High-pressure grinding rolls and vertical roller mills offer several potential benefits to mineral processing operations.
by Jonathan Rowland
Comminution circuit design has traditionally focused on reliability, ease of operation, CAPEX, and OPEX, with AG/SAG and ball mills the longstanding workhorses in mineral grinding applications. “AG/SAG mills played a crucial role in the evolution of mineral processing, as a single mill can replace two or three crushing changes,” explained Greg Lane, principal consultant at Ausenco, a global engineering consultancy. “These mills operate at high capacities while requiring a much smaller footprint than historic staged crushing plants.”
However, AG/SAG and ball mills consume significant energy when treating competent rock. Grinding ore for mineral liberation is the largest energy consumer and contributor to Scopes 2 and 3 CO2 emissions in minerals processing, with a typical comminution circuit accounting for nearly 40% of an open pit mine project’s total energy use. According to one study, gold and copper ore comminution alone may consume 0.2% of global energy.
According to Lane, improved energy and water efficiency targets have “increased interest in energy-efficient dry comminution technologies and pre-concentration/coarse separation technologies” among mining companies. Concurrent moves to enhance the safety of tailings storage facilities (TSF) are compounding this interest, as adopting dry comminution and coarse concentration (e.g., cobbing, coarse particle flotation) processes “can lead to a significant reduction in TSF footprint and water consumption, addressing two of the major environmental concerns associated with mining operations,” Lane continued.
Two dry grinding technologies stand out in discussions: high-pressure grinding rolls (HPGR) and vertical roller mills (VRMs). According to Grant Ballantyne, director at CEEC International, a global initiative highlighting eco-efficient comminution practices, HPGRs are “well established” in coarse, hard-rock grinding applications and “progressing into fine grinding applications in closed-circuit with air classification.” In contrast, VRMs’ current application in hard-rock mining is “limited,” although other sectors have long used them.
“Dry compressed-bed comminution technologies, such as HPGRs and VRMs, typically consume less energy than traditional AG/SAG and ball mills,” said Ballantyne, explaining that an established circuit configuration combining HPGRs with ball mills can reduce total energy consumption by 25% compared to an equivalent SAG and ball milling circuit (Lovatt et al., 2023). “The combination of HPGRs or VRMs with air classification extends the benefits of compressed bed breakage to fine sizes and can potentially reduce energy further. However, the energy consumption associated with the air classification and materials handling systems can significantly erode this benefit.”
Ballantyne also noted that HPGR and VRM circuits are less affected by ore hardness and variability than AG/SAG milling, with “more significant relative benefit” for competent ores. However, wear and maintenance can pose operational challenges for both technologies, increasing costs unless managed effectively. Energy-intensive dry classification can also consume significant energy and erode the benefits. “Unlike classification in wet grinding circuits, the energy used in dry classification circuits can be similar to the comminution energy if the ore is wet,” said Lane. “The challenge is thus to manage the impact of moisture in dry classification and reduce the energy expended by fans used in fine dry classifiers.”
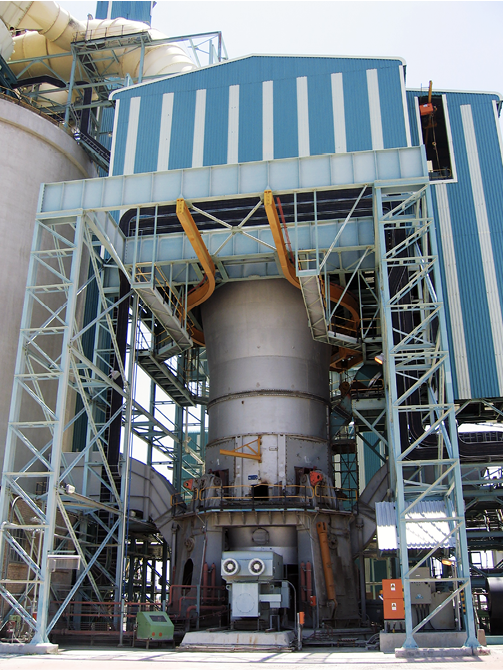
Dry grinding in the mining industry: current potential
HPGR and VRM dry grinding circuits have “similar comminution characteristics,” explained Ballantyne. “Yet the two systems currently lend themselves to different project settings.
The fully enclosed, modular VRM and classifier design has traditionally been applied in finish grinding applications, such as at the West Musgrave copper and nickel operation, where dual Loesche VRM-based grinding circuits are foreseen to process a high-abrasive hard rock ore (P80=165µm) for flotation. On the other hand, HPGRs have historically been used in pre-crushing applications to prepare feed for downstream ball mills, such as the Iron Bridge magnetite project. Their use in fine-grinding applications is a developing area.
HPGR technology “has evolved significantly from its initial applications in raw material processing to playing a critical role in processing high-competence ores,” added Ausenco’s director of Comminution and Processing, Bianca Foggiatto. “HPGR can be a competitive alternative to traditional comminution methods like SAG mills if the ore is competent and energy cost is high. Meanwhile, VRMs have a long history with bulk materials, such as cement and phosphate rock processing, and have recently gained attention for processing various commodity ores, such as lithium, iron, gold, and base metals.”
A VRM can handle coarse crushed material, “producing a single-pass product with a P80 as fine as 20 µm,” continued Foggiatto. “HPGRs can achieve an open-circuit product with a P80 of 10 mm and as fine as 2 mm when operated in a closed circuit with screens, while in a closed circuit with air classifiers, HPGR product size can be further reduced, preparing the material for downstream wet processing.”
VRMs and HGPRs with air classifiers can generate an intermediate fraction, which can “either be recycled for further grinding or directed to dry or coarse particle separation,” noted Foggiatto. For example, in the iron ore industry, this intermediate product can undergo dry magnetic separation (cobbing), with the non-magnetic fraction rejected as tailings, as is the case at Iron Bridge’s HPGR-based circuits. Global VRM supplier Loesche has also developed a flowsheet using its VRM to process the intermediate fraction.
Dry comminution integration into existing flowsheets is “not easy,” said Ausenco’s Lane. “You can integrate them as part of a parallel plant expansion but not within a wet grinding circuit unless there is a relatively dry stream of pebbles or similar material split from the existing plant.”
“As traditional circuits are usually designed for wet processing, retrofitting HPGRs or VRMs into existing circuits often requires significant redesigns of the plant layout,” explained CEEC director Ballantyne. One example is the Cadia gold and copper operation, which installed an open-circuit HPGR to debottleneck the existing SAG mill. “To make the most of the fine HPGR feed, SAG operating conditions required significant changes.”
Ballantyne also noted, “HPGR and VRM vendors are working on solutions to process the SAG mill pebble stream to produce a final product and debottleneck the SAG and ball mills. Meanwhile, Rob McIvor and his team at Metcom Technologies have investigated using HPGRs to replace ball mills on the SAG mill product stream.”
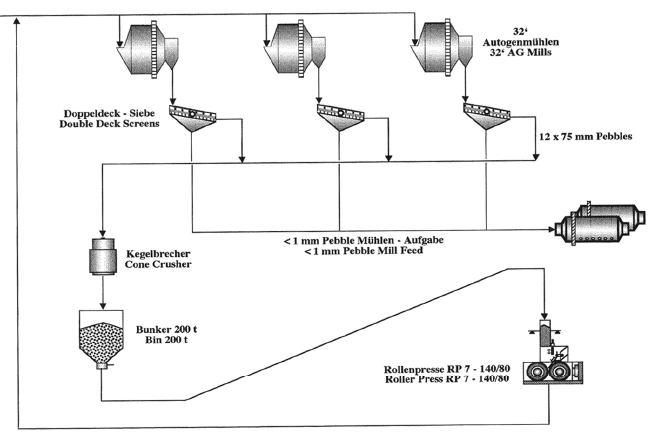
Technology in focus: HPGR
HPGRs originated in the 1980s in the cement industry. They are particularly effective with harder, more competent ores like copper, gold, iron ore, and certain base metals. According to Stephen Skjonsby, process manager – Product Implementation at Weir, a global mining technology supply company, the first North American hard-rock installation occurred during a 15-month trial at the Sierrita copper mine, Arizona, in 1995/96. The first North American production-scale HPGR was commissioned at the Cleveland-Cliffs Empire iron ore mine in Michigan. This installation treated -63.5 mm pebbles at throughputs up to 400 tph from 1997 until the site was idled in 2012.
HPGRs operate by “compressing rock particles as they pass through the operating gap between rolls, which results in interparticle breakage of the rock,” explained Skjonsby. “Balancing coarse and fine material in the feed is critical to optimizing interparticle interaction.
Consistent feed optimizes performance and allows for longer component life. You should also not feed material larger than the operating gap, as oversized feed can result in slippage on the rolls and damaged studs. In modern HPGR, studs on the rollers hold an autogenous layer of crushed fines in place, enhancing interparticle breakage and reducing wear.”
“Control of the feed top size by closed-circuit secondary crushing to reduce risk of oversize material is a common practice in HPGR circuit design,” added Ausenco’s Foggiatto. “Feeding these units with primary crushed or open-circuit secondary crushed feed is possible, but not advisable due to the higher wear and risk of catastrophic stud liner failure.”
HPGR particle size distribution (PSD) is flexible “depending on the recirculating load and the top feed size,” continued Skjonsby. “HPGR-based circuits in hard rock applications have typically been employed to generate an optimal ball mill feed (usually 4-7mm), although we have sometimes used product recycling or air classification to generate a final product below 1 mm.”
Skjonsby also mentioned the generation of “microcracking in fine HPGR product, which results in decreased power draw in downstream mill circuits,” although other of our experts consider this a somewhat debatable area.
According to Nick Logan, product manager for HPGRs at Weir, this latter application has seen HPGR used in flowsheets alongside vertical stirred mills and coarse particle flotation (CPF) to reduce energy consumption in mineral recovery. “HPGRs prepare the feed for the stirred mill. The mill preferentially liberates the target material at the desired recovery size, while CPF allows the flotation of larger particles than is conventionally possible. This combination can save over 30% of the energy consumed versus a traditional SAG-ball mill circuit.”
Technology in focus: VRM
Unlike HPGR, VRMs have yet to penetrate the mining industry significantly. “Although the mining industry has been reluctant to adopt VRMs, there have been some successful applications,” said Stefan Baaken, managing director of Loesche Australia Pty Ltd. “The first Loesche VRM in hard-rock mining has operated successfully for 25 years at the Foskor phosphate operation, processing a low- to medium-abrasive ore with an average Bond Work Index of 25 kWh/t. We have also supplied a phosphate rock grinding application in Kazakhstan, a gold grinding application in Turkey, and the West Musgrove copper and nickel grinding plant mentioned earlier.”
VRMs consist of a rotating grinding table to which rollers are attached. “Ore is fed into the center of the grinding table and moves outward under centrifugal force into the path of the rollers,” explained Dr. Carsten Gerold, Loesche’s senior manager for Ore and Minerals Technology. “Breakage is primarily induced by feed compression between the rollers and the table, supported by significant shear. The advantage of this process is that, through multiple contact points, applying pressure from all sides, there is a high probability of initiating cracks at the mineral boundaries and other weaknesses.”
The compressed ore continues moving to the grinding table’s edge before falling into the process air stream. “Finer particles are pneumatically transported upwards to the air classifier, ensuring any particles at target size are not overground,” continued Gerold. “The combination of the classifier’s rotational speed and the airflow’s inward speed determines the cut point with target-size material passing through the classifier’s vanes and leaving the mill to be collected by a baghouse filter. Coarse classifier reject returns to the center of the grinding table via the grit cone for further processing.”
The rapid grinding and classification achieved in a VRM produce a “steep cumulative particle size distribution with a low amount of ultra-fine material,” concluded the Loesche expert, who also noted that various studies have shown “compressive in-bed comminution improves mineral liberation and thus delivers a higher recovery rate than conventional milling.”
As a “rule of thumb,” the harder the ore, the greater the energy saving, said Baaken; however, “we have not found an ore that is unsuitable for our VRM, having conducted pilot campaigns with over 250 different ores with Bond Work Indices ranging from 3 kWh/t to 28 kWh/t. In almost all cases, the higher degree of mineral liberation combined with the steeper product PSD resulted in higher recoveries at lower operating costs and coarser liberation sizes. For all ores tested with feed moistures <5%, the VRM proved more energy efficient than a conventional mill. We have also seen benefits to the flotation process when grinding polymetallic ores.”
VRMs are also less sensitive to changes in ore hardness than conventional milling technologies. “Harder ores are usually more responsive to compressive and shear grinding, as they tend to be more brittle,” explained Gerold. “Hardening of the ore over time thus creates less impact on throughput in a VRM compared to an AG/SAG mill and can be easily compensated for by increasing grinding pressure. The Loesche VRM, for example, is equipped with a self-adjusting process control system that automatically adjusts the system to changes in ore hardness and mineral composition.”
According to Baaken, in “most flowsheets today, our VRM is already an alternative to SAG-ball mill circuits.” Due to the VRM’s high comminution ratio, the tertiary crushing stage can be avoided, with the milled product feeding directly into downstream processes. “The main difference is the need for a repulping stage to prepare the dry VRM product for flotation, which allows us to control and optimize the pulp density to maximize mineral recovery.”
On a more cautious note, Ausenco’s Lane noted that “wear and maintenance costs in a hard-rock VRM-based comminution circuit are poorly understood, as few plants are in operation using VRMs. Those circuits that are operating tend to process low-abrasive ores.”
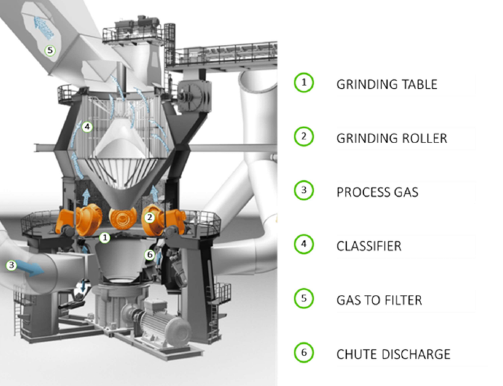
Impact on downstream flotation and tailings management
Dry comminution technologies have “the potential to improve recovery through leaching and flotation,” said CEEC’s Ballantyne. “Improved leaching extraction has been observed in HPGR products. Meanwhile, three potential actions of dry crushing may improve flotation recovery: eliminating galvanic corrosion of steel grinding media in wet mills; efficient classification providing a greater proportion of material to the floatable size fractions; and reduced over-grinding of high-density components due to a lower density bias in dry classification.”
Dry comminution also benefits tailings management, as “less material flows to downstream wet processing, reducing the volume of wet tailings and thus minimizing water losses,” added Ausenco’s Foggiatto. “Producing dry or coarse tailings also enhances stability for dry stacking.”
Challenges of dry grinding
Moisture content is perhaps the biggest challenge to dry grinding, as it “negatively affects processing performance and results in decreased processing capacity,” explained Foggiatto. “Additional energy is required for drying the feed, which offsets any energy savings these technologies deliver.”
According to the Ausenco engineer, HPGRs have “some tolerance to moisture;” however, excessive moisture content adversely affects specific energy consumption and can reduce the operating gap, resulting in lower throughput and decreased efficiency while creating sticky conditions that hinder material flow and increasing wear on the equipment.” Meanwhile, VRMs “face limitations when handling materials with high moisture content due to their internal air classification process and impact on ductwork. Excessive moisture leads to fines agglomeration, disrupting the classification process, reducing overall efficiency, and resulting in uneven PSD and challenges in achieving the desired product fineness.”
A high clay content in the ore can also “pose difficulties,” continued Foggiatto, “leading to a reduction in HPGR operating gap and impaired comminution efficiencies.” Although grinding raw materials, such as bentonite, a clay material that serves as a binding agent in iron ore pellet production, is a common VRM application, clay in the VRM feed “can lead to fine particle agglomeration, clogging and flow issues, and higher energy consumption.”
While dry comminution circuits “offer advantages in reducing energy consumption and steel consumable costs (no grinding media), work remains to validate the benefits of integrating coarse separation stages after dry comminution,” concluded Foggiatto. “A robust test program is essential, considering the performance of coarse separation and the effects on downstream processes such as dewatering and tailings stability. As with any crushing equipment, key challenges include operating costs and downtime, influenced by wear component life.”
The future of dry grinding
The future of dry comminution technologies is “promising,” summarized CEEC’s Ballantyne, “especially as the mining industry increasingly focuses on sustainability. As water becomes a more limited resource and energy efficiency becomes a higher priority, I expect technologies like HPGRs and VRMs to gain broader adoption. However, this is contingent on success at operations such as West Musgrave and Iron Bridge. With advancements in wear-resistant materials and improved control systems, these technologies will likely see increased integration into both greenfield and brownfield projects.”
Reference
Lovett et al., 2023. ‘Trade-off realities in HPGR vs. SAG milling – a practical comparison of Tropicana and Gruyere comminution circuits’, paper presented at SAG Conference 2023, 24-28 September 2023, Vancouver, Canada.