Efficient and reliable mine operations rely on carefully specified automated valves and control equipment.
By Steve Brewer and Mark Nymeyer, Emerson
Mining processes have always been brutal on control equipment. Abrasive and corrosive slurries are present throughout the facility, and many of the ore extraction steps involve corrosive chemicals. Recent initiatives to recover and reuse water from tailings have only compounded the problem because reduced water content creates even more aggressive slurries, eroding pipes, pumps, and valves.
This two-article series focuses on the more difficult operations found in most mines. It identifies the challenges associated with each of six main processing steps and offers suggestions to help specify the best automated valves, regulators, and relief valves for the more demanding applications. These first four processing steps will be covered in this article: crushing/grinding/ball mills; digestion/autoclaves; flotation/thickening; and leaching/solvent extraction.
The final two steps, tailings disposal and water management/chemical makeup, will be covered in the second article, along with additional sections covering actuators, and a use case.
Crushing/grinding/ball mills
These operations are used in virtually all mines, regardless of the ore being processed. To isolate and extract the desired mineral from the rest of the ore, the material must first be crushed and eventually grinded and even pulverized (Figure 1). Each step of these operations grinds the material into ever finer particles that are more efficiently processed in the later steps.
Material conveyors typically transfer the material from one grinding step to the next. In some ore extraction processes, the ore is ground so fine that the powder can be blown through pneumatic systems.
Two very critical components of any grinding/milling operation are water addition and the mill lube oil system. Water is fed into some mills to keep the finer particles in suspension, and to help keep the downstream screens clean. Lubrication is crucial for any large piece of equipment, particularly the rotating mills and grinders common in this area of the process.
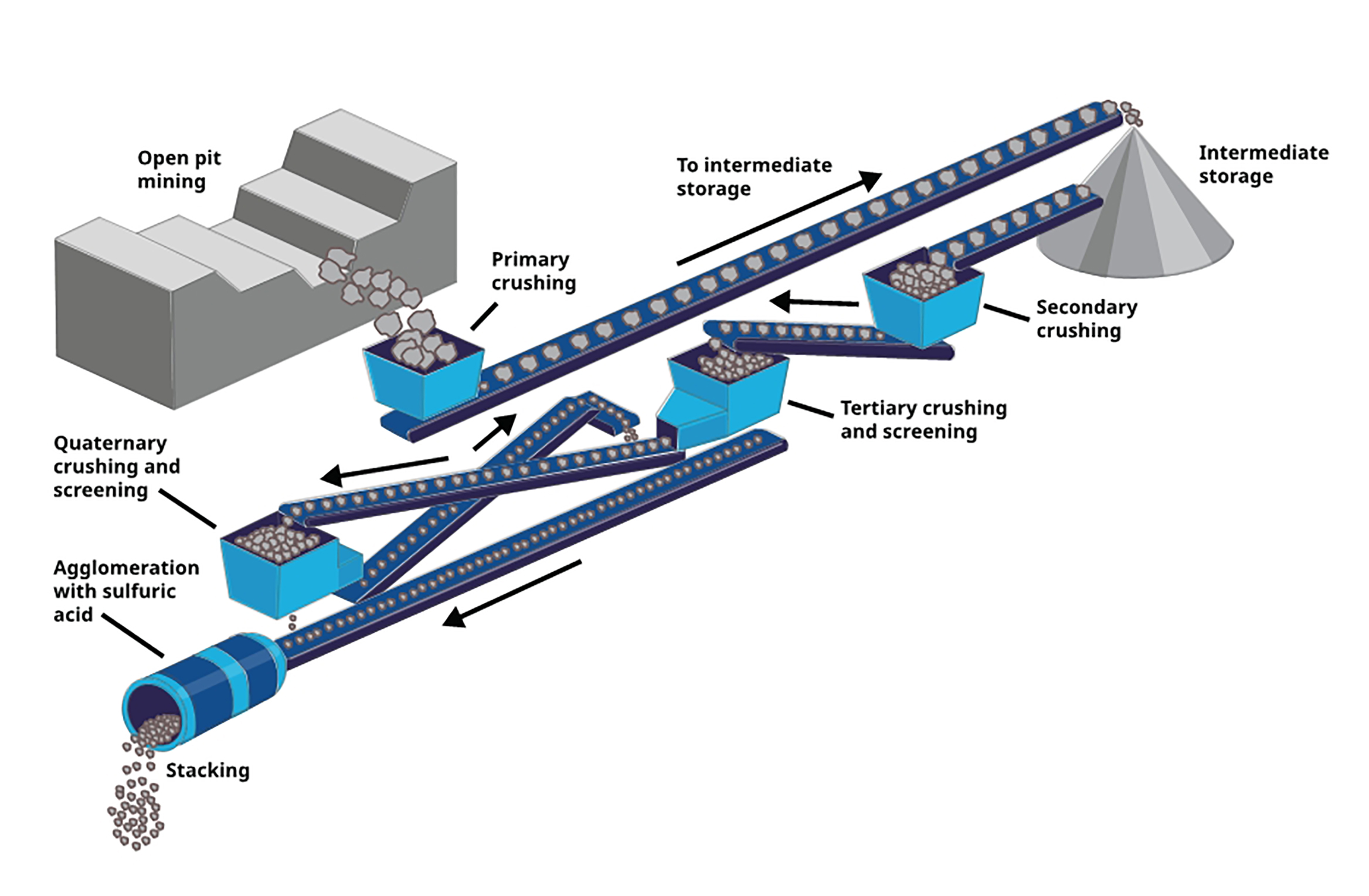
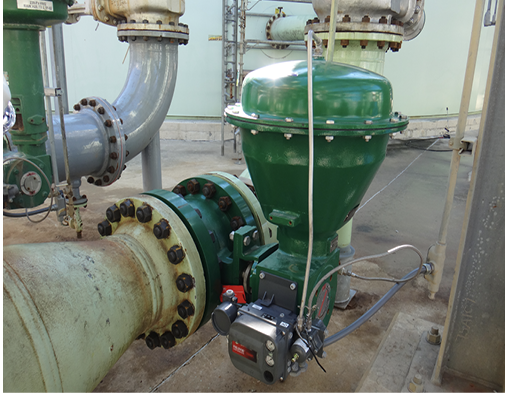
Water fed to the mills and screens is often recycled, so it tends to carry suspended solids and can create scale. There can also be significant pressure drops, which can create cavitation conditions. Large bore, v-ball type valves, such as Emerson’s Fisher Vee-Ball V150 and V300 Rotary Control Valves (Figure 2), are a good option for this service. 316 stainless steel bodies with chrome carbide-coated balls and Alloy 6 seals and retainers provide long service life, despite the conditions.
Sometimes cavitation can be an issue due to high pressure drop. In that case, anti-cavitation accessories, like Emerson’s Fisher Cavitrol Hex Trim, can be added. It has larger ports than most anti-cavitation trims and has been specially designed to work with the Fisher V-ball valve series.
Grinding/milling equipment tends to be enormous, subjecting the bearings and motors to very high stress and vibration levels. The lube oil systems make operation possible, and failure of this system will cause catastrophic damage, requiring months to repair. Because the lube oil system is so critical, it must be carefully designed using redundant pumps and reliable pressure regulators (Figure 3). Most plants further protect the equipment with a strong layer of interlocks.
Many lube oil circuits will utilize backpressure regulators – like the Fisher MR98, MR108, LR128, and 63EG – to maintain a constant pressure on the lube oil header. Lower pressure lubrication needs may require a pressure reducing regulator, like the MR95, MR105, LR125, or 1098. The proper regulator will depend on the pressure settings and flow requirements.
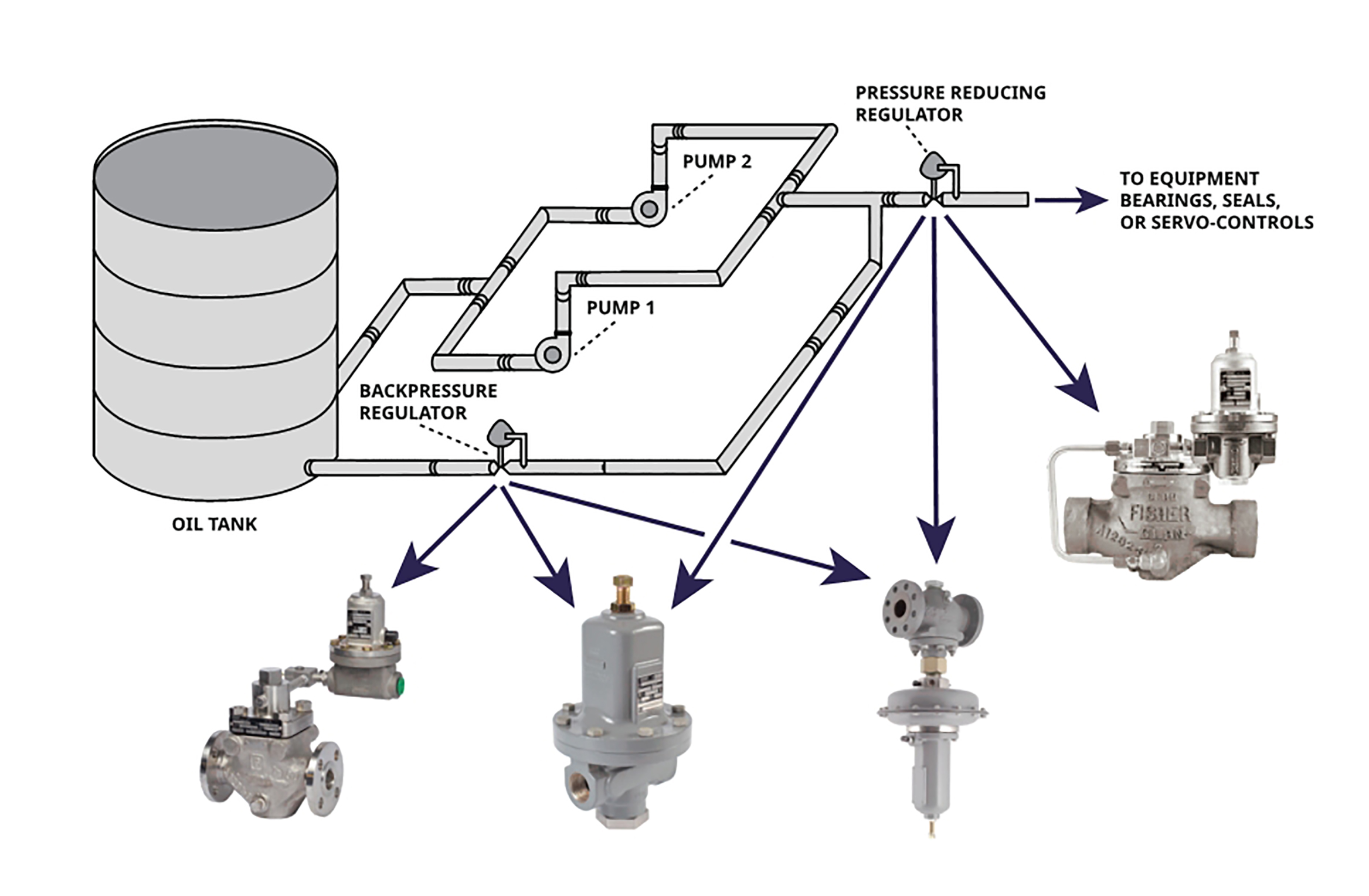
Digestion/Autoclaves
Some minerals require further processing at high temperatures and/or pressures to drive specific reactions that make extraction possible. For example, one of the first steps in the alumina process is reacting the crushed and washed ore with caustic in a digester at high temperature and pressure. This step dissolves the aluminum into a sodium aluminate solution so that the remaining ore residue can be filtered and discarded.
Alumina digester and flash tank pressure relief are particularly challenging applications. Materials tend to scale and stick to the internals of the vessel, either plugging lines or rendering them inoperable. Rupture discs can be used instead, but if these blow, the entire vessel must be fully depressurized before the disc can be replaced. During this whole time, the process is being vented, resulting in significant material loss.
A better option for this application is an Anderson Greenwood 500 series pilot operated relief valve with a high-pressure steam purge (Figure 4). The high-pressure steam purge is introduced below the relief valve to keep scale and mineral from coating and plugging the relief valve inlet. Figure 4. This redundant pilot Anderson Greenwood 500 Series relief valve from Emerson is installed on an alumina digester. The steam purged installation reduces downtime and saves significant costs over rupture disk arrangements.
When called into service, this fully-ported relief valve can quickly vent the vessel to relieve pressure and then close securely to contain the process and minimize product loss. It can also modulate, opening just enough to relieve the pressure and minimize emissions.
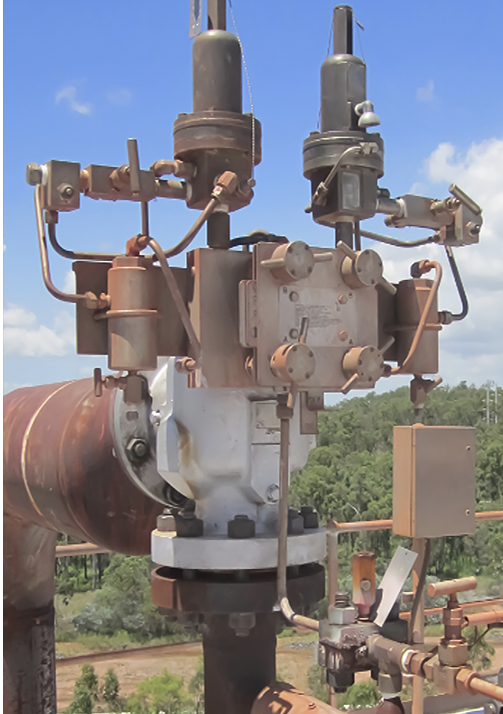
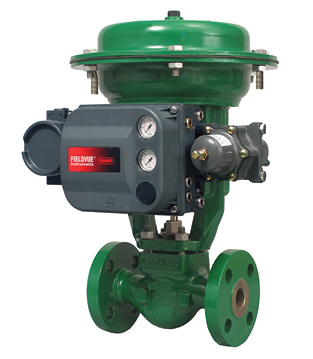
Floatation/Thickening
Most ore extraction processes involve floatation and thickening. In the floatation process, the pulverized ore is mixed with various chemicals and aerated in a large vessel. The rising bubbles from the bottom separate the material into a lighter froth that floats on top and a heavier material that sinks to the bottom. Sometimes the mineral of choice floats to the top and is skimmed off for further recovery. In other ore processes, the target material sinks to the bottom and is removed.
The floatation process requires the addition of specific chemicals, air, and sometimes oxygen and/or brine. Brine and oxygen valves require special materials of construction and must be specified carefully. A good option to regulate oxygen feeds is the Fisher GX (Figure 5) and Fisher easy-e™ EZ Control Valve series from Emerson with Monel alloy body and internals. The material of construction for the brine depends on its specific
For this service, a Baumann valve with Duplex, Ferralium, Super Duplex, or Avesta may be required to avoid corrosion and provide reliable, long-term service.
Both the top and bottom exit streams of the floatation tank are usually passed through a thickener to recover water for other ore recovery processes. The thickener receives the slurry and typically adds some type of flocculant, which makes the solids aggregate and settle to the bottom. The relatively clean water rises to the top and overflows into a channel that carries the water away for further processing. As the thick sludge builds on the bottom, it is removed for further processing. If the bottom sludge is a waste material, it is usually transferred to the tailings header for disposal.
The key valve applications around the floatation and thickening feeds vary by process and feed, but they typically utilize a number of low-pressure valves to divert feeds, underflow, and overflow slurry streams. In these applications, zero leakage, high-performing knife gate valves are required, such as the Clarkson KGA and KGD (Figure 6). The valves are full- ported and have replaceable sleeves to extend service life.
Either valve can be actuated with pneumatic or electric actuators as required by the plant, and both offer reliable, leak-free operation in low-pressure slurry applications.
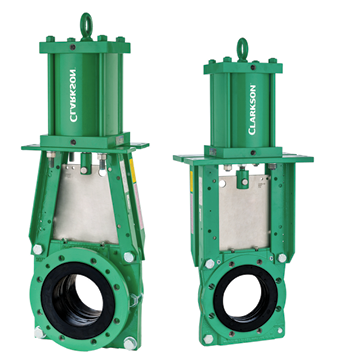

Leaching/Solvent extraction
A common unit operation in many mine processing areas involves leaching and solvent extraction. The refined and pulverized ore is stacked in piles and a solvent is poured over it to dissolve the target mineral into solution. The resulting leachate is processed in various ways to remove and condense the mineral of choice and recover the solvent for re-use.
The solvent is typically caustic or acidic and may include cyanide solutions in some ore recovery applications. These solvents are often very corrosive and difficult to handle.
The best valves for these applications will be those with protective linings that prevent direct contact with corrosive process media. Neotecha NeoSeal butterfly valves feature a PTFE-lined seat and disc that provide superior chemical resistance to extend service life (Figure 7).
Key takeaways
The best control equipment choices will vary from mine to mine and process to process. However, there are common applications across nearly every mine that can be effectively handled with the right choice of actuated valves, regulators, and relief valves. The major process challenges include:
- Grinding/Crushing/Milling: Water feeds to this equipment often contains particles, which can create scaling and erosion. Full-ported Fisher V-ball valves with stainless bodies and hardened trim can provide excellent service. If cavitation is an issue, the Cavitrol Hex Trim can be added to these models. Grinders and mills are usually large, expensive, and involve high horsepower motors with massive seals and bearings. The lubrication system for this equipment is critical for reliable operation and should employ a range of high-performing regulators – such as Fisher LR125/128, MR95/98, and MR108 – to ensure continuous operation.
- Digester/Autoclaves: These vessels operate under elevated pressure and temperature, and they are prone to material buildup and plugging in the overhead lines. Pressure relief devices, such as the Anderson Greenwood 500 series with steam purges on the inlet lines, will provide reliable, high-capacity relief and immediately seal once the pressure has been relieved.
- Floatation/Thickening: Brine and oxygen feeds to the floatation cells must be carefully specified to be compatible with their service. The user would be wise to consult their Emerson control valve rep to determine the best valve and material of construction for a particular flow application. Most of the erosive slurry flows around these areas are controlled with low pressure knife gate valves. Full-ported, reversible and serviceable knife gate valves – such as the Clarkson KGA and KGD – provide reliable, long-term service and zero leakage shut-off, despite the difficult application.
- Leaching/Solvent Extraction: The valves around these process areas are often subjected to very corrosive process streams, with varying line sizes. For this application, Neotecha NeoSeal lined butterfly valves work well as their lined disc and seat are impervious to the corrosive process fluids, and the body sizes are available from 1½ – 36 inches.
Mining processes offer a diverse set of challenges for automated valves and controls. Proper equipment selection requires a full understanding of the difficulties associated with each unit operation, as well as a knowledge of the numerous equipment options available to satisfy those needs.
Emerson has extensive experience in a broad range of mining applications and a proven track record of successful installations in many mines worldwide. It also offers a broad selection of control solutions, and the expertise to help mine operators select the right equipment to meet all requirements.
* This is part one in a two-part series.
About the Authors: Mark Nymeyer is the hybrid industry manager on the global industry sales team at Emerson for their flow controls products. In his 13 years at Emerson, he also served as the product marketing manager for their Fisher rotary valve and actuator product lines. Nymeyer works at the Emerson Innovation Center in Marshalltown, Iowa. He holds a BS degree in marketing from the University of Iowa and is a Certified Functional Safety Professional.
Steve Brewer is a business development manager at Emerson for their isolation valve group, covering the mining industry in North America. With 23 years of experience at Emerson, he has provided sales leadership in regional and international roles. Brewer holds an MBA degree from The University of Phoenix in Reno, Nevada.