Maintenance: is there a secret to success? NAM wanted to know, and opened up the floor to three companies from the core sectors of surface mining infrastructure – trucks and conveyors – to try to get the answers.
By Donna Schmidt
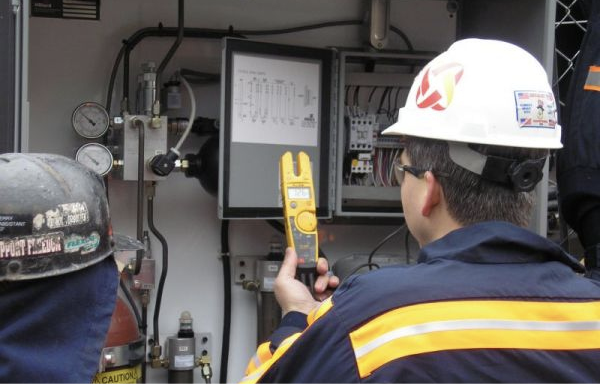
It seems like the ever-elusive answer to a key question: how can surface mining be more efficient? There are many different ways to answer it, but at the heart of it all is maintenance. Without it, the operation does not, well, operate. Headaches arrive, money is lost, and bottom lines get battered and torn.
We began our conversation with the polling of several companies from different facets of the industry on what the most crucial elements were to them – and the responses were as varied as the work the polled companies do each and every day.
One of the first to react to this roundtable question, Hilliard Braking Systems, offered what is perhaps at the core of best practices: preventative maintenance. Hilliard, which produces motion control and filtration systems such as conveyor braking, clutches and more, said its BBH3 Smart Braking System is an example of these features. It offers the operator notifications on a myriad of information, from upcoming service needs to needed maintenance. Oil condition, temperatures, filter life and replacement timing are also available in real-time whenever it is needed.
“Performance, reliability and value are at the heart of what we do at Hilliard,” according to Hilliard Marketing Manager Rob Doud.
“While our line is fail-safe and we respond to support needs quickly, having these details at the ready offers the user, our customer, allows them to determine what’s best for their application and keep a steady eye on their preventative maintenance program.”
Hilliard’s services include commissioning, start-ups, and spare parts, but also annual inspections, training and emergency services. It also often works with its clientele to research and test products in a lab-tyle capacity for a specific application.
“We welcome challenges,” Doud added. “The only way to reach that mutual goal of optimization is to be flexible.”
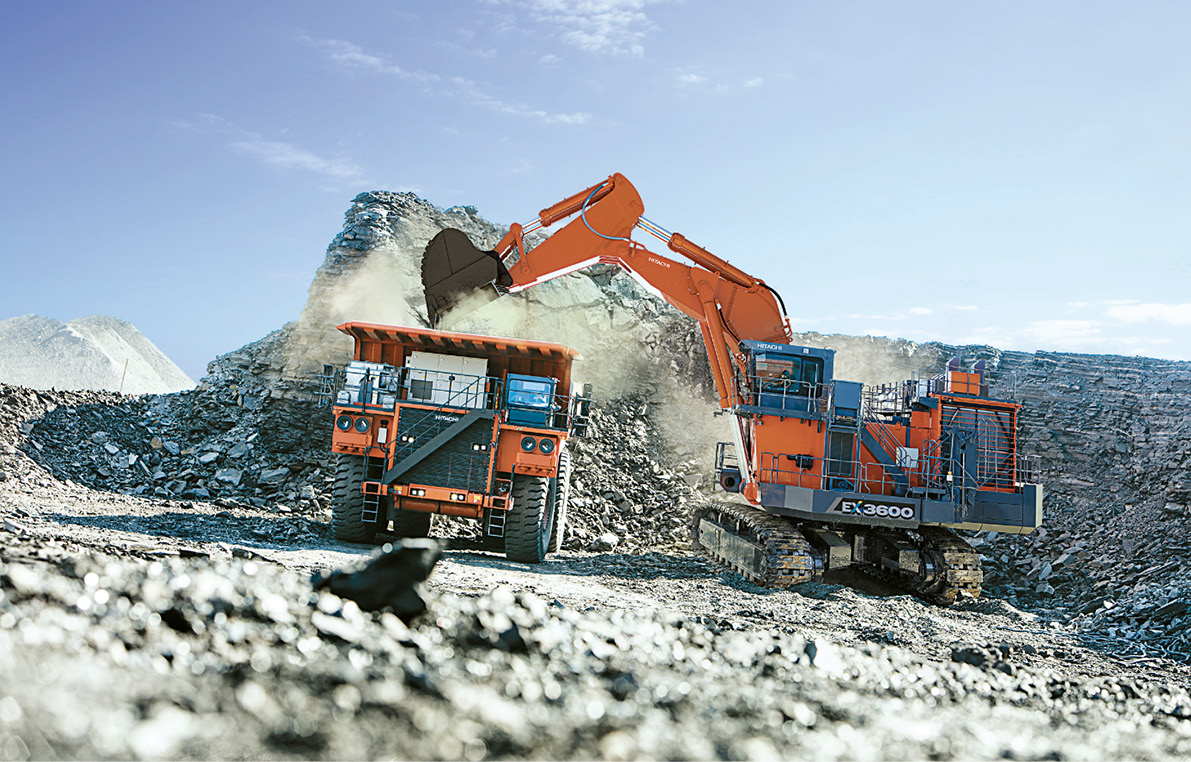
The three prongs of success
NAM also spoke with Babliton Cardoso, Sr. Director of Mining at Hitachi Construction Machinery Americas, who said the top three most significant elements of surface mining maintenance are design, maintenance guidelines adherence set by the manufacturer, and proper operation techniques.
“It starts with selecting the right equipment for the operation, which directly impacts maintenance requirements,” Cardoso said, pointing out that the OEM will analyze the operation beforehand to ensure the chosen machines are an appropriate match.
Next, the mine should follow all manufacturer maintenance recommendations to ensure maximum uptime. Finally, optimized surface mining maintenance relies on proper machine operation.
There have been a few trends over the last decade or so, and some still developing, Cardoso noted, that are setting benchmarks for the future.
“Machine communication is becoming increasingly sophisticated. [Our] haul trucks and excavators employ advanced AI techniques to diagnose and prevent issues that could cause downtime…both on the machine itself and through Internet of Things (IoT) cellular and satellite connections (ConSite).”
ConSite, he explained, closely monitors the entire operation status of a machine to improve its overall performance and increase availability and efficiency, sending monthly operational reports and notifying the user of emergency alerts to ensure optimal machine operation.
Another trend is the growing environmental focus on enhancing efficiency, fuel economy and reducing CO2 emissions, Cardoso said.
“The new machines are more efficient, such as [Hitachi’s] EX3600-7 excavator, which offers a 5% increase in production while using up to 8% less fuel than the previous model. Improvements in hydraulic system design are key to this improved efficiency.”
When asked if automation is having an impact, or could at some point, on maintenance, Cardoso said it depends. “Various technologies, including cylinder stroke end control and auto-leveling, as well as more advanced features like remote operation and autonomous haul systems, significantly enhance operational efficiency,” he said.
“For safety, there are systems like avoidance detection, machine guidance, forward collision alert and operator monitoring (SmartCap). The SmartCap is a wearable technology that asses real-time operator fatigue levels and monitors for oncoming microsleeps that create safety hazards. Improving operations through automation generally leads to better maintenance.”
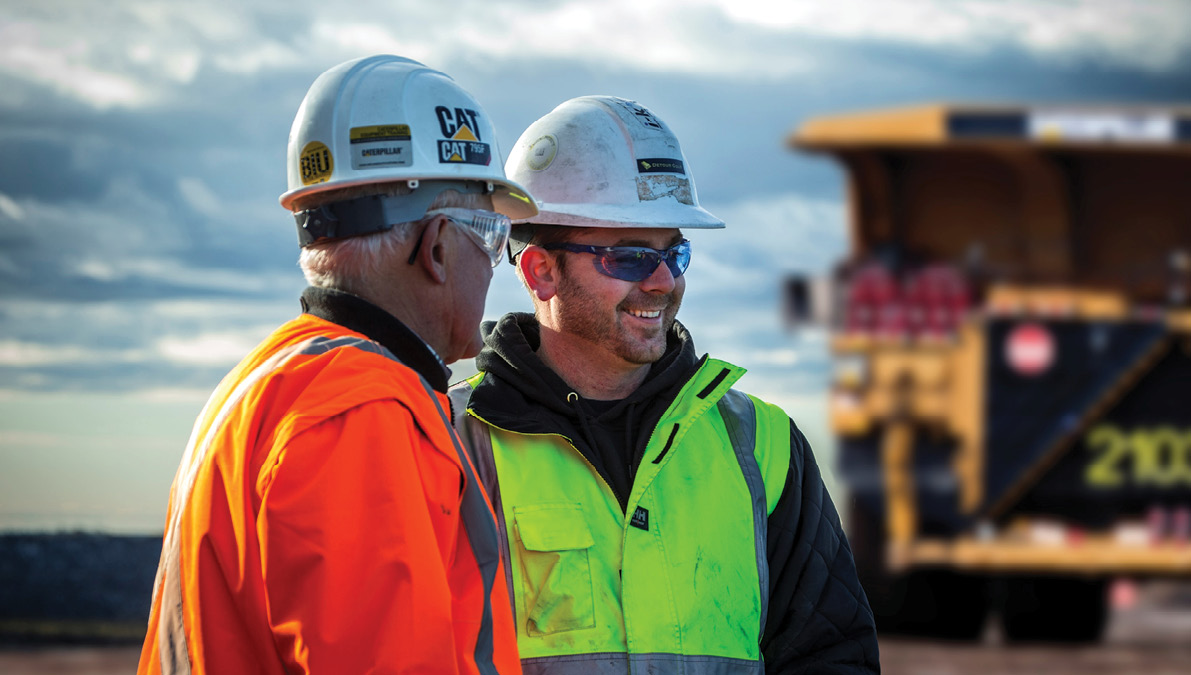
Integrating problems and solutions
A lesser-known area of Caterpillar’s capabilities is Cat Job Site Solutions, which integrates all areas of the Caterpillar and dealer organizations and works hand-in-hand with mines as well as quarries and construction sites to focus on what it called core competencies: productivity, equipment, safety and sustainability. Additionally, its goals for mines are to reduce downtime, minimize unplanned maintenance and, in the end, up total productivity.
Among its safety services, by the Caterpillar Safety Services team, are assessments and workshops, digital learning, training programs and coaching and consultancy. It has put that team in place, it said, to address the main “aches and pains” of operations, such as complacency, underreporting events, repeat and serious incidents, equipment damage and plateaued results.
“[A mine’s] challenges, and therefore the ideal solution, vary by size, by fleet, even by machine component. Our approach is scalable and customized to deliver exactly what you need – nothing more and nothing less,” the OEM explained.
“When we deliver a solution, we’re doing more than encouraging [a customer] to follow best practices; we’re executing those best practices ourselves, on [their] behalf. We’re continually innovating to find ways to deliver additional value through the solutions we provide.”
As an example in the surface maintenance realm, Cat Job Site Solutions pointed to a project it worked on alongside a large mining company that was seeking ways to maintain high machine uptime required to meet demand and also monitor machine performance and health for that fleet.
The OEM’s proactive maintenance solution was the VisionLink web-based machine fleet monitoring technology for the measurement of individual machine productivity and data gathering. Among its data collection areas: production volumes per machine, idle times, fuel consumption and operator capability; Caterpillar’s team also examined maintenance planning, oil sampling and fleet operation. What started at one site now covers the undisclosed customer’s five operations and a total of 25 machines.
The customer’s response was positive and, according to Caterpillar, is why its Job Site Solutions team exists.
“Through Cat Job Site Solutions, our equipment fleet is definitely achieving higher productivity, and fuel consumption is less,” the customer’s industrial performance director said. “We are also seeing less machine downtime due to our ability to be proactive on maintenance.”
With another client, a multi-site mine, the goal was to reduce unplanned maintenance costs for 13 of its Cat machines. The result: a 9% jump in planned maintenance and a 2% rise in physical availability.
“Recognizing that unplanned maintenance can cost almost three times as much as planned maintenance, the multi-site mine reached out to its local Cat dealer and Cat Job Site Solutions for help with technology execution, machine condition monitoring, comprehensive reporting services, reducing unplanned maintenance costs and increasing planned maintenance.”
“[We] recommended a custom solution that included a combination of technology, data analytics and a condition-based maintenance strategy applied to their equipment to help boost the performance of their loading and hauling fleet. The solution included condition monitoring coaching and on-site technical support,” the company said.
Cat Job Site Solutions and the dealer team met weekly with site personnel to review data, answer questions and review the alerts and trends from machine health data.
They then coached and consulted with the site to understand what the data was indicating, which gave the site a greater ability to plan and perform preventive maintenance and inspections of their assets to ensure better health for critical asset elements such as struts, tires, air filters, body shimming, auto lube system and contamination.