A look at the design and maintenance of mechanical conveyors for this vital American mining region.
By Dan Baxter
Several factors play into the safety, reliability, and maintenance requirements of mechanical conveying systems. And while all mining and mineral processing operations are more demanding of their mechanical conveying equipment, handling iron ore and taconite in the Iron Range requires special consideration.
The challenging characteristics of iron ore and taconite, paired with the often-inclement weather of the Midwest, mean conveyors in America’s iron belt must be especially robust, requiring buyers to do their homework in designing a system and selecting a vendor.
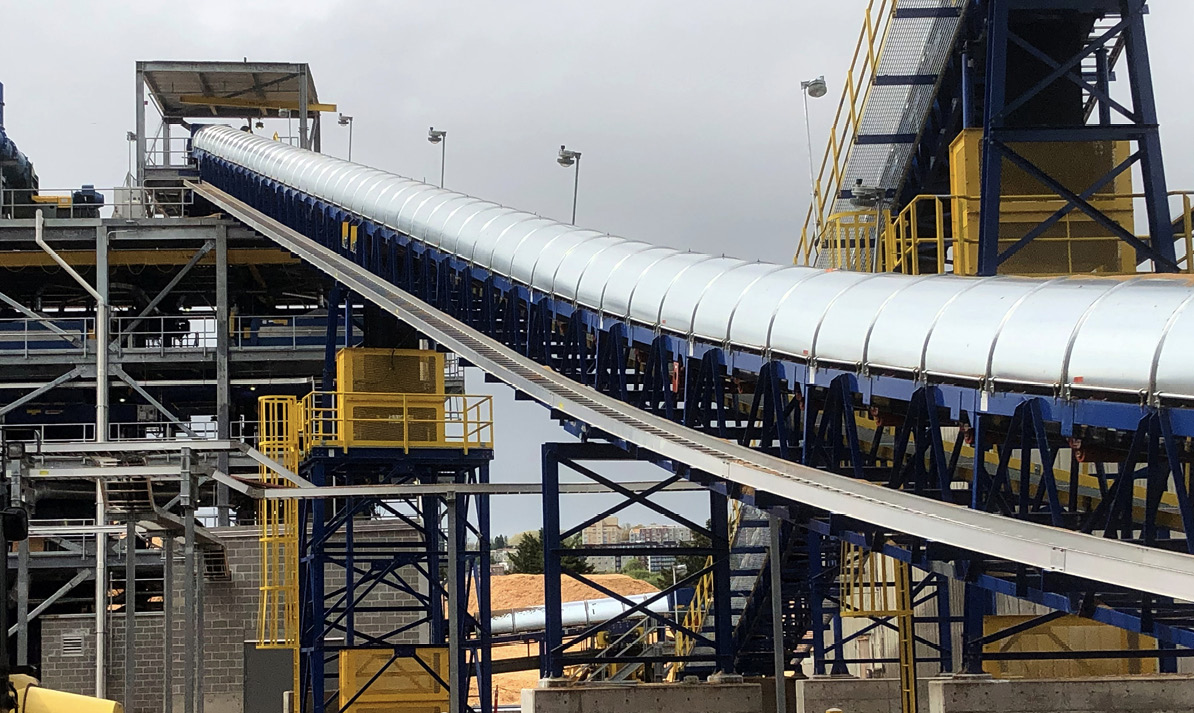
Top factors to consider
The most important factors to consider in engineering a handling system for the Iron Range, which translate to a number of essential upgrades, are summarized here.
Safety
Safety is a top priority when it comes to conveyors, with guarding required throughout the system anywhere there are moving parts: head and tail pulleys, take-up assemblies, and more.
Guarding protects employees from pinch points and moving parts that hold an inherent potential for injury. Guarding requirements and compliance are managed by the Mine Safety and Health Administration (MSHA), though it’s important to note that additional guarding options beyond what MSHA mandates are also available.
Beyond required guarding, additional measures can be taken to further improve the safety of the system; closed-end housing bearings are an improvement on the rotating shaft extending beyond the housing. Return idler guards can also be implemented to block off nip points and serve as a catch basin in the event of an idler failure, protecting employees that might be passing by below. E-stops and pull cords provide added protection in the event of an issue.
Dust management, discussed below, is another important consideration when it comes to safety, as dust can be harmful to employees, as well as present a risk of combustion.
Durable construction
Durable construction is a necessity for iron ore miners, with implications on every system component.
Frames
Both iron ore and taconite are heavy and may require special structural analysis and the use of heavy-duty frames. Heavy-duty frames are especially important if drip pans are employed; drip pans have the potential to fill up with material, adding extensive weight onto the already-heavy load the conveyor is under. Walkways, platforms, and cable trays must also be considered during the structural analysis of the equipment.
Drive assemblies
The heavy weight associated with iron ore and taconite also demands a more robust drive assembly, with IEEE841 motors and direct drive reducers (instead of high-speed v-belts) recommended. The use of a soft-start package or fluid couplings to assist in starting a conveyor under a full load may also be desirable.
Idlers and pulleys
Heavy-duty construction is required of idlers and pulleys as well. CEMA D and E idlers are most commonly employed for use with iron ore products due to the anticipated weight. Shaft size and shell thickness increase progressively from CEMA C idlers to allow for higher load ratings.
Pulleys are available in three different classes: CEMA/heavy duty, mine duty, and engineered class, with each class increasingly robust. Each class also involves special design considerations regarding the rims and end discs, where stresses on the pulley are highest. Engineered class pulleys are custom engineered by the pulley manufacturer based on calculated belt tensions. This class of pulley includes a completely machined end disc to eliminate welds near the hub.
Feed areas
Feed areas also require special attention to withstand impact loading; load areas are often fortified with impact beds or CEMA E rubber disc impact idlers. Both approaches provide additional support to the loading area while helping to minimize wear on the conveyor.
E-stops and pull cords are especially important at feed areas where more inspection is typical and skirtboards present pinch point hazards if not guarded.
Dust management
Dust management is another top priority when handling iron ore and taconite. In addition to being a safety concern, dust can quickly damage equipment if not properly managed.
Iron dust is particularly damaging to bearings, necessitating the use of taconite seals – an extra seal on the bearing which can be filled with grease and purged to prevent contamination of the lubricant and subsequent damage.
The level of dust management often varies throughout different areas of the plant, with some areas experiencing the potential for excessive dust. Feed areas and transfer points can be especially problematic.
To manage dust in these areas, conveyors should be designed with dust pick-off points, as well as skirtboards to contain any potential fugitive dust. An apron seal, which is an additional piece of rubber, can also be incorporated into skirtboards as a sort of double sealing mechanism.
The harmful nature of dust to equipment also means being diligent with preventive maintenance and housekeeping. In addition to keeping dust in the environment at bay, regular oil changes on the reducer are essential to prevent dust from infiltrating and destroying the equipment.
One upgrade on the traditional motor and reducer setup that prevents dust infiltration is the use of a motorized head pulley, in which the motor and reducer are internally contained within the head pulley. It comes at a premium price but can have a quick payoff if it prevents a failure due to poor housekeeping or forgotten oil changes.
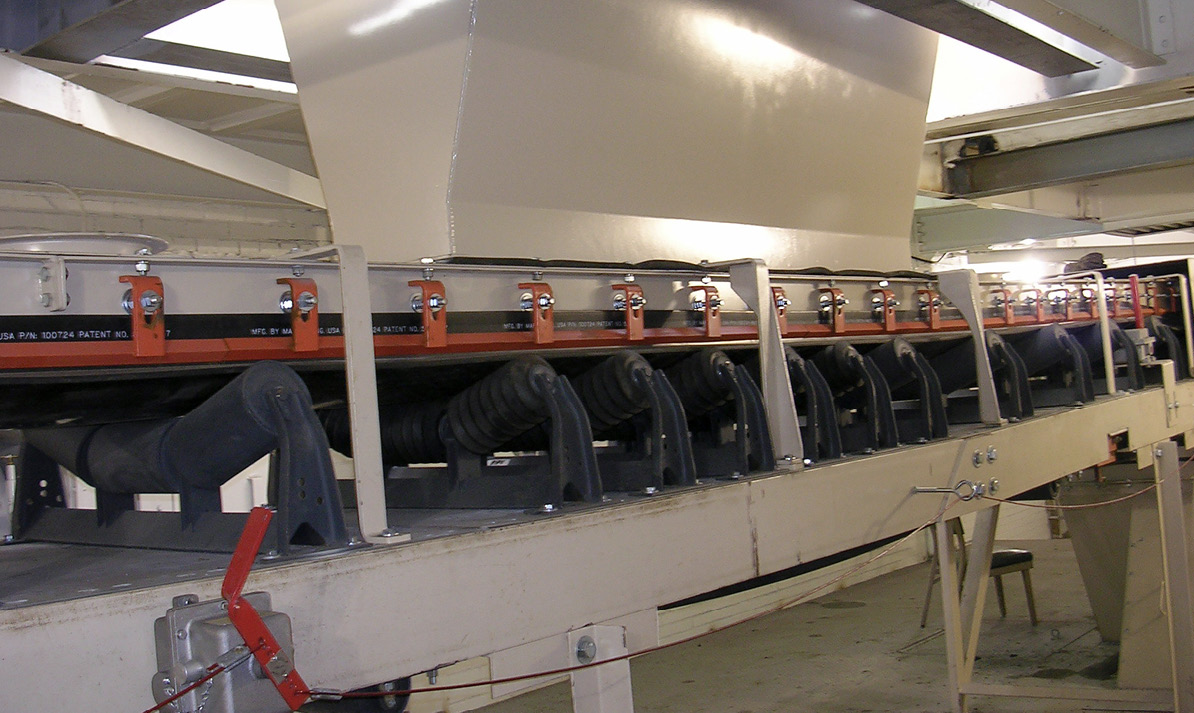
Weather/operating conditions
The frigid winters typical of the Midwest U.S. must also be considered in the design of a conveyor system for the Iron Range.
Conveyors should utilize low-temperature grease in the bearings and employ ductile iron bearings in lieu of cast iron, which can be brittle in extreme cold. Low-temperature-rated instruments, as well as an oil heater in the reducer, are also typically recommended.
Protection from the elements is often necessary for conveyors operating outdoors. Weather covers offer effective protection of the material from wind, rain, and snow. When additional protection is needed for employees walking the conveyor, gallery enclosures can be employed.
Abrasive wear
Abrasive wear is a primary concern in designing reliable equipment for use in the Iron Range, with protection needed at all areas in contact with the material (belts, skirtboards and discharge hoppers). Iron ore and taconite are so abrasive in fact, that standard abrasion-resistance measures are often insufficient.
While AR400 plate (quenched and tempered carbon steel) is suitable for equipment protection in other industries, the iron ore sector requires a bit more muscle. Manganese steel plate is a costly upgrade, but worth its effectiveness in fighting against abrasion.
It is also common to increase material thickness on hoppers and feeders (particularly in the case of the discharge hopper), so that if abrasive wear does occur, there is an extra wear allowance built into the design.
Additional maintenance considerations
The harsh operating conditions associated with iron ore and taconite processing make site maintenance programs especially critical, with small issues having the potential to quickly escalate into major problems.
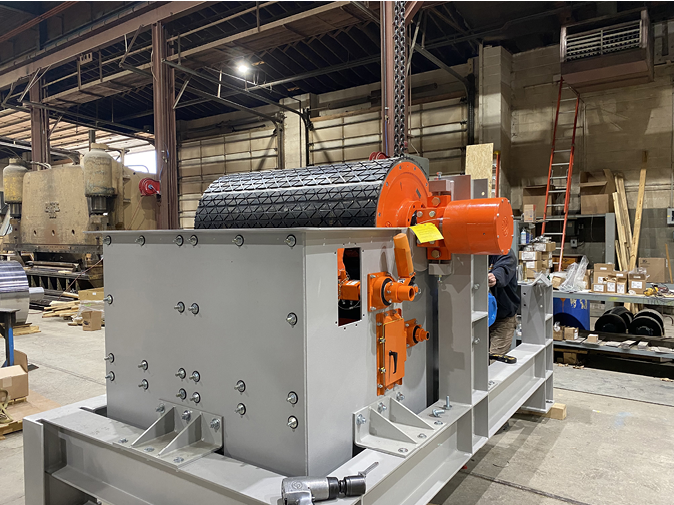
Managing carryback and sticky material
Areas of the plant conveying materials with a higher moisture content can have problems with carryback and material sticking to the belt beyond the discharge point. Carryback can potentially become lodged between the belt and pulley and can also cause buildup on idlers and pulleys, considerable problems when it comes to iron ore.
Return-side belt plows, or v-plows, are helpful in managing material on the underside of the belt. Positioned just prior to the tail pulley on the return/non-carrying side, the plow prevents large particles from wedging between the belt and pulley. Self-cleaning tail pulleys, of which there are various designs, are also helpful in this effort.
When material presents a sticking issue on the carrying side of the belt, primary and secondary cleaners can be incorporated to prevent problems.
Inspections
In addition to diligent housekeeping and oil changes, site personnel should prioritize regular inspections of all equipment and conduct all routine maintenance procedures on a strict schedule based on manufacturer recommendations.
Proper lubrication
All moving components (bearings, pulleys, etc.) should be kept lubricated as well. This will not only prevent friction between components but will also help to negate the abrasive nature of any fugitive material the components may encounter.
Keeping a spare parts inventory
Plant managers and maintenance personnel should also plan to keep an inventory of spare parts. This should include both two-year operational spares (wear items expected to fail eventually) and capital/critical spares (expensive long-life items with long lead times). It may be tempting to not include capital spares in the stock, as these items are not expected to fail, but in the event that they do, having them on hand means the difference between days and weeks of downtime.
Concluding remarks
While the demanding conditions associated with handling iron ore and taconite in the Midwest can be challenging, by keeping considerations such as safety, durable construction, dust management and more in mind and following recommended maintenance procedures, plant managers in the Iron Range can ensure their belt conveyor systems are designed – and maintained – for maximum reliable service life.
Those unsure of where to start, or looking to upgrade their existing equipment, should work with a qualified OEM.
About the author: Dan Baxter works in material handling sales for FEECO International.