North American Mining takes a short walk through some recent topics in underground mine safety.
By Jonathan Rowland
Recent mining fatalities in the U.S. mining industry have involved vehicle collisions, electrocutions, falls, equipment rollovers, and drowning. Although fewer in number thus far this year compared to the same time last year, “fatalities, injuries, and illnesses are preventable, and one fatality is too many,” an MSHA spokesperson told North American Mining. It is thus important to “prioritize identifying and eliminating hazards that can cause injury or illness.”
New technologies such as AI and machine learning may offer opportunities here, “enhancing analysis of real-world data and identifying patterns and trends in ways that allow more effective targeting of resources,” according to the MSHA spokesperson. “Of course, we need to confirm the reliability of AI and machine learning in the challenging and sometimes unpredictable mining environment.”
As Florent Garin, senior product manager at Hexagon, noted, there is a more fundamental roadblock to using AI and machine learning to improve underground mine safety. “Some underground mines are still not equipped with basic technologies such as communication, infrastructure, production management tools, fleet management systems, and asset tracking solutions.”
This is changing, however: “I have seen a recent shift in the mentality of underground miners towards prioritizing technology as a common denominator across the entire mining operation, rather than isolating it in a specialist department,” continued Garin. “Digital technology is evolving into part of the business model rather than a peripheral consideration. This evolution is important because, to make the most of AI and machine learning, I believe mines must first harness the potential of the foundational technologies available today.”
Communication and connectivity
“Safety in underground mining requires the best possible information about real-time conditions,” explained MSHA’s spokesperson. “Reliable communication and connectivity for real-time monitoring is thus critical to ensuring safety measures and decisions address current and ongoing circumstances in the mine.”
“Communication and connectivity play an important role for emergency management underground,” agreed Hexagon’s Garin. “Infrastructure such as WiFi, LTE, and leaky feeder technology enable data transmission back to the surface for analysis; it’s also necessary for locating people.” However, given the complexity of the underground environment and the challenges of ensuring reliable, continuous communication, technologies that do not rely on communication infrastructure, such as peer-to-peer collision avoidance systems, have a vital role.
Underground mines are also beginning to “connect the dots” and understand that “we are rarely solving for a single problem, but for an array of them,” continued Garin. “This view can justify higher investment in technology for greater rewards and solutions that can be scaled. Two technologies I believe must be explored for underground mining are vision- and radar-based systems. These can be complementary and help solve safety and operational problems.”
Atmospheric monitoring
Mine operators “must be vigilant about atmospheric and dust monitoring in underground mines because of fire, explosion, and preventable health risks to miners,” noted the MSHA spokesperson. “We know these risks are always present in mining environments and pose serious risks to miners’ health and safety. Continuous monitoring is a critical tool in identifying and preventing hazards. For example, mine operators can use engineering controls to prevent miners’ overexposure to airborne contaminants and use further sampling and environmental evaluations to monitor exposures.”
The recently finalized MSHA rule protecting miners from exposure to respirable crystalline silica discusses advancements in engineering and sampling technologies. It notes that several commentators (including the National Mining Association) on the earlier proposed rule had mentioned the need for sampling devices with real-time or new real-time sample analysis capabilities for respirable crystalline silica.
MSHA is “encouraged by various stakeholders’ efforts to promote the safety and health of miners through the use of advanced technologies in atmospheric and dust monitoring,” the spokesperson said. The rule also recommends that operators “stay aware of and evaluate advances in technologies to identify control options that facilitate compliance, improve mine operator and miner awareness, and improve miner health” (Section VII A 2 b).
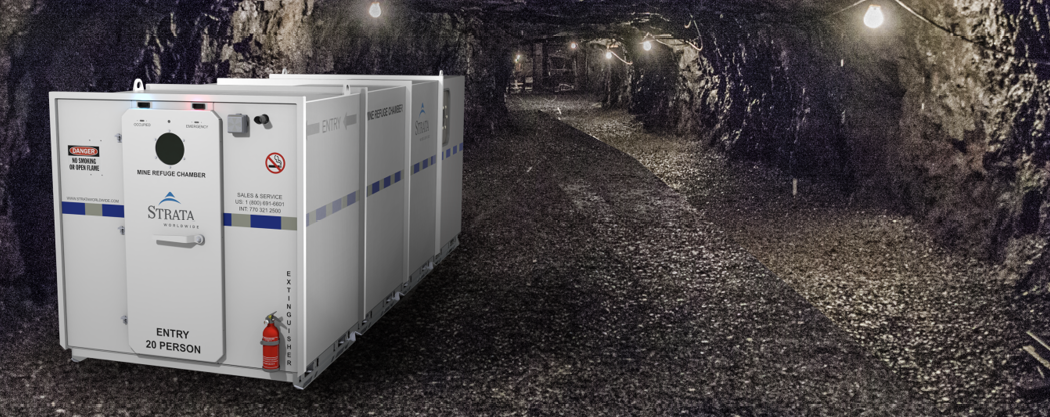
Refuge chamber developments
Strata Worldwide recently introduced a new economical and versatile lightweight emergency refuge chamber for mining and tunneling: the Strata Emergency Refuge Chamber Modular (ERCM). Designed with a series of attachable sections that can be assembled pre- or post-delivery, the ERCM helps overcome handling and shaft-size restrictions while offering mines the opportunity to order chambers to existing requirements and add capacity as needed later.
“A significant benefit of this new, lightweight modular design and subsequent manufacturing economies is that the chamber provides greater flexibility and price competitiveness for the customer,” explained Dave Maust, general manager of Refuge Chambers at Strata Worldwide. “Although some premium accessories available on Strata’s traditional chamber may not be available on the ERCM, the uniform, modular design enables us to inventory the modules, which allows for a quicker production turnaround and shorter lead times for the assembled chamber.”
Modules include:
- Technology module. The rear section contains essential systems and components, including the Strata ActiveAIR breathing air system, batteries, power station, air conditioner, air cylinders, and the optional computerized Strata human-machine interface (HMI). The HMI is a touch-screen user interface for real-time monitoring and control of chamber components, systems, sensors, and communications.
- Seating module. The middle section has seating for six people and modules can be added or removed to adjust capacity at ordering or later.
- Entry module. The front section includes the entry door, emergency lighting, siren, and fire extinguisher. The standard entry module leads into the main chamber compartment and seats six people.
- Airlock entry module. An airlock entry is used when a safety airlock is needed. This airlock module comprises a main entry door with a secondary interior door that leads into the main chamber, reducing air contamination entering the main chamber. An optional purge air system is available to flush the airlock before opening the secondary door.
A collaborative approach?
Ultimately, relocating people “away from risk is the goal,” said Hexagon’s Garin. “Will we fully achieve it? Regulations and the costs associated with having human operators in underground environments will impact this. I imagine that some deeper operations will likely lead to fully teleoperated and autonomous ways.”
Garin concluded with optimism: “These are exciting times for underground mining. We are seeing a big push to bring solutions rather than products to the challenges faced by miners. It is up to technology companies like Hexagon to embark on a journey with mining companies to help solve these challenges.”
Our MSHA spokesperson echoed this collaborative message: “The entire mining community – MSHA, miners, operators, and labor unions – must work together to prevent accidents and occupational illnesses at mines because, when the mining community works together, miners are safer and healthier.”