to premature tire wear. Leveraging data between vehicles and tires equips mining personnel with substantial information to strengthen safety, improve overall mine productivity, save on budget, and increase truck availability.”
For Continental, this creates the possibility of intelligent or smart tires, which can be tracked at all time, resulting in greater control of operating lifetimes. Integrated functionality to track tire checks and health status also “allows a more transparent prediction of when replacement and/or rotation is required,” said the company’s Reinhard Klant.
So how does digital tire management work? Klant again: “Sensors inside the tires transmit real-time data about the inflation pressure and temperature in relation to the load cycle of the vehicle. When tires are underinflated or at risk of overheating, warnings can be shown to the driver, via an in-cabin display or vehicle dashboard, as well as to the fleet manager via a web-based application.”
The latest tire management systems may also feature a digital twin of each tire, complete with part number, meaning fleet operators “always know which tire is fitted to which vehicle and in what position,” continued Klant. “On top of inflation pressure and temperature, performance parameters from fleet checks, such as tread depth and tire condition, can also be tracked.”
This captured data “establishes norms and baselines that help mines make better decisions about the tires they are currently using, as well as helping predict future tire requirements more accurately,” explained Goodyear’s Matson. “By tracking performance and other indicators over time, you can enhance the ability to predict when tires will need to be replaced. This drives up efficiency and drives down waste.”
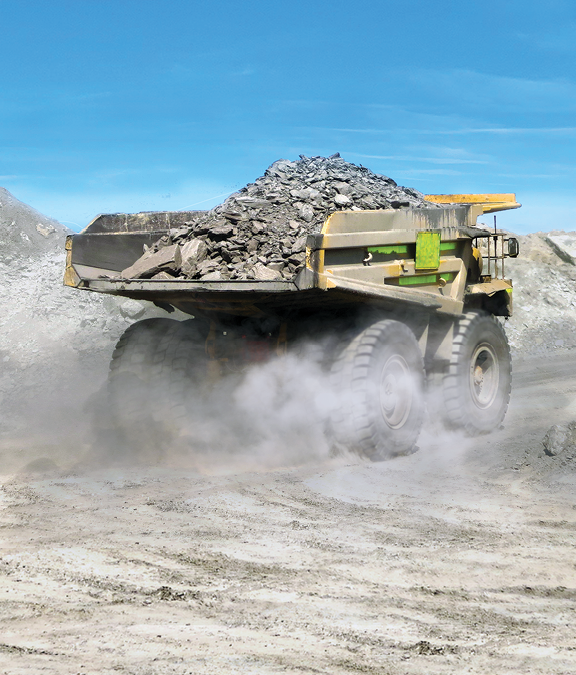
THE THIRD STEP: CLOSING THE LOOP
And this brings us back to where we began the article – to those end-of-life tires. Well, almost. Firstly, we come to re-treading and Allan again: “Repairing tires, or re-treading, extends the life of the tire versus purchasing a new one and can result in hundreds or thousands of additional service hours, lessening a tire’s carbon footprint.”
To measure the sustainability impact of re-treading, Kal Tire developed a proprietary carbon calculator, verified by SCS Global, an international leader specializing in third-party environmental certification. Through this program, the company provides customers with a certificate outlining the GHG savings accomplished with the repair (on tires 49 inches and above) or re-treading of the tire. “We know that these types of calculations are important to customers,” said Allan, “and by using third-party accreditation, we can assure that they are independent and unbiased.”
“The materials used to build a mining tire can easily exceed one tonne in weight,” said Continental’s Reinhard Klant, taking up the theme. “Reusing the largest part of this resource – namely the tire carcass – thus represents a huge step forward in tire sustainability.”
When it comes to tire recycling, there are many different types of technologies available, noted both Kal Tire’s Allan and Michelin’s Murphy. Some are already in use; others are still in the R&D phase. Examples include:
- Shredding and grinding tires
- Ambient scrap tire processing (similar to shredding and grinding)
- Cryogenic crushing: a process of freezing the tyre and then crushing it
- Pyrolysis
- Water jetting
- Molectra: integrates mechanical, chemical, and microwave treatments
- Devulcanization
While technologies change quickly, “we really want to ensure that the entire tire can be re-used or re-purposed to ensure the highest and best use of the elements of the tire,” concluded Allan. Kal Tire currently uses thermal conversion – a process that uses heat and friction in the absence of oxygen to induce a reaction that converts tires into their base elements – in its recycling plant. This process breaks down the tire to its core elements (carbon ash, steel, oil, and synthetic gas), with each of these able to be re-used or recycled in other products. This contrasts with a technology like shredding or devulcanization, when “there is still a portion of the tire that cannot be used and will likely find its way into a landfill.”
MAXAM Tire takes a similar approach to convert tires back into their constituent parts. Michelin, meanwhile, has three active projects on three continents, working alongside customers, to “explore and develop end-of-life tire recycling solutions,” said Murphy. One of these, a project located in Chile, is expected to be operational this year.
However, despite companies being looking seriously at recycling, thanks to an enhanced focus on ESG performance, as well as impending legislation in various countries, there remains a question over how to pay for recycling.
“Regardless of the chosen method, recycling OTR tires is costly and, if there is no regulation, mines can struggle to make the case for capital allocation,” explained Allan. “One way to tackle this may be through accessing mine remediation budgets. Every mine has money set aside for reclamation and eventual closure. The challenge lies in accessing that budget today, so that mines can recycle tires progressively, rather than waiting until closure, when there are thousands of products awaiting disposal. There is an evolution that should happen internally to bring those two value streams closer together.
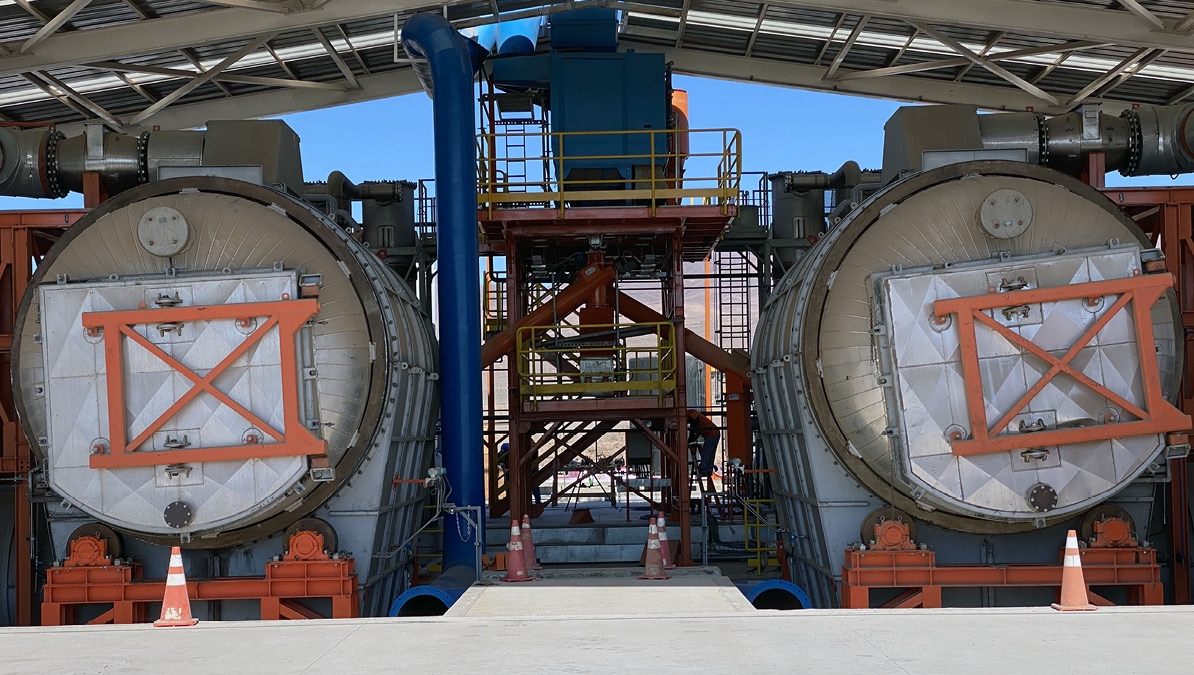
CONCLUSION
The mining industry has “a unique role in enabling a cleaner plant and supporting humankind achieve net zero,” concluded Michelin’s Murphy. With ESG and climate change top priorities for mines worldwide, every aspect of the mine is under the spotlight. This includes mining tires. And as Murphy continued: “our mining customers are expected to grow more quickly and cleanly than ever before.”
The solution, according to Murphy, will lie in “collaboration and partnership.” Fortunately, it appears those involved in the manufacture, supply, and management of mining tires stand ready to assist the mining industry achieve the most sustainable mining tire solutions possible, and thus to continue driving up sustainability standards into the future.
OUR PANEL
- Dave Allan, vice president Canada, Kal Tire’s Mining Tire Group
- Matt Johnson, vice president, MAXAM Mining Group
- Matthew Futrelle, head of business field – Earthmover Tires, Continental
- Reinhard Klant, product manager for Earthmover Tires, Continental
- Eric Matson, manager of Global Field Engineering, OTR, The Goodyear Tire & Rubber Co.
- Adam Murphy, senior vice president, Michelin Mining
- Rob Seibert, president, Off-the-Road, U.S. and Canada, Bridgestone Americas
