Over 100 Years Ago, No One Thought Rio Tinto Kennecott’s Bingham Canyon Mine In Utah Would Be Profitable. Today, It Is Not Only An Economic Stalwart, But Also A Major Charge In Driving The Future Of Responsible Mining.
By Donna Schmidt
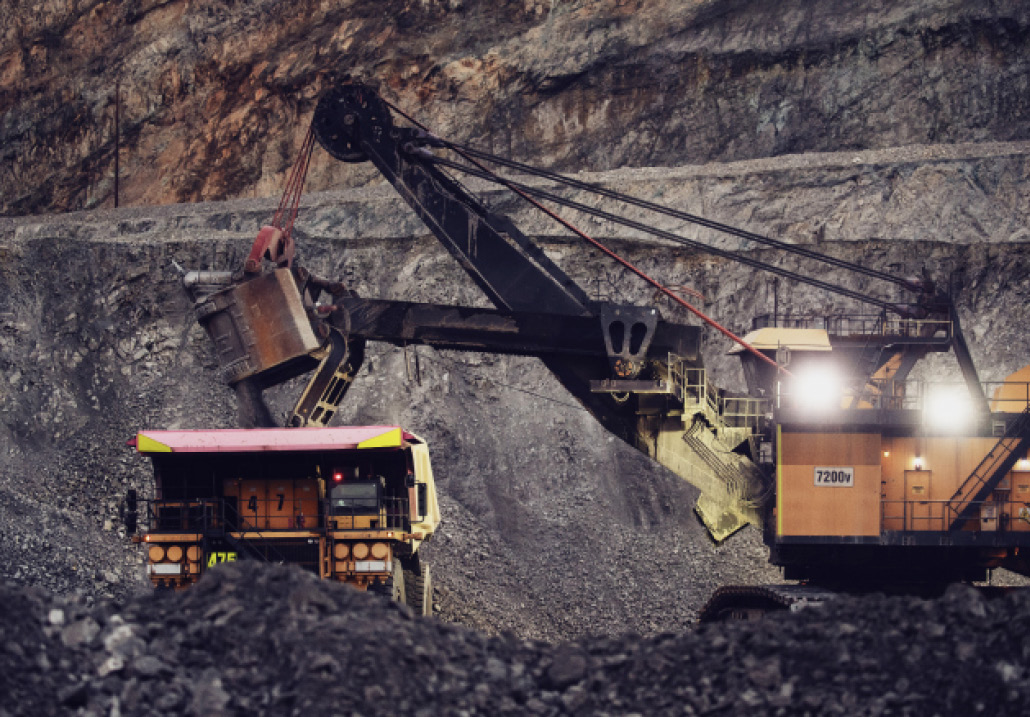
The Bingham Canyon mine in Salt Lake County did not begin its life at the point it is today – that is, with the distinction as the largest open-pit copper mine in the world. When operations there first began in 1906 under the ownership of Utah Copper Company, the surface mine at Bingham Canyon had a low ore grade, just 39 pounds of copper per ton of ore.
As the mine’s management points out now, it’s just that Kennecott still had not taught the world how to surface mine. In the many years since, its 26 miles of operations and more than 2,000 employees have come to serve as safe, productive and efficient, with Bingham Canyon mine production of 159,400 tons of copper in 2021 along with 139,500 ounces of gold and 2,228,000 ounces of silver.
And best of all, owner Rio Tinto stresses, it’s being done in a way that is respectful to the environment – something that those even at the mine’s start in 1906 couldn’t ever have imagined.
From the Ground Up
To understand this indisputably enormous operation is to understand what lies beneath the surface, and a crucial term to use here is “complex” – describing both the geology of the site and its surrounding environment.
“According to the Utah Geological Survey, the geology of the Bingham mine orebody is complex. In simplified terms, about 30 to 40 million years ago, magma was injected into a sequence of predominantly quartzite and limestone beds that are part of the roughly 300- to 350-million-year-old Oquirrh Group. The magma cooled to form a body of igneous rock (monzonite porphyry) known as the Bingham stock.
“Hot fluids generated from this magma deposited various copper-sulfide (mainly chalcopyrite) and other metallic minerals, forming a large low-grade orebody,” said Utah Geological Society.
Put more formally, the Bingham Canyon deposit is a classic porphyry copper deposit with economic values of copper, molybdenum, gold, silver and historic lead and zinc production. Peripheral copper-gold skarns, lead-zinc fissures, and disseminated gold deposits are also associated with this copper porphyry system, according to Rio Tinto data.
According to Rio Tinto’s 2020 Annual Report, at the end of 2020, the mine’s Proved Ore Reserves were 365 million tonnes at 0.47% copper and Probable Ore Reserves were 187 million tonnes at 0.39% Cu for total Ore Reserves of 552 million tonnes at 0.44% Cu. The site’s recoverable copper metal as of the same date: 2.126 million tonnes.
Portrait of Infrastructure
Located in the Oquirrh Mountains, the mine is wholly owned by Kennecott Utah Copper, a subsidiary of Rio Tinto. The operation includes a concentrator, smelter, refinery and tailings impoundment in addition to the mining operation itself that measures over two miles across at its rim.
Crews, working on 12-hour shifts, perform the work using rotary drilling and blast, shovel/truck, and in-pit crushing system circuit, with two to four blasts each day.
A running theme for this mine is investments for improvements, and one of the first in a series of significant ones has been an ex-pit, semi-mobile gyratory crushing unit that links it to the Copperton Concentrator via an 8-kilometer conveyor system, which has helped reduce haulage distances from the working faces substantially. Even with that addition, the mine still has a large fleet of Caterpillar mechanical drive and Komatsu electric-drive trucks, most of which are 362-ton capacity, to service 10 P&H electric rope and hydraulic shovels.
Looking solely at its mobile fleet, Rio Tinto Kennecott notes that it does maintain a replacement strategy that looks at several variables on a consistent basis, including efficacy, availability, the ratio of production versus production capability and TOTEX, or total costs needed to maintain a given asset.
A fleet is made greater with an efficient dispatch system; at Bingham Canyon it is managed by Modular Mining (which will eventually transition to Caterpillar MineStar). It also uses Thunderbird Pacific’s drill monitoring and logging systems. Both GPS and Glonass are used for drill positioning, terrain monitoring and mapping.
Rio Tinto selected Kennecott’s Copperton Concentrator as one of the first sites to introduce and implement the business’ new operating system, called the Rio Tinto Safe Production System. Significant improvements have been seen at the concentrator since its deployment last July versus the previous 12 months of performance.
The Copperton Concentrator, which was last expanded in 1992, added some of the largest SAG and ball mills and flotation cells in the world to date. There are four grinding and flotation lines to produce copper and molybdenum concentrate, the former of which is then piped to its smelter located about 15 miles away.
Its smelting facilities include a newer primary flash smelter and flash converter system and a slag treatment plant, part of a large investment project and designed by Outokumpu. The converter treats matte that has been granulated and powdered, and the 98.6% copper from the new converter is refined to 99.5% copper at two anode furnaces and then railed to the refinery’s electrolytic tank house.
Rio Tinto Kennecott confirmed its 99.9% pure copper cathode is sold to various customers based on mine output and customer needs, which include chemical and physical specifications. Most is transported via rail to customers, though the operator does have some customers with no unloading facility – so it meets their needs via truck transport.
Sulfuric acid, a byproduct of its copper smelter, is also captured and loaded into tank cars and shipped to customers.
With Rio Tinto Kennecott producing both gold and silver, in 2020 it was awarded the Responsible Gold Certificate and Responsible Silver Certificate from the London Bullion Market Association, a credible trading platform known globally for its standards to produce gold and silver bars.
“Kennecott provides a heavy-plate electro refined copper cathode that is particularly in demand with up-cast and cast and roll technology,” Rio Tinto Kennecott said, noting that while the product is sold across the USMCA market, the U.S. is its most significant market.
End-use markets for the material are heavily geared toward construction for cable manufacturing, and automotive, with other applications in industrial, coinage, munitions and plating materials.
Rio Tinto Kennecott’s sulfuric acid customers are mainly U.S. based but operate in a variety of sectors including fertiliser and food production, mining, power generation, water purification and other chemical industries. Its molybdenum customer base is worldwide, primarily stainless steel mills.
Nine Levels of Monitoring
With a nine-layer suite of monitoring protection, the mine defines proactivity. That system, it stresses, begins with people – specifically, more than 800 sets of trained eyes keeping track of every square foot of the mine.
“All mine personnel [are] trained in identifying geotechnical hazards during [an] annual MSHA refresher,” Rio Tinto Kennecott noted. “Hazards are reported to supervisors or production control, [then] information is passed to the geotechnical team for investigation,” it added, noting that rock fall spotters are also used during active failures.
The second level keeps those same workers in full focus with regular documented inspections of all areas of mining activity. There are shift supervisor inspections at the beginning of every shift, and periodic inspections by geotechnical engineers that seek out potential hazards such as loose pit wall rock, tension cracks, rolling rock and dust clouds and rock falls on the catch bench. In short, if something is seen, it is addressed.
Layer three brings in technology, in this case more than 220 units of the Prism network and four skyboxes. It utilizes both simple measurement devices as well as sophisticated instrumentation including electronic extensometers robotic theodolites that provide regular updating of slope movement information collected from hundreds of monitoring points.
“Prisms are scanned every hour, and extensometers readings are taken every 10 minutes,” mine management explained. “Movement is captured 24/7, giving geotechnical engineers valuable insight into areas of instability.”
Additionally, six extensometers, the company’s fourth layer of predictive protection, measure tension crack displacements at the open pit’s slopes with tensioned wire line.
TDR, or time domain reflectometry, is considered layer five in the suite. The cable system, which detects and monitors movement of known and potential landslides, is considered a subsurface monitoring device and was designed to detect discontinuities or damage in electric cables. Those changes can aid in determining movement depth, progression and magnitude overall.
Layer number six of nine is the mine’s microseismic array, which work using geophone arrays installed in drilled boreholes. Each detects noises, which are made with every break of an intact rock, which are recorded with their arrival times, then sent to a central officer computer where a software determines the location and provides a pre-computer 3D seismic wave velocity model of the pit.
GroundProbe’s-slope stability radars are layer seven, and the network of three slope stability radars continually survey and detect movements by comparing successive slope scans. Scan time depends on the size of the area, but typically ranges between four and 10 minutes and permits detection of both short- and long-term slope movement.
“The radars are programmed with specific, adjustable alarm settings; if the alarm is triggered, then mine personnel are notified of the movement, allowing rapid evaluation of the surface deformation,” Rio Tinto Kennecott mine management said. “GroundProbe radar’s accuracy level is up to 1/10th of an inch and has a range of 10,000 feet.”
The radars, which saw an uptick in popularity in the industry for its work predicting ground falls including the one Rio Tinto Kennecott suffered in 2013, can give mines data resolution and quality that improves at closer ranges, especially when operated within a few thousand feet of the moving area.
In the layer list, the IBIS Radar System is number nine. The three at the mine use advanced survey technology to monitor slope movement for open-pit mines by scanning a portion of an open-pit in six to eight minutes. At the mine, the effective accuracy level of the IBIS radars are at least 1/10th inch with a range of up to 10,000 feet.
“IBIS radars are also equipped with alarming capabilities, notifying the mine personnel of detected movement in open pit slopes. IBIS radars are capable of monitoring mine pit slopes in adverse weather conditions and during low visibility. The mine is purchasing a fourth IBIS radar,” Rio Tinto Kennecott said.
Finally, the mine has a geographic Information System (GIS) data display that has been customized by Rio Tinto Kennecott staff. It is capable of capturing multiple data sources and is accessible by wireless technology.
While there have been ground falls at the Rio Tinto Kennecott mine over the years, these proactive technologies have been significantly beneficial. Given the mine’s size and dimension, Rio Tinto Kennecott has put predictive technology into optimum use.
Automation, Advanced Fleet Opportunities
It is perhaps most obvious how far Rio Tinto Kennecott has come over the decades since its 1903 founding and 1906 start than in its use of alternative power and automation.
Some 110 years ago, Bingham Canyon mine and nearby smelter were already considered the world’s largest industrial mining complex in the world. The man who proposed the mine, Daniel Cowan Jacklin, is known today as “the Henry Ford of mining” for pioneering processes and equipment that became almost universal. It’s safe to say he would remain proud of that progress.
Rio Tinto Kennecott management is strong in its conviction to constantly look for ways to integrate new technologies to make its operations safer, more efficient and more sustainable. One example of that has been Mark, the company’s “superhero robot,” which it uses to map underground tunnels, test oxygen levels and collect soil and water samples.
He is the company’s newest member of the remote operated vehicle (ROV) team, designed specifically for the mine’s needs – and created using just an over-the-counter rock crawler all-terrain vehicle, formidable engineering skills and a 3D printer.
Rio Tinto Kennecott uses UAVs as well for its preventive maintenance, especially to identify safety risks and map out-of-reach areas. One, known as Wilson, helps crews check machinery quickly, saving time and money.
In general, drones have given the mine a number of advantages highlighting safety above all else. Drones are often used to identify safety risks, such as cracks and signs of rock movement, as well as perform certain jobs that could put staff in harm’s way, for instance, highway mapping or rock fall analysis.
Rio Tinto Kennecott is quickly becoming a leader in the advancement of next-generation fleet options as well.
As part of a $108 million investment earmark announced in 2021, the operator is set to trial underground battery electric vehicles to reduce carbon emissions – at Kennecott and across all of Rio Tinto’s global operations.
In fact, Sandvik Mining and Rock Solutions will be suppling a battery electric haul truck and loader to evaluate performance and suitability for future underground mining fleets.
Sustainability
Sustainability is a crucial mission for the mine and has been for decades. One of its highlighted projects from the mid-1990s, for example, was its transformation of acreage once dominated by overgrazed lands, salt evaporation ponds and illegal dumps to a 3,670-acre shorebird and waterfowl reserve along the south shore of the nearby Great Salt Lake.
“Rio Tinto created the Kennecott Inland Sea Shorebird Reserve (ISSR) under a mitigation plan developed in partnership with the U.S. Army Corps of Engineers to offset the loss of 1,000 acres impacted when the company expanded its tailings impoundment in 1996,” the company said.
“Only two years after opening, the Association of Engineering Geologists designated the ISSR as the Outstanding Environmental and Engineering Geologic Project. The number of bird species using the reserve area has increased from 50 in 1995 to 200 today, with 150,000 birds using the reserve annually, an increase of over 1,000 percent. Because of this incredible success, the reserve has now expanded to over 3,600 acres.”
That area became an Important Bird Area (IBA) in 2004. Today, it is part of BirdLife International’s IBA Program that identifies, monitors and protects a global network of IBAs to conserve birds and other biodiversity.
In 2019, Rio Tinto Kennecott permanently idled its coal power plant. At the same time, it announced the purchase of 1.5 million megawatt hours of renewable energy certificates from Rocky Mountain Power that, combined, have reduced its annual carbon footprint associated with the operation by over one million tonnes of CO2, a 65% reduction.
The coal power station operated for 75 years and idled in 2017 as part of an initiative to manage seasonal air quality and maintenance requirements.
In October 2021, Rio Tinto Kennecott announced it would donate up to 18,387 acre-feet of water annually over the next 10 years to help address dropping water levels at the Great Salt Lake. A donation made in collaboration with the Utah Division of Wildlife Resources, Central Utah Water Conservancy District, National Audubon Society, The Nature Conservancy and Utah Reclamation Mitigation and Conservation Commission, the water will benefit the ecosystems of the Salt Lake Valley rather than be diverted from the lake for other uses.
Rio Tinto Kennecott Managing Director Gaby Poirier said the company takes much pride in those sustainability missions which help the drive to net zero.
“Kennecott has been independently assessed as meeting the highest environmental, social and governance standards in the industry, allowing us to respond to the growing expectations of consumers around the world for sustainable supply chains,” Poirier said.
“We strive to be a leader by demonstrating good management of natural resources, responsibly reducing our environmental footprint and exceeding community expectations.”
In 2020, Rio Tinto Kennecott was the first producer to be awarded the Copper Mark, a new and independently assessed copper industry responsible production program. To earn the distinction, the mine had to demonstrate compliance with more than 30 criteria for responsible environmental, social and governance practices. Its Copper Mark was bestowed that August, just five months after the formation and launch of the initiative by the International Copper Association.
Investing and the Future
Poirier pointed out that Rio Tinto Kennecott will continue to maintain its momentum to drive the future of supplying vital materials for a greener future.
To do that, of course, takes money, which is why the company has backed up its ongoing dedication with sizeable investments into the future of the mine, which is today in its prime.
“Rio Tinto Kennecott is helping to drive economic strength by supplying the critical materials needed for decarbonization in the United States. We operate the largest smelter in the U.S., one of only two operating in the country, enabling us to supply 15% of domestic copper production, and the copper we produce has the lowest carbon footprint in America,” Poirier said.
Since 2019, the miner has made two major project announcements for Rio Tinto Kennecott that each have come with matching major price tags. The first was $1.5 billion for extending the mine’s strip waste rock mining and support additional infrastructure development, part of the second phase of the South Wall Pushback Project.
That work will allow mining to progress into a new area of the ore body and give it access to almost one million tonnes of refined copper between 2026 and 2032, extending the mine’s lifespan.
The six-year investment program began in 2020. The first phase of the South Wall Pushback, which was completed in 2021, extended production from 2019 to 2026.
A second investment, this one for $108 million, was focused on underground development to enable early orebody access and undertake orebody characterization studies for underground mining.
The project, announced last July with Rio Tinto Kennecott’s BEV test work involving Sandvik, entails a feasibility study that will focus on gathering critical geological, geotechnical and hydrogeological data to inform Rio Tinto’s assessment of underground development options and is expected to be completed in 2024.
“Existing infrastructure from previous underground projects will be extended to access the North Rim Skarn orebody, allowing for the development of crosscuts and further drilling of the resource. The project includes approximately 15,000 feet (4,500 meters) of lateral development, 1,000 feet (300 meters) of vertical development and associated support infrastructure,” the company said.
It goes without saying that Rio Tinto Kennecott is also dedicated to the future energy transition as well as the ever-growing need for copper that is produced domestically.
The miner said the U.S. was the fourth largest copper-producing nation in 2019, after Chile, Peru, and China. However, analysts estimate global copper demand from wind, solar, EVs and battery applications will increase by 600%-900% by 2030 to as much as 8.7 million tons (per the Goldman Sachs Commodities Research of April 2021).
Given that a total of nine products are currently recovered from the ore extracted at Kennecott, Rio Tinto is also seizing the market to recover tellurium, a critical mineral used in solar panels, from copper refining.
Announced last March, the $2.9 million project will have the capacity to produce about 20 tonnes of tellurium each year.
Also, last year, the mine’s staff began working alongside researchers from nearby Brigham Young University to develop innovative and sustainable solutions to improve reclamation at the Bingham Canyon mine.
BYU Associate Professor of Plant and Wildlife Sciences Matt Madsen said at the time: “This partnership is helping Rio Tinto Kennecott to continue improving the quality of its reclamation efforts and give our students the opportunity to learn skills that will benefit them in their future employment. The restoration we are doing in these areas can benefit Utah’s land and community by bringing back native vegetation, improving the site for wildlife habitat, air quality and the viewshed here in Utah.”
All told, Rio Tinto Kennecott’s commitment to its own future isn’t the end of the story; the operator contributes $1.6 billion every year to Utah’s economy. Not bad for a mining operation that was never expected to get off the ground, let alone become a top producer across the globe.
In 2022, Rio Tinto Kennecott is additionally expanding its efforts to give back to nearby communities. On average, it donates $2.2 million annually to those needing it most.
The members of Rio Tinto Kennecott’s Communities and Social Performance team is helping to build meaningful partnerships in Salt Lake County and the state of Utah.
“Rio Tinto Kennecott’s operation succeeds when all segments of the local communities, environment, and business community are successful. For this reason, Rio Tinto Kennecott makes strategic investments in communities, the environment, and cultural places. These investments lay a foundation for long-term collaboration. Strategic, outcomes-focused partnerships are prioritized towards supporting communities to achieve their goals and aspirations and achieve positive change,” it said.
Rio Tinto Kennecott also recently teamed up with the American Heart Association; the partnership will focus on improving health outcomes in Salt Lake County and the Navajo Nation.
In the end, it truly isn’t about the commodity being mined, the efficiency with which it is extracted, or even how much of it is being produced per year. It begins and ends with the people, just as it did more than 100 years ago. Along the way, Kennecott also certainly did teach many others how to mine.
“Kennecott has a rich heritage and has been a leader in the copper industry for 118 years, contributing billions to our state’s economy. We’re part of a close-knit community and many of our employees, family and friends have worked at Kennecott for decades. There is so much to be proud of as we look back, but there’s even more as we look ahead,” Poirier said.
Kennecott’s Safety Record
Rio Tinto Kennecott has earned several safety honors for its work. In 2021 alone, it was recognized several times by the Utah Mining Association and the Utah Safety Council for its safety and performance records during 2020.
The Utah Mining Association awards were presented to the Bingham Canyon Mine and the Copperton Concentrator based on their overall safety performance for 2020, zero fatalities during the year, and the reportable injuries frequency rate for each operation.