North American Mining spoke to two raise borer OEMs and three drilling contractors about the current state and future direction of the raise boring sector.
by Jonathan Rowland
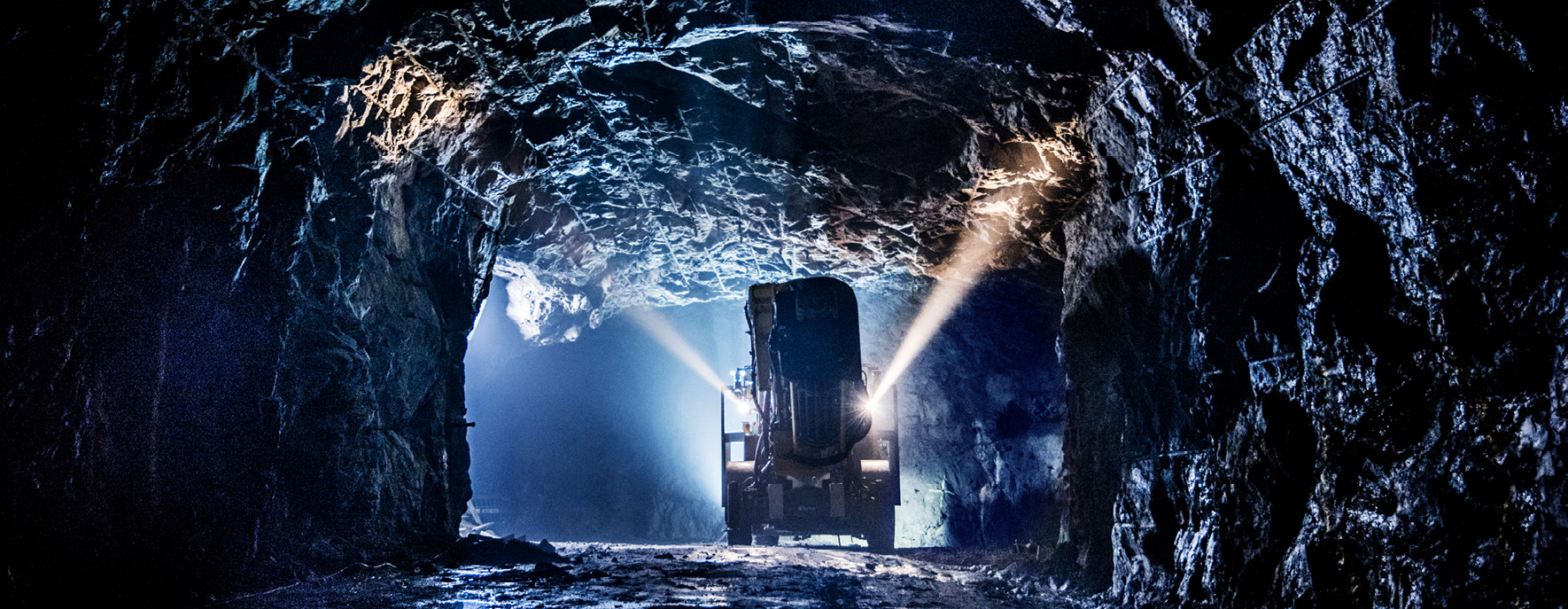
When you think of raise boring in underground mining, you probably think about the construction of ventilation and access shafts. But they are not the only application. With more advanced and increasingly mobile rigs being developed, their potential has grown as mines look to take advantage of the benefits of raise boring above alternative excavation methodologies.
“Compared to drill-and-blast techniques, raise boring brings a number of benefits,” explained Izak Bredenkamp, group business development manager at Master Drilling, a global drilling services provider. “Since it uses no explosives, it is safer and eliminates the risks posed by rock fractures associated with blasting; it also provides stable and accurate circular excavation with zero damage to the sidewalls of the hole. Meanwhile, the operation of modern raise borers delivers cost-effective, quick, efficient, and flexible excavation at various angles and dips, with advanced controls providing the ability to obtain machine data and advance rates.”
As new mines are constructed to meet demand critical metal and minerals, raise boring can also provide flexibility to mine development, particularly when mines require multiple shafts, slopes (declines), and underground development as part of initial construction. “Raise boring offers the opportunity to add a second or third shaft during initial construction of a mine, off the critical path of the schedule, before the completion of a slope of decline,” noted Kyle Wooton, senior VP of operations at Frontier-Kemper Constructors Inc (FKCI), a full turnkey provider for new mine construction. “These shafts are economically advantageous, because the contractor who is set up to handle rock can handle the raise-bored cuttings out of the primary shaft or decline.”
That is not to say that raise boring is without challenges: the same pressures currently impacting the underground mining sector in general – greater depths, complex geologies, productivity, automation and digitalization, safety – are also playing a role in the development of the raise boring sector.
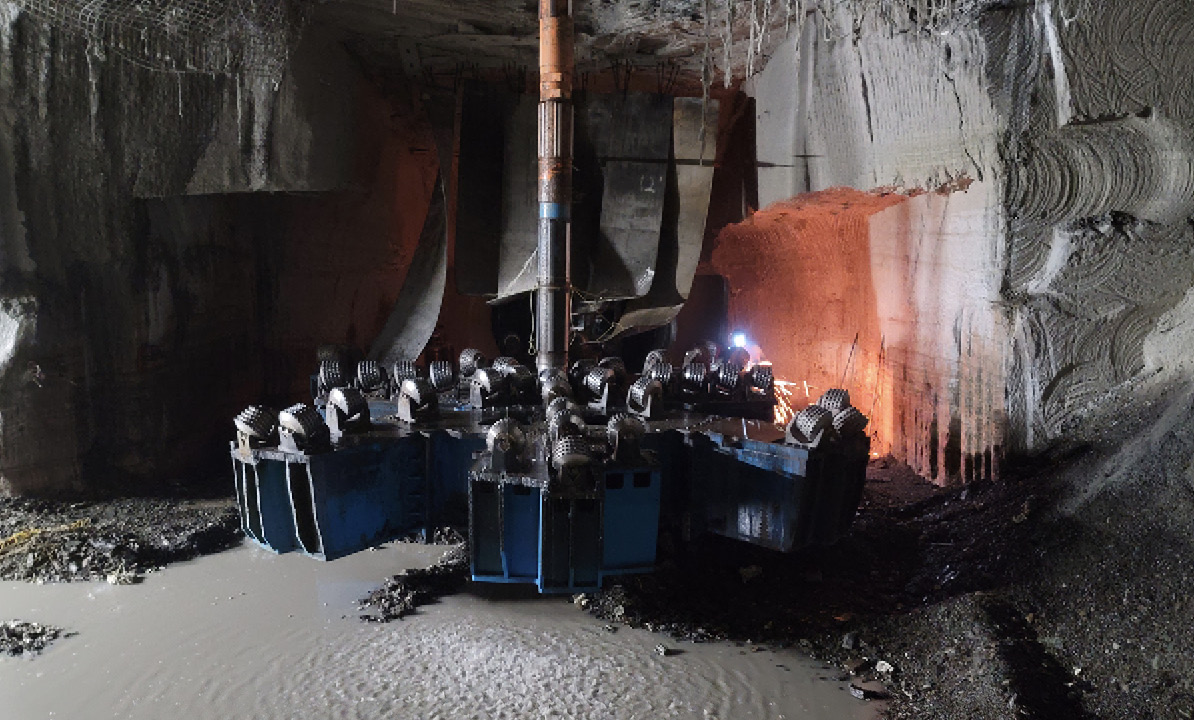
Going deeper underground
“As mines extend deeper underground, there is often an increase in the compressive strength of the rock,” Tijana Turbic, global product manager, raiseboring and Easer, at Epiroc, told North American Mining. “Harder rock is more challenging to drill, crush and process, which requires the development of advanced technologies that are capable of efficiently handling harder rock, while minimizing wear and tear on equipment.”
“There are several challenges posed by deeper progress underground,” agreed Master Drilling’s Bredenkamp. “These are mainly related to rock stresses and the impact on safety, heat and ventilation requirements, as well as productivity and economic impact. Mines want to reach the ore body as quickly and safely as possible. Raise boring operations allow for ventilation to allow these activities to take place; some blind boring and even horizontal boring has been done with raise boring machines to allow for quicker development.”
As shafts get deeper, “it creates the need for a larger machine, exposes the raise borer to unforeseen geological conditions and increased ground water inflows, extends the time between shaft boring and installation of the liner, and exposes the cutters to more cutting time,” added FKCI’s Wooton. From a contractor’s standpoint, this provides an opportunity to consider its equipment fleet and procure newer technologies and safety features. “For example, when we purchased our Herrenknecht RBR 600, we elected to add the robotic arm rod handler, which reduces hazard exposure during rod changes,” noted Wooton.
Mining is “always at the mercy of geotechnical factors,” concluded Glen Fallon, area manager of raise boring at Cementation Canada Inc., a global mine development contractor. “The deeper you go, the tougher and more unpredictable the ground conditions become due to rock pressure, quite aside from specific local geologies. As we go to greater depths, the earth’s dynamic elements become harder to manage overall, making it difficult to complete the job at hand. Transportation costs also escalate: the logistics of rod handling/storage and the amount of muck generated at the lower horizon for a long hole should not be underestimated. We also see trends for larger and longer raises, which in turn drives a need for larger drills and hardware.”
Productivity in raise boring
“Any efforts to reduce the number of trips up and down the shaft to maintain the cutters is going to offer a great advantage to the contractor,” agreed FKCI’s Wooton. The point also picked up by Master Drilling’s Bredenkamp: “Cutters are the most expensive consumable during reaming. The more meters you can get from cutters, the more cost effective this will be. The time spent on cutter changes is also reduced.”
According to Bredenkamp, the basics of cutter selection and operation include:
- Choosing the right cutter for the geology.
- Ensuring a proper cutter dressing.
- Operator competence.
- Correct machine settings.
- Improve tungsten for cutter buttons.
- Improved casing materials.
- Better shaft lubrication.
Beyond cutter design, operating practices also have a significant impact on raise borer productivity. As an example, “lowering reamers for cutter change is the opposite of productive and the highest risk in any raise boring operation,” said Epiroc’s Turbic. “By designing a cutter bearing package that matches the cutting structure performance, you can prevent unwanted interruption to the drilling process.”
There was not universal agreement on the role of cutters on raise boring productivity, however. “When raise boring large ventilation shafts, cutter performance is of course important,” said Jarko Salo of TRB-Raise Borers Oy, whose Rhino line of raise borers are distributed by Sandvik. “Any failures are likely to cause huge delays and other problems with the project. However, when talking about raise boring productivity with smaller diameters, we know from experience with production drilling applications that cutter performance is only really a factor with per unit costs. Other factors – like set-up and demobilization times – are far more important to productivity.”
Picking up this theme, Wooton also noted the importance of mobilizing and demobilizing equipment. “It’s often more important than the boring rates. Contractors are constantly trying to innovate their equipment for fast set-up and tear down to reduce labour and haulage costs, as well as creating opportunities to reach tough project locations.”
Automation, remote control, and safety
Adapting to more challenging mining and raise boring conditions “raises related concerns about worker safety,” began Epiroc’s Turbic. “To address these concerns, innovative solutions are being developed to minimize risks and enhance safety measures.”
One such solution involves the introduction of mobile and automated equipment to support tasks like replacing cutters and reamers in high-risk zones. “In this approach, the focus is on reducing the need for manual labour in hazardous areas,” Turbic continued. “By utilizing mobile and automated equipment, workers can remotely operate machinery and perform tasks without direct physical presence in the risky environment. This minimizes exposure to potential dangers associated with challenging underground conditions.”
This also has as an operation benefit: by reducing reliance on human intervention in high-risk zones, tasks are completed consistently and without compromising safety standards. And when it comes to digitalization, “modern raise borers can be equipped with data analytics and monitoring systems that allow for real-time tracking of equipment performance and environmental conditions,” concluded Turbic. “This proactive approach allows operations to identify potential issues before they escalate, ensuring uninterrupted operation and maximum efficiency.”
However, traditional raise boring remains “grounded in a very human element,” Cementation Canada’s Glen Fallon. “At the same time, we’re committed to achieving zero harm in our operations. We are thus constantly trying to find a balance between employing reliable automation solutions that improve operator safety and project results, while still maintaining the responsiveness that the human factor can provide. The linchpin in a thorough understanding of the expected geology and environmental conditions in advance, combined with real-time perception from the drill rig and measurements as confirmation, with adjustments as necessary.”
Regulations in raise boring
Government safety requirements also play a “pivotal role in shaping the efficiency of raise boring operation,” according to Turbic. Beyond the development of remote-operating technologies, advances in safety regulations have had a number of additional impacts.
Enhanced safety protocols: government safety requirements necessitate rigorous safety protocols in raise boring operations. Latest developments in practice prioritize comprehensive training for personnel, ensuring they are well-versed in safety procedures and equipped with the necessary knowledge and skills to operate safely. This reduces the likelihood of accidents and disruptions, contributing to operational efficiency.
Advanced safety equipment: To meet safety standards, rigs are being equipped with cutting-edge safety features, including enhanced operator interfaces, emergency shutdown systems, and improved monitoring tools. These not only ensure a safer working environment but also minimize downtime due to safety-related incidents.
Environmental compliance: Government regulations often include environmental protection requirements with the latest rigs designed to reduce emissions, noise pollution, and the environmental impact of drilling operations.
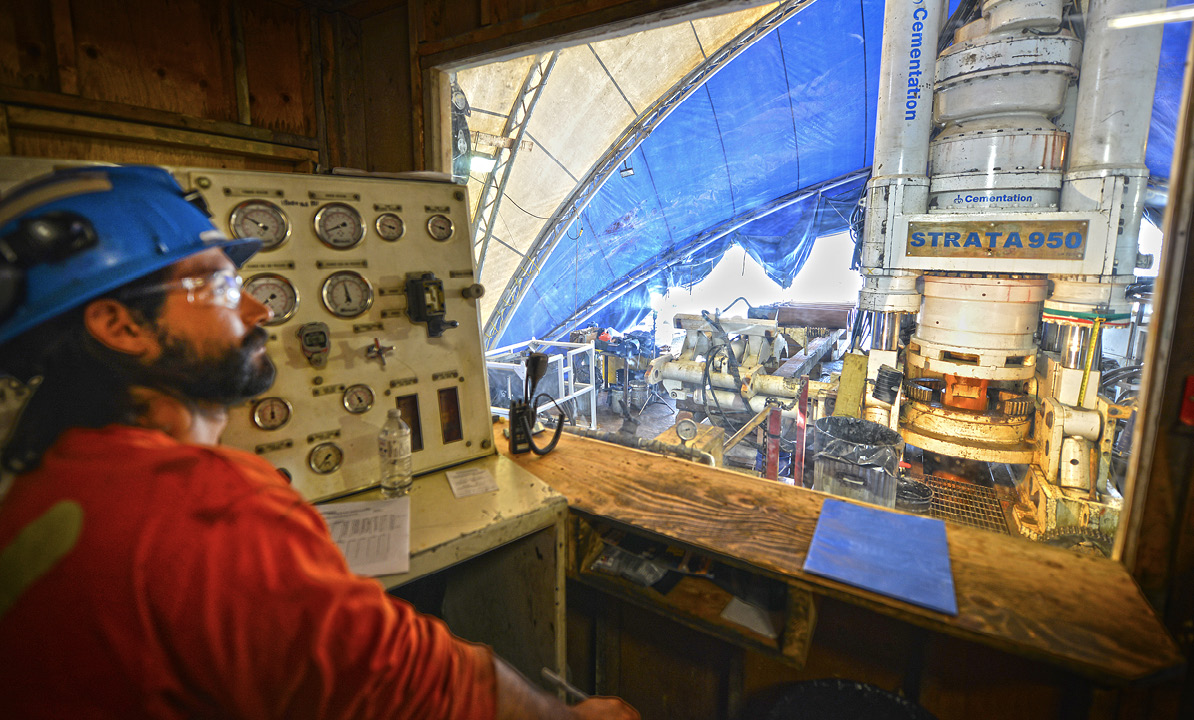
Some technical considerations
“Like anything else we do,” said Patrick Hudd, corporate manager – international & marketing, at Cementation Canada, “we have to evaluate what is the best approach for the project and select the right equipment. Other factors that contribute to efficiency include engineering studies and prefeasibility assessments, data, project design, supply chain logistics, capital sustainability and a mine’s geotechnical presentation. If we are well set up at the outset, we save time and money and add tremendous value.”
For a large diameter upreamed raise bore to be successful, Fallon suggests four questions that must be answered:
- Is there access at the top and bottom of the raise? Upreaming for long large-diameter holes, requires top access for the set-up and bottom access to install the reamer head and muck cuttings.
- Can we handle the muck generated underground? Significant volumes can be generated on large-diameter projects. Mines should not underestimate the mucking requirements – and the potential for delays – this can have. A 5.52 m dia. ream may progress at 0.5m per hour, generating about 12m3 in-situ volume, or 40tph, of spoil. Complicating this, the mine may not want to pay to hoist this waste or there may be restrictions on waste hoisting windows to maximize ore hoisting.
- Is the ground suitable? Do we thoroughly understand the
anticipated ground conditions? This affects sidewall stability and water inflows. Generally, the higher the rock quality designation (RQD), the better the rock will support itself in a vertical hole, meaning fewer reaming stalls and less in-hole hardware fatigue. The same outcome can be
said for lower compressive strengths and low silica contents. - Is the design within current equipment capabilities? The length of raise or sections currently proven is around
1,000m for reamers and in excess of 6 m dia. in hard rock.
Looking ahead
Epiroc is “working on several noteworthy developments that enhance the efficiency and productivity of both our Robbins and Easer rigs,” noted the company’s Tijana Turbic. These advancements provide a glimpse of what to expect in the near future:
- Continuous drilling with automated pipe handling not only minimizes downtime; it also enhances drilling efficiency since operators can focus on other crucial tasks while the rig handles the drilling process. The Epiroc Easer
E10 S is the first of the company’s product line to be equipped with this technology, followed by the Robbins 92 and the rest of the Robbins family. - To ensure continuous drilling for extended periods, Epiroc is developing a pipe rack system for uninterrupted operations. Designed to store and manage drill pipes, it will allow drilling operations to continue seamlessly for at least an entire shift. This innovation optimizes operator time and further increases drilling productivity. It will be rolled out first in the Robbins product line.
- The company’s digital consumables tracking tool enables efficient monitoring and management of drilling consumables, ensuring operators have a clear view of
when replacements are needed. This helps reduce downtime associated with unexpected tool changes and streamlines the maintenance process.
“Our perspective on the future is highly optimistic, driven by several trends and evolving applications,” continued Turbic. “We are witnessing a shift in the role of raise boring, as rigs are being progressively integrated into various applications beyond traditional ventilation, ore passes, and lift shaft. Their remarkable capability to drill high-quality long holes is gaining recognition, not only in production drilling within mining operations, but also in other specialized areas where the quality of holes is of utmost importance.”
“Within this lifetime, we will see many changes in the rase boring sector,” agreed Cementation Canada’s Glen Fallon. “One of the key current trends in underground mining is electrification, which may ultimately result in reduced need for ventilation. However, the picture for the raise boring sector as a whole is positive. We are experiencing requests for larger and longer raises at greater depths than ever. All scenarios also bring with them a need to innovate how we handle materials, including reducing our reliance on mucking and exploring how to create alternatives, such as increased ore passes. Meanwhile, the use of raise-bored shafts for borehole hoisting gives an opportunity for expanding and deepening mines to utilise this more efficient means of transportation, compared to extending ramp haulage.”
“Downreaming is another emerging alternative gaining stream seen in Sweden,” added Johan Sälgfors, CEO of Orefields Raise Boring AB, which has formed the Orefields Cementation Alliance with Cementation Canada Inc. “Here at Orefields, we have developed a method of making new shafts into existing shafts that allows for the distribution of materials or redirection of ventilation where needed.”
“An increasing number of mines are going underground,” concluded Master Drilling’s Izak Bredenkamp. “Demand for raise boring is thus likely to grow. Developments to look for include remote cutter changes; the application of thin sprayed-on liners (TSLs) behind the reamer as we ream; fully-remote operations; blind shaft drilling, equipping as we progress; and horizontal development using raise-borer cutting technology.”
The articulated, highly-mobile Rhino 100 raise borer was developed specifically for slot raising in production drilling. Photo: TRB-Raise Borers Oy.
The next frontier: raise boring for production
“What is exciting in raise boring is the new development in slot raising in production drilling applications,” noted Jarko Salo of TRB-Raise Borers Oy. “Raise boring perfectly meets the need of production drilling. It’s safe, productive, and simple: indeed, it can be completed in a single pass. The consequent reduction in complexity alone provides many benefits to underground operators.”
However, raise borers are still seldom used for production for one simple reason: their lack of mobility. “For typical production, the time and cost of daily raise-borer transport and set-up makes it impossible to justify,” continued Salo. However, slot raising is different.
“Slot raises are relief holes within a stope that provide voids into which blasted rock can expand, thereby improving fragmentation,” explained Salo. “These holes can be produced using a number of methods but were a prime opportunity for a raise boring revolution – as long as an appropriate machine could be developed that allowed rapid machine set-up, dismantling, and relocation.”
The Rhino 100 raise borer was developed specifically for this task: it’s an articulated, highly mobile unit capable of carrying all necessary equipment to drop a standard slot. “Set-up and operation follow much the same principles as any mining jumbo or long-hole rig,” said Salo. “The design also integrates dust suppression and a muck guide to create a dust-free drill site and remove cuttings from the rig. And when combined with tele-remote controls, as is often the case nowadays, the safety of the operator, as well as the efficiency and productivity of the mining operation, is maximized with one simple solution.”
Agnico Eagle Kittilä gold mine in Finland has been a pioneer in the use of raise boring for production drilling. The first Rhino 100 was introduced there in 2014 and since then has proven to be a “much more productive solution” than the long-hole stoping method used there before. “Raise boring allows all work stages to be completed by a single machine and single operator, simplifying the process and speeding-up cycle times. It also allows both the long-hole drills and supporting equipment to be reassigned to other tasks.”
Despite the advantages, raise boring for slot raising is “nowhere near a new mining standard”, admitted Salo. North American mines have also been “slower to follow this trend of ‘easy productivity improvement’ when compared to Europe and Australia.”
However, some are now taking the plunge, including Nevada Gold Mines, Nevada; OceanaGold’s Haile Gold Mine, South Carolina; Agnico Eagle’s Meliadine gold mine, Nunavut Territory; and Fresnillo plc’s Juanicipio silver/gold project, Fresnillo. And Salo is positive: “ever since the introduction of the Rhino 100, there has been huge interest in raise boring as never before. And as we continue to prove at mines around the world, a single raise borer work order can turn a typical mining operation around so that horizontal development becomes the bottleneck.”