What makes a reliable mining chain and chain supplier? They may not be questions you often think about. But choose wrong and the implications can be severe. North American Mining spoke to two mining chain manufacturers about chain selection, operation, and maintenance.
By Jonathan Rowland
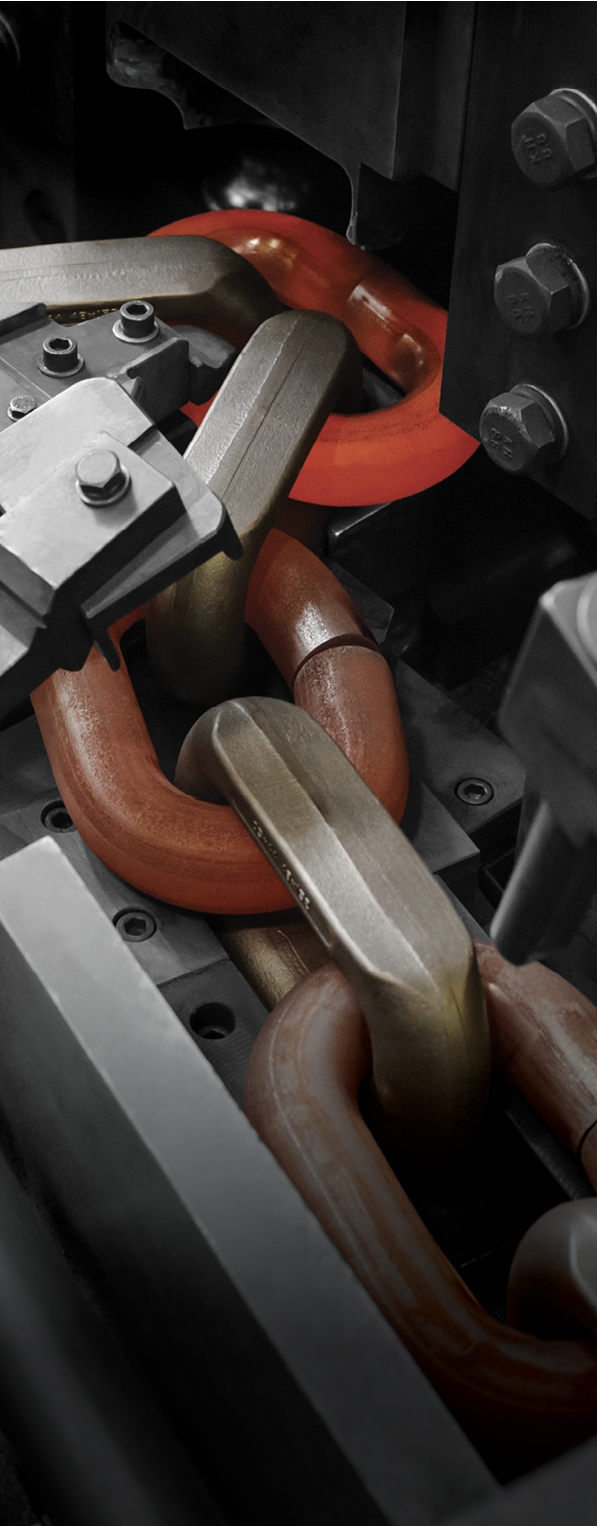
Chains are a crucial part of various underground mining equipment, with each application requiring chains of “different technical parameters and characteristics,” said Aleksandra Tilszer-Sowa, deputy director for the U.S. market at FASING SA, a manufacturer of high-strength round and flat link chains. Based in Poland, FASING is present in the North American market via its subsidiary, FASING America, and specializes in chains for longwall mining equipment.
“Wherever high strength and durability are needed, chains are the best choice,” added Tilszer-Sowa’s colleague, Mateusz Bik, vice president and export and foreign investment director. A poor-quality chain – on the other hand – can bring a mining operation shuddering to a halt.
“Do not believe all chains are equal because they look similar,” said Ray Hensley, director of Business Development at Renold, a supplier of shuttle car, feeder-breaker, and other industrial chains. “Your chain manufacturer’s experience, build specification, and reliability will affect your operation. Using inferior chains risks impacting a mine’s overall performance and bottom line.” “Although in the total purchase value, the chain represents only a small fraction of total equipment cost, it is crucial for uninterrupted operation,” agreed FASING’s Bik. “Any chain replacement or repair caused by breakage thus generates huge costs in unplanned downtime for a mining operation.”
A chain you can rely on
How then should mines approach the selection of a chain and chain supplier? FASING’s Tilszer-Sowa began the discussion by quoting her company’s motto: “there are no perfect chains that meet all requirements. But there are chains that are perfectly suited to specific conditions.”
“The basic criteria for chain selection are purpose, application, and the associated nature of operating conditions,” explained Zofia Guzy, vice president and technical director at FASING. “Selection properties (chain grade) are thus determined with reference to the recommendations contained in equipment technical documentation, the environmental conditions in which the chains/chain assemblies will be operated, and relevant industry regulations.”
The result is that chain selection “requires an individual approach and analysis” to ensure chain properties deliver the performance needed,” continued Guzy. For example: mining applications often require high-grade, high-strength chains that maintain appropriate chain link ductility to avoid breakage in even the harshest conditions. “Depending on the application and mining conditions, we recommend chains in the relevant quality grade based on the requirements of relevant standards, e.g., DIN 22252 and DIN 22255.”
If you are not familiar with these standards: DIN 22252 is the standard for round steel link chains used in chain conveyors, bucket elevators, and mining equipment, and specifies requirements for the design, selection of materials, test methods, and working forces. DIN 22255 is the associated standard for flat link chains, which are used when the equipment profile does not allow the use of round link chains according to DIN 22252 of the same nominal size.
The tailored approach to chain selection is also what drives new product development. “Our innovations are driven by the needs of our customers,” concluded Guzy. “Most often, these products are custom-made solutions, engineered in-house and certified in our metallurgical and testing laboratories. It is this knowledge, experience – we have 110 years in the mining industry – and resources that allow us to create products best suited to our customer’s need.”

Photo: FASING S.A.
Selecting (and manufacturing) an appropriate chain is only part of the picture, however; chain reliability also comes down to proper operation. Guzy suggests the following general guidelines:
- Always run equipment according to its technical and start-up documentation.
- Regularly check the sprocket sockets. Excessive wear here will result in excessive wear of the chain links.
- Use and monitor proper chain tensioning.
- Ensure the chain is well paired and operated at the correct voltage.
What to look for in a chain manufacturer
When evaluating a chain manufacturer, mines should be looking for a company that “uses appropriate-quality materials, precision manufacturing processes, and heat-treatment techniques,” said Renold’s Hensley. “The manufacturer should also preform quality verification to ensure the chain will deliver appropriate strength and wear performance.”
For example: according to Hensley, Renold’s engineered chains are “explicitly designed to perform optimally in the harshest conditions. Sidebars are heat treated to provide strength, while maximizing ductility to handle higher shock loads. Pins and bushings are engineered and heat treated to provide longer service life and combat corrosive wear conditions. Where necessary, corrosion-resistant plating can further increase a chains’ life.”
“Chain selection is best done as a collaboration between chain supply and the mine,” added FASING’s Tilszer-Sowa. “It always takes two to find the best solution and provide the best product for a given mine. In this respect, we truly appreciate the cooperation and openness of our U.S. customers.”
“We are impressed with the U.S. market, productivity, and attitude to success,” agreed Tilszer-Sowa’s colleague, Mateusz Bik. “It is hard to find this elsewhere in the world on such a scale. It makes it very enjoyable to work here. There is commitment at every level of mining companies, whether it is the operators at the coal face, managers, or directors, because they all have one goal: to mine as efficiently and economically as possible in a safe manner. In such conditions, our work is pure pleasure!”
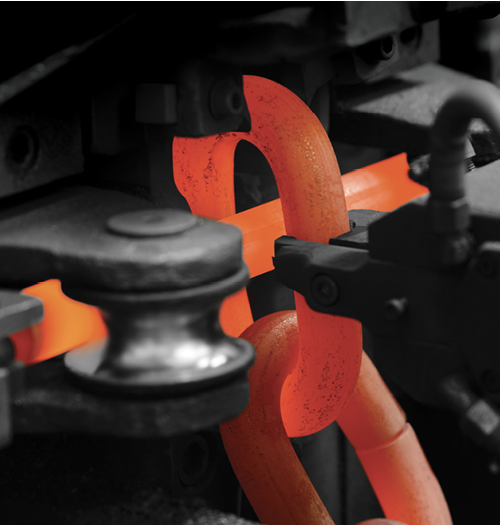
Considering corrosion
“Corrosion is obviously one of the causes of wear during chain operation,” noted FASING’s Guzy. “But chains can also be exposed to corrosive conditions during transport and storage, e.g., if stored improperly underground during equipment assembly.”
According to Guzy, there are several ways to protect against corrosion. “One is the use of a tectyl-based lubricating coating, together with an agent that has hydrophobic properties and thus prevents condensation corrosion. Another way is heat-chemical treatment after the basic production process – so-called ‘hot-dip galvanizing.’ During this process, the steel chain is coated with zinc. When exposed to the atmosphere, the zinc reacts to form a hard zinc carbonate layer that protects the steel from corrosion.”
FASING also uses “inlet protection of chains, especially plow chains,” continued Guzy. “This uses a corrosive-resistant agent based on zinc and its compounds, which forms a durable, flexible coating that is resistant to abrasion and weathering. Depending on the strength class of the chain, different protection agents – or a double concentration of them – can be used.”
Securing and protecting the surface of mining chains not only protects against corrosion; it also allows “better run-in of the chain by reducing friction between the links and effectively reduces the chain’s resistance to movement, especially during the initial period of operation,” concluded Guzy.
Chain maintenance
The most important advice when performing chain maintenance is “to use appropriate tools to install chains properly,” said Renold’s Hensley. “In addition, never modify chain components for easier field assembly: breaking out the grinder negates the carefully engineered and manufactured high-pressure press fits required to optimize chain life.” And again, the benefits of collaboration were highlighted: “Work with your chain manufacturer to outline the correct maintenance program.”
When conducting maintenance, “ensure appropriate preparation to keep your team safe,” continued Hensley. “Always remove all tension on a chain before disconnecting it, and be sure to fully support it, so there is not uncontrolled movement. As with installation, you should always use the appropriate tools for chain assembly and disassembly, and you should never be tempted to re-used chain components.”
On lubrication, “mines are best served by contacting a professional lubrication company to assist in selecting the best option,” said Hensley. “Chain manufacturers typically lubricate chains with a light rust inhibitor before shipping to protect them during transport, but after installation, you will want a lubricant specified to handle the applications specific demands.”
Mines in the U.S. are “well-oriented on how to take care of their chains,” concluded FASING’s Bik. But if there is any doubt, the message is again: collaborate! A chain manufacturer “should be there to work together with the mine to achieve success and answer any questions.”
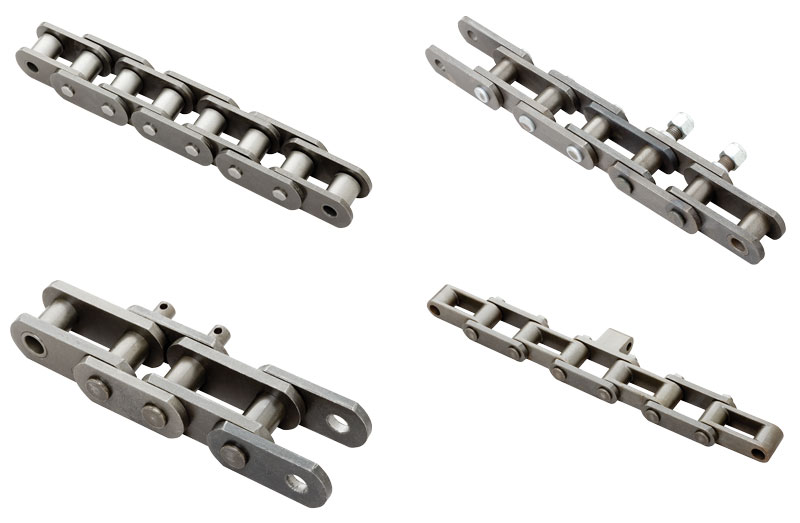