Hydrogen is one of the buzziest of sustainable buzzwords. Does it deserve the hype?
By Jonathan Rowland
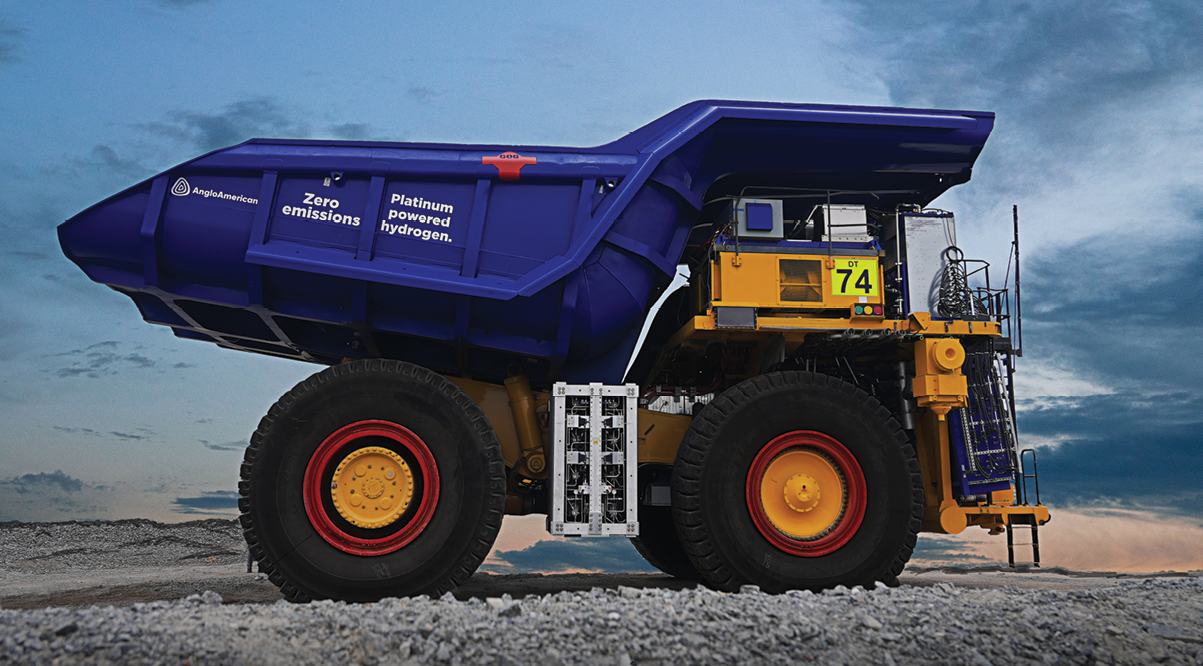
A hydrogen milestone
Much about the mining process is complex – from exploration May 2022 saw the launch of the world’s largest mine haul truck to be powered – at least in part – by hydrogen. Developed by Anglo American, the catchy-named nuGen Zero Emissions Haulage Solution is the latest step in the mining industry’s transition to net-zero emissions; it also adds to the already-considerable and excitable talk around hydrogen as a critical element in the global effort to limit global warming and the efforts. In this article, we consider the potential use of hydrogen within the opencast load and haul environment, before going on to consider whether hydrogen lives up to the hype that surrounds it.
The nuGen truck is the product of a partnership between Anglo American, multinational energy services company; Engie, who produced and supplied the hydrogen for the prototype; and engineering and technology companies First Mode, Ballard and NPROXX. Retrofitted from a traditional diesel-powered ultra-class truck, it is designed to operate in everyday mining conditions at the Mogalakwena platinum group metals (PGM) mine in South Africa.
The onboard 2-megawatt power plant replaces the traditional diesel engine, and was designed in collaboration with First Mode, a Seattle-based creative engineering firm, which has worked on (among others) NASA’s Mars Exploration and Rover programs. The power plant comprises a hydrogen fuel cell and battery pack, each of which provides half of the available power. It’s a combination that helps overcome the challenges that hydrogen fuel cells and batteries pose when used individually.
As First Mode said in a statement marking the launch of the nuGen truck: “Balancing onboard battery storage with fuel cell power generation allows the truck to take advantage of the best of both worlds, with the batteries enabling energy capture from regenerative braking, and the fuel cells enabling rapid refueling with hydrogen.”
Or as Anglo American explained, “by harvesting the regenerative energy created when driving downhill, we reduce our need for external energy. This energy, stored in the battery, together with the hydrogen extends the truck’s range and reduces the out of cycle time for the trucks, since hydrogen refuelling is significantly faster than recharging batteries.”
Hybridization of fuel supply may be the answer to one set of problems, but it posed a whole new range of design challenges. “One of the challenges in developing the power plant was that the building blocks of a zero-emission truck are fundamentally larger than the building blocks of a diesel truck,” explained First Mode. “Power generation, batteries, hydrogen storage, and the power electronics that connect [the] power plant to the nuGen truck’s drivetrain all take up significant space, far more than the diesel systems that were removed to accommodate them.”
Generating and utilizing 2 MW of electrical energy on a moving vehicle also presents significant practical challenges.
“With the truck expecting a diesel engine and alternator to be present, methods had to be developed to ensure safe operation of the truck, while presenting it with an entirely different electrical energy source,” the company continued. This included a software solution to safely manage power and energy between the fuel cells, batteries and vehicle drivetrain.
Meanwhile, “the challenging vibration and shock environment presented by repeated loading with hundreds of tons of ore required extensive design work for even the simplest components, such as electrical junction boxes, and many pre-existing truck systems had to be repaired after removing the original diesel engine.”
To safely store the hydrogen onboard the truck required the development of a new pressurized tank system by the hydrogen fuel tank system specialists at NPROXX. The Dutch company also designed and delivered the pipework and truck refueling system, as well as two larger tanks for storing hydrogen onsite to guarantee a ready supply of the gas for fueling.
How then does the hydrogen fuel cell work? Anglo American explained as follows: hydrogen flows from the onboard tank into the fuel cell, where it mixes with oxygen and a platinum catalyst. The resulting chemical reaction generates electricity, which is used to power the motors that drive the wheels, as well as supporting auxiliary systems, such as hydraulics and steering. The only emission is water vapor.
Hydrogen beyond haulage: hydrogen-powered loading?
Much of the hype around hydrogen centers on its potential to act as an energy storage medium to support renewable energy generation. In this scenario, renewable energy is used to produce clean hydrogen via electrolysis, which can be stored (or piped to areas of higher energy demand), and then used to generate electricity when it is needed.
The advantages for mine sites of such a hydrogen-based energy ecosystem are clear – especially those sites that operate off-grid and currently generate electricity using diesel generator sets. Mines also often have significant areas of available land that allow for the installation of solar arrays or wind farms. Hydrogen therefore offers the potential to develop a decarbonized mine site. Caterpillar, for example, already offers gensets that are capable of running on 100% hydrogen.
Rolls-Royce is also on the hydrogen train via its mtu brand of power solutions. The company announced that, from 2023, it would market new gensets powered by its Series 500 and Series 4000 mtu gas engines for use with up to 100% hydrogen. It will also offer design-to-order conversion kits to allows the retrofit of existing engines to hydrogen.
“The decarbonization of power generation requires reliable, flexible, but also climate-neutral, power plants to supplement the fluctuating generation from wind and sun. We assume that natural gas will initially be the primary fuel in the development of the hydrogen ecosystem, but we see hydrogen as technically and economically possible. That is why we continue to develop our gas engines for use with green hydrogen – whether as a 10% or 25% admixture or for 100%,” explained Andreas Görtz, vice president of Power Generation at Rolls-Royce Power Systems, in a September 2021 press release.
Combine such hydrogen-based ecosystems with the trend toward electrification of shovels, and hydrogen becomes one potential pathway to the decarbonization of loading operations, without the need to retrofit existing electric shovel fleets with hydrogen fuel cells.
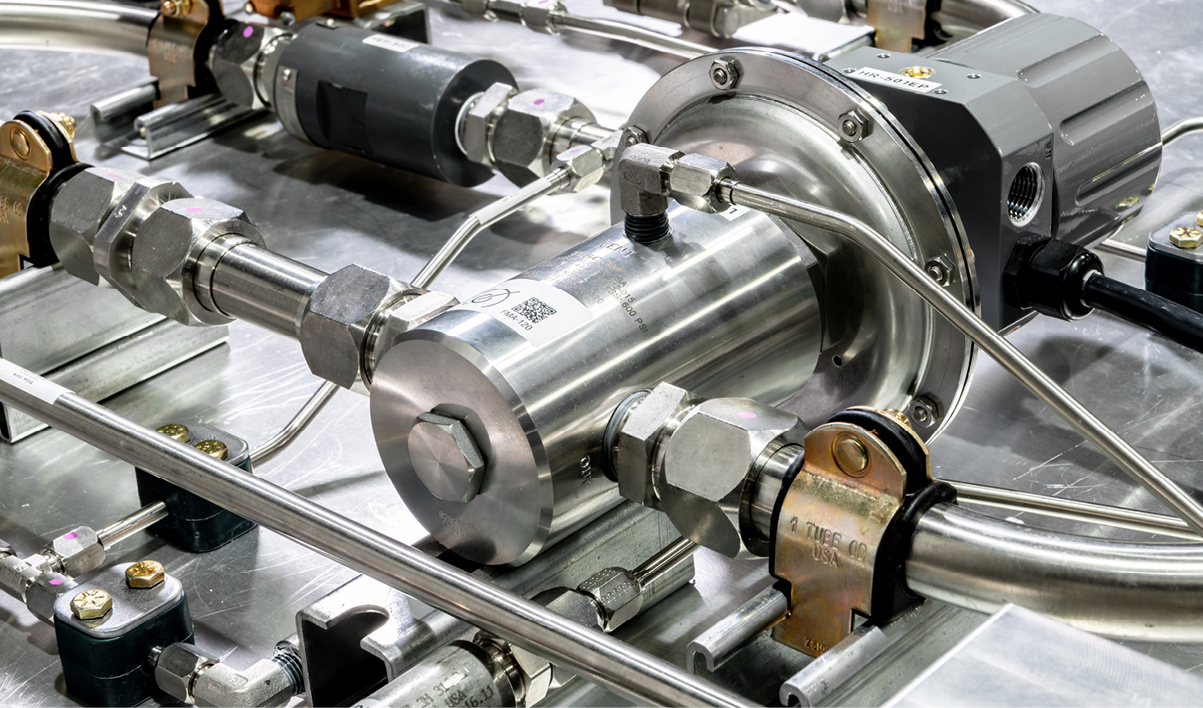
The hydrogen rainbow
The nuGen vision is an example of such an integrated hydrogen ecosystem. In addition to the development of the nuGen truck, the project is linked to the construction of a green hydrogen production complex at the Mogalakwena PGM mine in South Africa, which is one of three sites identified as green hydrogen hubs by the South African Hydrogen Valley Initiative.
Green hydrogen is the “holy grail” of the hydrogen world, according to Bridget van Dorsten, a research analyst at Wood Mackenzie. It describes the process of producing hydrogen via electrolysis powered by renewable energy. A variation is pink (also called purple or red) hydrogen, which uses nuclear energy to power the electrolysis process.
Green hydrogen is emissions free; however, it is expensive, although prices are expected to fall. In the feasibility study of the Hydrogen Valley Initiative by the South African Department of Science and Innovation (DSI), the cost of producing green hydrogen is forecast to be in the range of $4.10 and $4.30 per kilogram by 2030, depending on the location, about 25% lower than the anticipated cost in 2025.
Despite this, the DSI still forecasts a green hydrogen premium over so-called grey hydrogen of between $1.70 and $2.00 per kilogram, although it does admit that it takes a “conservative approach in […] cost evaluation” and that “further reductions are possible depending on policy and technology evolution to 2030.” And Wood Mackenzie is bullish on green hydrogen, expecting it to account for more than 80% of the total hydrogen market by 2050.
This also introduces what has been termed the “hydrogen rainbow.” If green hydrogen is at one end of this color spectrum, at the other are grey, black and brown hydrogen. Grey hydrogen is produced as a by-product of the ammonia, refining and methanol sectors in a process called steam reforming. A variant on this is blue hydrogen, which is also produced via steam reforming of natural gas, but incorporates carbon capture, utilization and storage (CCUS).
Black and brown hydrogen are both produced via the gasification of coal (bituminous and lignite, respectively, although the terms are sometimes used interchangeably to describe any coal-based hydrogen production). Not unsurprisingly, coal-based hydrogen production is the “polar opposite of green hydrogen in terms of carbon emissions,” said van Dorsten. Coal gasification can also be combined with CCUS; however, according to the International Centre for Sustainable Carbon (ICSC), this could be a more cost-effective route to clean hydrogen than the electrolysis-plus-renewable-energy pathway.
“Coal gasification with CCUS costs typically $1.6–$2.4 per kilogram with the lowest cost being that in China,” said ICSC report author Greg Kelsall. “Learning by doing, through large-scale commercial roll-out, together with cost reduction through technology innovations, could reduce the cost by perhaps 10%–15% by 2050.”
Kelsall continued: “In terms of emissions, the addition of CCUS at an assumed, conservative 90% capture rate can reduce the carbon intensity of this process to below 3 kg of CO2 per kilogram of hydrogen. Whilst this is good, it is not consistent with net-zero emissions, so capture technology with increased capture rates approaching 100%, or technologies such as the Allam Cycle based on supercritical CO2 working fluid, should be explored in the medium-long term in the transition to 2050. Cofiring a portion of biomass or waste with the coal feedstock, coupled with CCUS, could lead to net zero or even negative CO2 per kilogram of hydrogen, which would help to ‘future proof’ the gasification plant.”
There are currently three commercial facilities producing hydrogen from coal, coke and petroleum coke: Great Plains and Coffeyville in the U.S., and Sinopec Qila in China. Additionally, the Hydrogen Energy Supply Chain (HESC) pilot project in the Australian state of Victoria, with backing from the Japanese government and industry, successfully produced and liquified hydrogen from Latrobe Valley coal, proving in concept the idea that coal-based hydrogen could be exported in the manner of liquified national gas.
Commercial-scale development – which will include capturing and storing CO2 via Australia’s CarbonNet Project – remains the HESC vision, although the end-of-project report admitted that “much more work is needed to take HESC from a pilot project to a commercial reality.”
Turquoise hydrogen completes the rainbow, and describes the production of hydrogen via methane pyrolysis. Carbon is generated as solid by-product, eliminating the need for CCUS. However, turquoise hydrogen is the “new kid on the block,” said Wood Mackenzie’s van Dorsten. “The process is still in the experimental stage and has yet to be proven at scale.”
Although originally designed to simplify the delineation between climate-friendly hydrogen production and carbon-intensive alternatives, the hydrogen rainbow has become increasingly complex. Other schemes are now coming into place that certify hydrogen according to the carbon intensity. The Green Hydrogen Standard, for example, requires projects to operate at 1 kg of CO2 per kilogram of hydrogen or less in order to be certified. The rainbow remains helpful in highlighting the complexity of the hydrogen issue. Powering mines with hydrogen is all well and good, but is only sustainable if that hydrogen is itself produced in a sustainable manner – which most is not at the moment.
Hydrogen and mining: symbiosis?
As the above discussion of coal-based hydrogen production above highlights, in addition to being a consumer of hydrogen, the mining industry might yet play an important role in providing a feedstock for its production. It is ironic to consider that an industry so linked to the net-zero transition could yet provide a lifeline to the industry most demonized by the environmental movement.
Less controversially, the growth of the hydrogen fuel cell vehicle (FCV) fleet is likely to support rising demand for platinum (just as growing demand of batteries in electric vehicles is driving lithium demand). As Fitch noted in a March 2010 research note, FCVs “use platinum alloy catalysts, and are estimated to use nearly 10 times as much platinum than platinum catalysts for diesel engines.”
In addition, one of the leading electrolysis technologies – proton exchange membrane (PEM) – also uses PGMs on a significant scale. According to SFA (Oxford), a consultancy specializing in the PGM value chain, “PEM electrolysers currently represent around 70% of new projects, and over the long term provide an opportunity for significant new platinum and iridium demand.” It’s yet another reminder of the centrality of mining to the wider global shift to net zero.
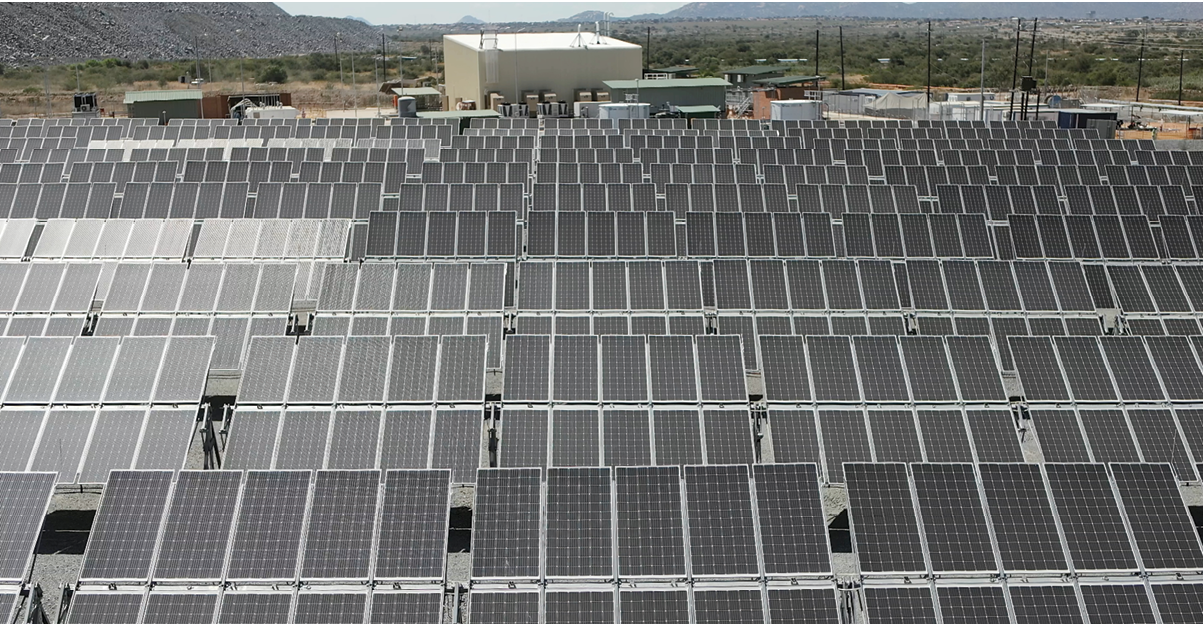
Conclusion
According to Accenture, “the way in which mines are operated makes the mining industry the first logical mover in the hydrogen economy.” The consultancy points to the following:
- Mine haulage fleets “return to base” to refuel at the same site at the end of every shift. They would thus benefit from a centralized refueling infrastructure and suitable economy of scale.
- Diesel fuel and electricity costs are often higher at mine sites given their relative isolation. This provides a strong incentive to switch to renewable energy, which could then be utilized to produce green hydrogen.
- With mileage and bulk less of a concern for heavy vehicles, mine vehicles are expected to utilize hydrogen storage tanks pressurized to a more conventional 350 bar (this is true of the nuGen truck). This implies lower compression costs and storage systems than lighter vehicles, which need more compact and complex tanks with higher pressures.
- Mines are already familiar with issues around the safe
storage and management of chemicals, reagents and
compressed gases. In addition, mines will usually have sufficient land to safely store compressed gasses away from workers, infrastructure and local communities.“While there are still enormous hurdles to overcome before the broader hydrogen economy takes hold, these hurdles are
lower for mining than for most other industries,” Accenture concluded.
In addition, “mining companies have an opportunity to change public perception about their commitment to environmental stewardship and emerge as a spark that ignites the global hydrogen economy.”
With its nuGen truck now rolling, we’ll give the last word to Anglo American CEO Duncan Wanblad: “We believe that the emerging hydrogen sector has the potential to dramatically improve the growth and development of many economies by creating new industrial value chains and economic generation opportunities. Growing the hydrogen economy will revolutionize not just Anglo American’s operations, but all mining and many other industries – and ultimately shape a better, cleaner world.”
AngloAmerican www.angloamerican.com
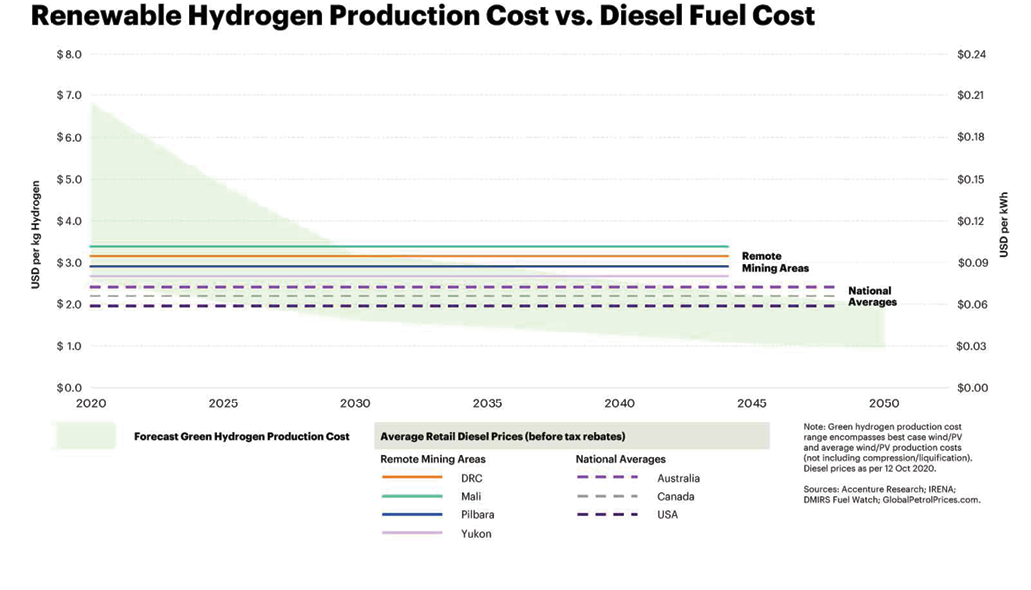