Job site mechanization offers cutting-edge industry solutions, and the benefits can add up – quickly.
By Raymond Ippersiel
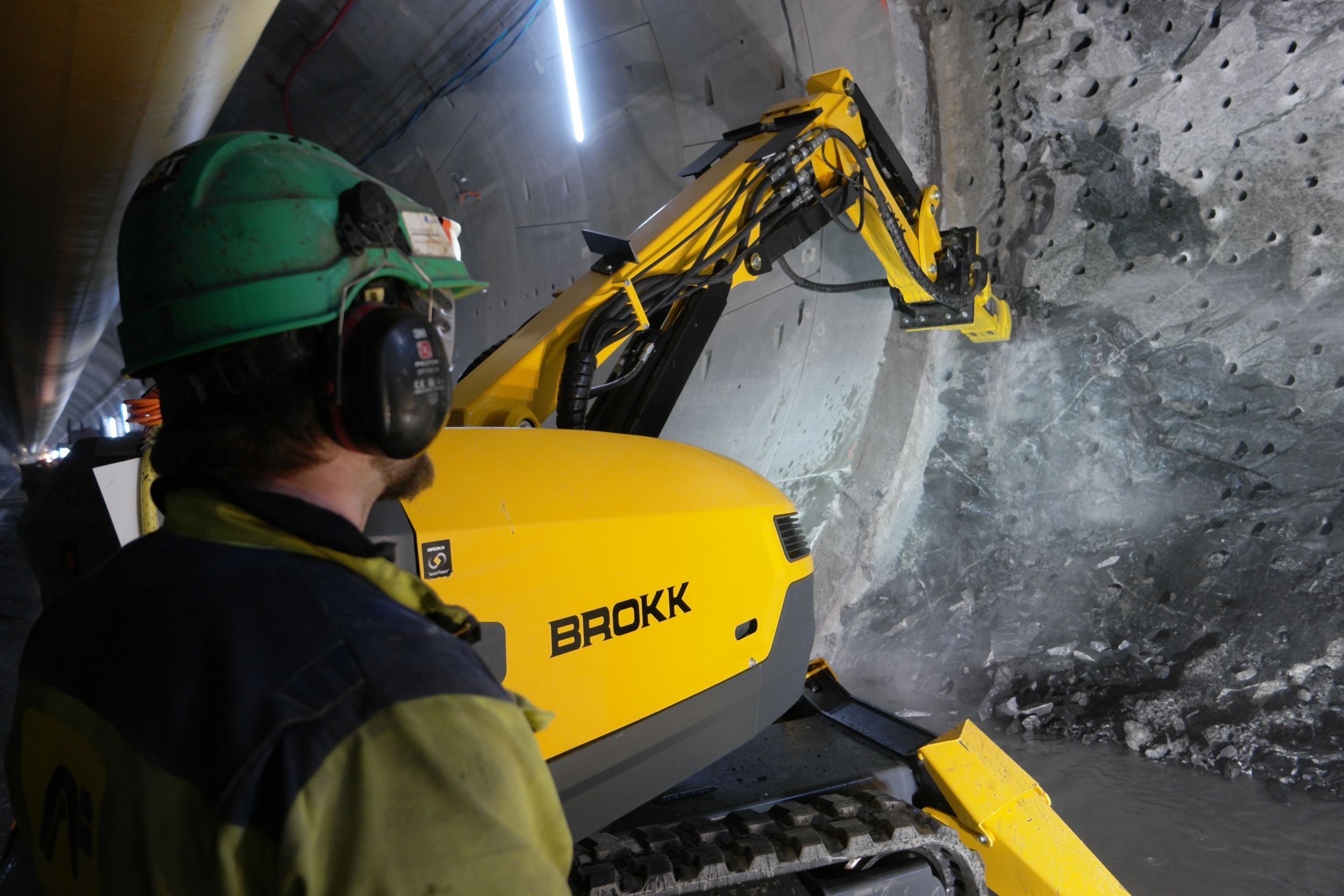
The mining industry continues to see steady change. With precious metals like gold, platinum and chrome being vital components in everyday objects, the demand for these ores continues to grow. Crews are pushing for safer and more productive solutions to transform modern mining operations. At the same time, “The Great Resignation” and Baby Boomer mass retirements contribute to labor shortages across the board.
With all these factors at play, relying on manual labor is simply unsustainable – in terms of worker recruitment and retention, safety, productivity and overall cost-effectiveness. As a result, successful operations work to think outside the box and supplement experienced crew members with technologically advanced equipment like robotic demolition machines to increase efficiency and reduce the physical strain on laborers. Additional mechanization options help operations take advantage of current opportunities while accommodating industry trends.
PRODUCTIVITY BOOST
Handheld pneumatic breakers and other highly physical methods have been commonplace for decades. Traditional mining methods rely on hours of punishing physical labor in extreme conditions using manual tools such as jacklegs, stopers and ad-hoc bar and arms. However, increased job site mechanization has allowed mining operations to revolutionize productivity.
A demolition robot paired with a hydraulic breaker, for example, improves upon previous productivity goals with impressive hitting power, on par with excavators three times their size, and offer industry-leading power-to-weight ratios. These compact machines access some of the most confined and restrictive job sites – including underground mines. At 31 inches (79 centimeters) wide and weighing 1,235 pounds (560 kilograms), the most compact units can fit through small tunnels and are light enough to be lowered down a shaft by crane, making them ideal for close quarters and for mining. Larger models are available with higher power ratios for more challenging applications or larger shafts.
By employing these heavy-hitting machines, mining operations can greatly increase efficiency in applications previously limited to large crews with handheld equipment. One mine employing demolition robots has seen labor costs per linear meter go down by 60% from conventional manual methods.
SAFETY BENEFITS
For many operations, increased safety is one of the biggest benefits of mechanization. Remote-controlled demolition equipment addresses some of the most pressing safety concerns this industry faces.
With an operating distance of up to 984 feet (300 meters), remote-controlled units physically distance employees from falling rock, harmful vibrations, sprained backs, pinched fingers and unsafe noise levels. Long-term use of demolition tools like jacklegs, stopers and ad-hoc bar and arms is linked to a number of chronic injuries, including carpel tunnel syndrome, nerve damage and hand-arm vibration syndrome.
For operations using remote-controlled machines, these safety benefits can quickly add up. In the United States, for example, keeping workers out of the most dangerous areas can result in significant savings on workman’s comp and insurance premiums. Remote operation paired with smaller crew size can significantly lower worker liability costs by limiting personnel in confined spaces or hazardous operations.
RECRUITMENT AND RETENTION
Implementing cutting-edge technology also offers some powerful recruitment and retention tools. When it comes to safety, for example, the workforce is well-aware that quality of life and length of career can be significantly affected by injuries and silica dust exposure.
At this time, the median age of a miner is 42.1 years. Mining operations that invest in mechanization reduce the amount of dangerous and hard manual labor workers must perform, which is a powerful benefit to young and experienced workers alike. A young employee may consequently see mining as a long-term profession, while an experienced worker may see it as more realistic to remain in the industry for the duration of their career.
THE MECHANIZATION ADVANTAGE
It’s both an exciting and challenging time for mines. Opportunities abound, especially those who find creative ways to recruit, retain and best use the skills of their workers. Technological advances, such as robotic demolition, can help change the way mining operations work and make it possible to thrive in today’s environment while preparing for the future.
Mechanization allows operations to quickly adapt to changes in labor, process or regulation, keeping them ahead of the curve – and the competition.
About the author: Raymond Ippersiel is a training and application specialist for Washington-based electric remote-controlled demolition machine and attachments company Brokk, and has worked as a machine operator since 1979.